Artikel
Verktyg och metoder för avvikelsehantering
-
Redaktion
-
- Ärendehantering
- 9 min läsning
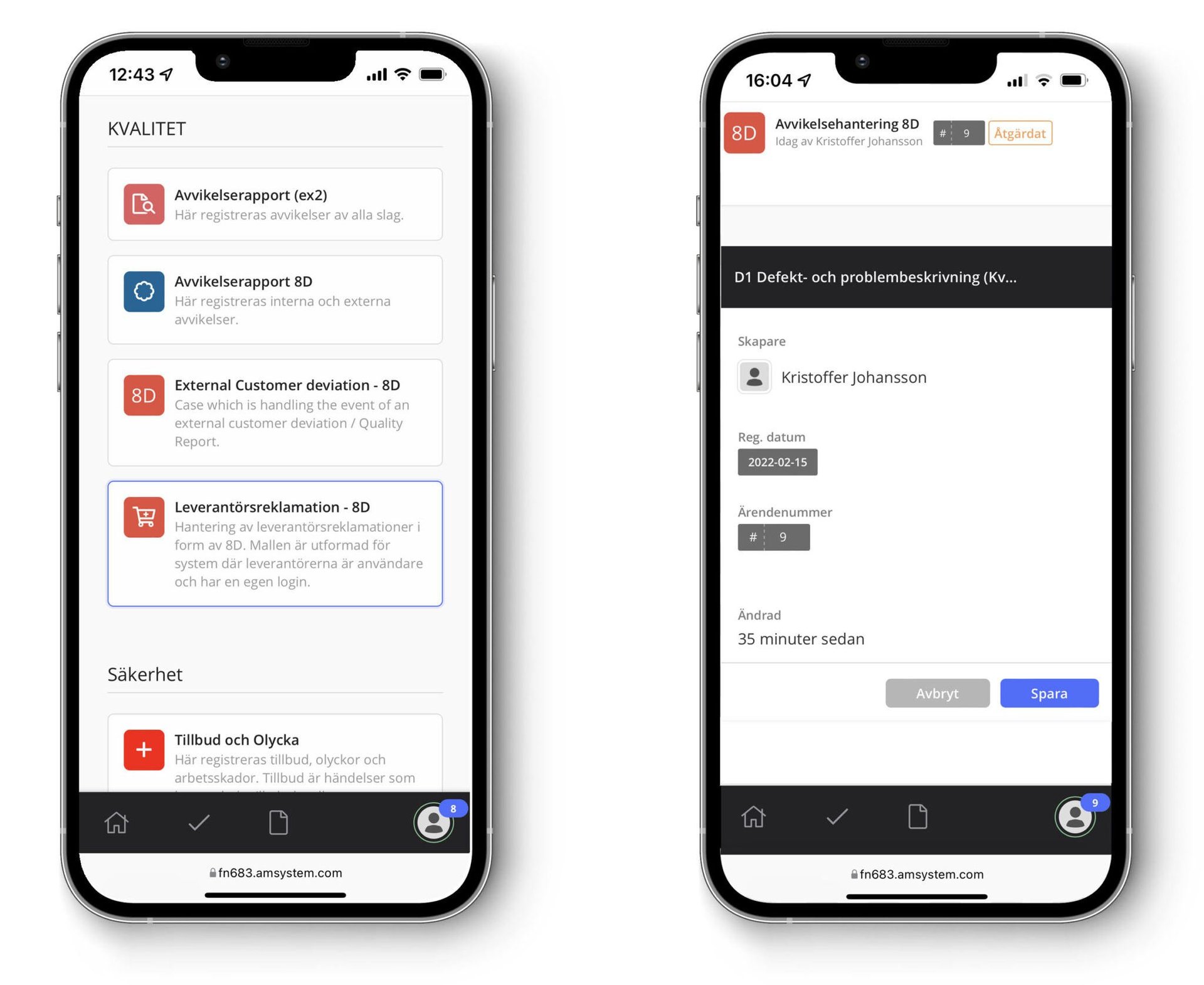
Att arbeta strukturerat med avvikelsehantering kräver rätt metoder och verktyg. Dessa metoder hjälper till att skapa tydlighet i processen och säkerställer att avvikelser hanteras på ett sätt som både löser problem och förebygger framtida avvikelser.
Avvikelsehantering inom den tillverkande industrin är en avgörande process för att säkerställa produktkvalitet, minska driftsstörningar och förbättra produktionsflöden. Processen sträcker sig från att identifiera och rapportera avvikelser till att genomföra rotorsaksanalyser, implementera åtgärder och validera resultaten. Detta kräver ofta samarbete mellan företagets olika funktioner, såsom produktion, processtekniker, kvalitetsavdelning, underhåll och ibland även leverantörer och kunder.
Nedan artikel beskriver olika verktyg och metoder för avvikelsehantering.
Tips! Vill du istället lära dig mer om avvikelser som nyckeln till lärande och förbättring, kan vi rekommendera denna artikel >
Verktyg
Det finns olika verktyg för avvikelsehantering som vart och ett fyller en funktion i den processen. Verktygen används ofta och med fördel i en logisk ordning för att säkerställa en systematisk och effektiv problemlösningsprocess. Nedan beskrivs dessa verktyg, deras syfte och hur de hänger ihop i processen, från identifieringen av problemet till implementering av långsiktiga åtgärder.
(P)FMEA
FMEA är ett vanligt förekommande verktyg som används för att bedöma potentiella fel och deras konsekvenser, både för produkter och processer. Verktyget hjälper till att rangordna risker genom att bedöma felets allvarlighetsgrad, sannolikhet och upptäckbarhet, vilket beroende på kravstandard leder till ett så kallat Risk Priority Number (RPN) eller Action Priority (AP). Att tidigt in avvikelsehanteringen förstå hur processens krav hanterades och riskbedömdes är viktigt, eftersom det arbetssättet potentiellt ledde fram till avvikelsen.
Fiskbensdiagram (Ishikawadiagram)
Fiskbensdiagram är ett visuellt verktyg som används för att strukturera möjliga orsaker till ett problem i kategorier. Det liknar ett skelett av en fisk, där huvudproblemet utgör “fiskens huvud” och kategorier som “Människor”, “Maskiner”, “Metoder”, “Material”, “Miljö” och “Mätning” utgör “fiskens ben”. Varje kategori fylls med möjliga orsaker, vilket ger en detaljerad översikt över möjliga felkällor.
Fault Tree Analysis (FTA)
FTA är ett strukturerat och visuellt verktyg för att analysera potentiella fel i komplexa system. Det används för att identifiera kombinationer av händelser som kan leda till ett kritiskt systemfel. FTA skapar en logisk karta i form av ett “felträd” där olika felorsaker bryts ner i delhändelser som bidrar till huvudproblemet.
5 Varför (5Whys)
5 Varför är ett enkelt men kraftfullt verktyg för rotorsaksanalys. Det används vanligtvis i början av en avvikelsehantering, eller mest effektivt för varje misstänkt orsak från Ishikawadiagrammet, för att snabbt identifiera grundorsaken till ett problem. Genom att upprepade gånger fråga “Varför?” om ett fel, kommer man djupare in i problemet tills den verkliga orsaken avslöjas.
Metoder
Det finns såklart många olika sätt att lösa avvikelser och olika metoder för det. För att nämna några som man generellt hittar för det så är PDCA (Plan-Do-Check-Act), 8D-metoden (Eight Disciplines Problem Solving), CAPA (Corrective and Preventive Action), Six Sigma DMAIC (Define, Measure, Analyze, Improve, Control) några. Du är säkert mer eller mindre bekant med alla eller några av dem.
Oavsett benämning är det övergripande syftet i stort sett detsamma; att identifiera en avvikelse, förstå dess orsak, implementera åtgärder och att validera att åtgärderna är effektiva innan ärendet stängs.
Beroende på krav och komplexitet finns det möjlighet att anpassa den egna metoden till sin egen verksamhet. Inget företag vinner på att överarbeta sina metoder, samtidigt som alla företag behöver bedöma och implementera en tillräcklig metod som inte bara möter krav, utan också maximerar värdet i arbetet.
8D-metoden
En 8D-metodik talar för sig själv. Det handlar om 8 definierade steg för att strukturerat maximera värdet av varje identifierad avvikelse. Varje företag kan anpassa denna metod till de steg och med de verktyg som är tillräckliga för den egna verksamheten, och kanske gradvis förstärka arbetet med fler och fler steg och bättre utnyttjande av verktygen. Vi på AM System tänker ge det ett försök att förklara de olika delarna och dess syfte, utifrån vårt perspektiv. Här tänker vi att du som läser bör vara medveten om att det kan skilja sig lite beroende på kundkrav och så vidare vad som löses & definieras i vilket steg.
Vill du läsa mer om hur du kan jobba med 8D i AM System?
D0/D1- Skapa teamet och beskriv problemet.
Ofta finns olika roller som inkluderas fastställt i företagets rutiner, så grunden bör hittas där. Utifrån det preciseras personerna som ska vara medansvariga i uppgiften, liksom vem som driver ärendet.
Problemet beskrivs såklart initialt med relevant produkt & processdata. Alltså artikelnummer, namn, batchnummer, datum och kanske skift eller klockslag. Allt som spårar tillfället till en specifik situation.
I grunden fortsätter man vanligast genom att ställa sig frågorna;
- Vad - Vad hände när avvikelsen upptäcktes?
- Varför - Varför är det en avvikelse?
- Vem - Vem upptäckte avvikelsen?
- Vart - Vart upptäcktes avvikelsen?
- När - När upptäcktes avvikelsen?
- Hur - Hur upptäcktes avvikelsen?
En klar problembeskrivning är avgörande för att rikta analysen korrekt, så skapa en enkel och tydlig struktur för att effektivt samla all relevant data i början. Underlätta för fokus där det händer, då det händer.
D2 - Liknande produkter & processer
För att inför D3 ha en så heltäckande riskbild som möjligt kan det vara intressant att direkt göra en första analys kring om felet kan inträffa på liknande produkter och liknande processer och vart produkter med risk för liknande fel kan vara. Det kan handla om det egna lagret, på plats hos kund, eller påväg till kund.
D3 - Initial analys
Med syftet att få en första förståelse för avvikelsens art och ursprung är det vanligt att i detta steg förstå vart felet skulle ha identifierats. Det kan exempelvis vara;
- I produktionsprocessen och en specifikt operation
- Redan hos leverantören
- På slutprodukten
- Innan leverans (internt/externt)
Kan man redan här ha en uppfattning om varför felet inte upptäckts på det sätt processen hade tänkt finns direkt lärdomar att dra från det.
D4 - Kortsiktiga / akuta åtgärder
Kortsiktiga akuta åtgärder vidtas för att snabbt få en uppfattning om felets spridning, bekräfta vilka volymer som är OK, liksom för att sätta in tydliga och robusta kontroller som under utredningens gång säkerställer att ett upprepat fel inte slinker igenom. Dessa åtgärder ska vara på plats och dokumenterade oftast inom 24h.
För dessa åtgärder är det viktigt att flera funktioner på företaget enkelt kan samarbeta för att lokalisera misstänkt material, ta fram en tydlig instruktion för kontrollen, kontrollera de volymer som misstänkts och se till att införa en extra kontroll ifall produktionen/verksamheten behöver fortgå.
Aktiviteter som skapar värde i detta steg är enkel kommunikation mellan interna och kanske externa funktioner, tydlighet och kompetens för att kunna skapa och följa instruktioner, hantering av misstänkt eller felaktigt material och att snabbt kunna bekräfta vad som är ok eller inte. Här kan uttryck som positiv brytpunkt nämnas. Det kan vara ett datum, tid, batchnummer eller förslagsvis ett följesedelsnummer om det levereras externt.
D5 - Rotorsaksanalys
Rotorsaksanalysen syftar till att på ett så effektivt sätt som möjligt kunna få fram den eller de verkliga orsakerna till att problemet både uppkom och inte detekterades. I detta steg sker arbetet med fördel tvärfunktionellt eftersom en process ofta planeras, utförs och följs upp av många olika funktioner. Det kan handla om process- och produktionsteknik, arbetsledning, underhållstekniker, operatörer, kvalitetstekniker osv.
Med data från riskbedömningar (FMEA) kan gruppen snabbt förstå varför processen styrs som den gör och hur. Risker har blivit processen styrning och operatörernas instruktioner, vilka ska ha följts av funktioner med rätt träning osv.
I rotorsaksanalysen kan det vara värdefullt att strukturera arbetet genom att använda verktygen som vi tidigare beskrivit. Ett av de mest använda verktygen för att identifiera potentiella orsaker till en avvikelse är Ishikawa-diagrammet, även känt som fiskbensdiagram. Genom att systematiskt kartlägga möjliga felkällor i kategorier hjälper det teamet att visualisera komplexa orsaks-samband.
Mer om Ishikawa-diagram (Fiskbensdiagram)
Arbetet med Ishikawa kräver att teamet är öppet och lyhört för olika perspektiv. Varje funktion eller avdelning bidrar genom att föreslå möjliga orsaker som sedan diskuteras och utvärderas. En viktig del av processen är att försöka motbevisa de föreslagna orsakerna genom att använda data, utfall från tidigare analyser och erfarenheter. Orsaker som inte kan motbevisas blir föremål för djupare undersökningar genom ytterligare datainsamling, experiment eller testning.
En intressant aspekt av Ishikawa-diagram är dess breda tillämpningsområde. Även om det är särskilt populärt inom tillverkande industri, används det också inom andra branscher för att förbättra processer, minska ledtider och höja kundnöjdhet. Dess enkelhet och visuella struktur gör det till ett av de mest användbara verktygen för att identifiera både direkta och underliggande orsaker till problem.
I slutändan finns således en eller flera tänkta orsaker kvar. Beroende på hur komplexa processerna är eller hur säker man vill vara kan nästa steg innefatta en FTA-analys. Den innebär i korthet att teamet ifrågasätter de orsakerna som är kvar på ett sätt som identifierar hur de kvarvarande orsakerna kan samverka för att leda till det ursprungliga problemet.
Mer om FTA-analys (Fault Tree Analysis)
I en FTA-analys (Fault Tree Analysis) arbetar teamet baklänges från det definierade felet, kallat topp-händelsen, och bryter ner det i tänkbara orsaker på ett strukturerat sätt. Dessa orsaker placeras i ett hierarkiskt schema där varje nivå representerar möjliga felkällor eller kombinationer av händelser som kan ha bidragit till problemet.
Det som gör FTA unikt är användningen av logiska portar som ‘AND’ och ‘OR’ för att visa hur flera orsaker måste inträffa samtidigt eller enskilt för att utlösa huvudproblemet. Orsaker som identifierats i ett Ishikawa-diagram kan nu analyseras djupare för att förstå deras beroenden och samverkan. Till exempel kan en upptäckt från Ishikawa-diagrammet som ‘Bristande operatörsutbildning’ och ‘Felaktigt maskinunderhåll’ i FTA-analysen visas som två separata händelser som behöver inträffa samtidigt för att skapa ett specifikt fel.
Denna strukturerade nedbrytning hjälper teamet att hitta dolda fel som kan ha förbisetts i tidigare analyssteg. Det gör också att man tydligt kan se vilka faktorer som är kritiska för att förhindra att problemet uppstår igen. Genom att använda FTA som ett komplement till Ishikawa-diagrammet säkerställer man att både enskilda orsaker och kombinerade felkedjor analyseras för att eliminera de mest kritiska riskerna.
När teamet har identifierat kvarvarande möjliga orsaker från Ishikawa-diagrammet och kartlagt deras potentiella samverkan genom FTA-analysen, är nästa steg ofta att genomföra en djupare rotorsaksanalys med hjälp av 5 Varför-metoden. Detta verktyg används för att bryta ner varje kvarstående orsak till dess verkliga grundorsak genom att ställa frågan “Varför?” upprepade gånger, vanligtvis fem gånger eller fler vid behov.
Mer om 5 Varför
Även om FTA och Ishikawa-diagrammet har gett en strukturerad översikt av möjliga orsaker och deras relationer, kan vissa orsaker fortfarande vara för generella eller oklara. Genom att använda 5 Varför för varje kvarvarande orsak kan teamet gräva djupare för att förstå varför ett specifikt fel inträffade. Detta är särskilt användbart när det finns mänskliga faktorer, underhållsrutiner, eller operativa processer inblandade – områden där orsaker ofta kräver djupare analys.
Exempel:
Om en av de identifierade orsakerna från FTA-analysen är “Bristande operatörsutbildning”, kan teamet använda 5 Varför för att förstå varför detta problem uppstod:
- Varför? Operatörerna följde inte rätt procedur.
- Varför? De hade inte fått tillräcklig utbildning i den nya processen.
- Varför? Ingen utbildningsplan hade implementerats efter processförändringen.
- Varför? Ansvarsfördelningen mellan produktion och utbildningsavdelningen var otydlig.
- Varför? Inga rutiner för utbildningsuppföljning var definierade.
Koppling till tidigare verktyg:
Från Ishikawa: Bristande operatörsutbildning identifierades under kategorin “Människan”.
Från FTA: Bristande utbildning kopplades logiskt till att “Felaktigt maskinunderhåll” kan ske samtidigt, vilket leder till maskinstopp.
Med 5 Varför: Den verkliga grundorsaken upptäcktes som “Avsaknad av utbildningsuppföljning”, vilket nu kan åtgärdas genom en långsiktig lösning.
5 Varför säkerställer alltså att analysen inte stannar vid symptom utan når den verkliga rotorsaken. På så sätt blir det lättare att identifiera effektiva korrigerande och förebyggande åtgärder, vilket stärker hela avvikelsehanteringsprocessen. Om ett tydligt svar inte kan fastställas genom 5 Varför kan ytterligare data behöva samlas in eller fler analytiska verktyg användas för att nå djupare insikter.
D6 - Korrigerande åtgärder
Grunden till att planera och utföra rätt korrigerande åtgärder ligger i hur väl rotorsaksanalysen fungerat. Åtgärderna har absolut bäst effekt över tid om de fokuseras på de verkliga orsakerna till problemet. Beroende på inom vilket område orsakerna identifierats kommer såklart insatser från olika delar av verksamheten vara ansvariga för att utföra åtgärderna. Orsaksanalys och definierade åtgärder ska finnas dokumenterade i 8Dn inom 10 dagar.
Teamet skapar en tydlig åtgärdsplan i D6, där minst en åtgärd per identifierad orsak bör finnas med. Det är här vanligt att diskutera i termer av “Occurance” och “Detection”, alltså åtgärder som både förhindrar att felet kan inträffa och/eller säkerställer att det detekteras om det inträffar.
Åtgärder planeras in och utförs av respektive ansvarig funktion och vid utförandet inkluderar det både att göra den faktiska uppgiften, liksom att skapa förutsättningar och kommunicera ändringen till de funktioner det berör. Ändringar i en produktion innebär ofta uppdaterade rutiner och instruktioner för medarbetarna, vilka då behöver upplärning och träning. Till grund för de ändringarna kommer PFMEA och Styrplaner ha uppdaterats, vilket säkerställer att lärdomar från avvikelsen loggas och systematiseras, därmed med större sannolikhet tas tillvara vid utveckling av liknande processer/produkter i framtiden.
Det är värdefullt att arbetet i D6 har en enkel och tydlig struktur kring vem som gör vad och tills när, och att det enkelt kan överblickas av den som leder arbetet.
D7 - Validering av införda åtgärder
I detta steget ska det säkerställas att de införda åtgärderna fungerar som tänkt. En validering kan såklart ske på olika sätt, baserat på olika data eller input. I D4 skapades direkt extra kontroller i processen, eller i de processer, som felet identifierats i eller riskerade att finnas i. Har man haft en extra kontroll under 8D-arbetets gång, där fel fortsatt upptäckts, kan den loggen tjäna som en bra input i valideringen. Fr o m att den långsiktiga lösningen har implementerats ska inte några fel av feltypen längre hittas. Tiden processen ska köras eller vilket antal producerade artiklar i processen som behöver tillverkas varierar såklart mellan olika verksamheter. Syftet är ändå detsamma, att statistiskt säkerställa att processen är stabil och inte längre riskerar att producera felet.
Det är värdefullt att kunna ta datadrivna beslut baserat på fakta, vilket gör att loggning av data från utfallet har ett stort värde för de som ska validera åtgärderna. Likadant är det viktigt att det finns överenskomna personer/funktioner som ska göra det utifrån överenskomna deadlines. Ju mer data och visuell återkoppling, kanske i form av bilder och film, som kan samlas in som bevisning, desto säkrare kan man vara på sitt beslut, liksom påvisa framstegen i arbetet. Både för de som är deltagande nu, eller som i framtiden behöver gå tillbaka till ärendet för att förstå vissa moment.
D8 - Lessons learned, fira & stäng
Syftet med det sista steget i en 8D är att summera utfall, bekräfta att allt som var överenskommet att göras är gjort, liksom att fira den slutförda uppgiften med teamet. Det sista kan låta märkligt, samtidigt som det är viktigt att aktivt uppmuntra till positiv feedback och att få fira som grupp och individ.
Som en del av lessons learned i detta steg finns det värde i att veta om och bekräfta, att man systematiserat och inkluderat de lärdomar som företaget dragit genom det aktuella ärendet. Som exempel kan nämnas att PFMEA/Riskbedömningar är uppdaterade, instruktioner och rutiner, kompetensuppdateringar, grundläggande underlag som ritningar eller mätmetoder. Även kund- eller leverantörsrelationer har fått förändrade förutsättningar?
Summering avvikelsehantering - tänk på att
En strukturerad avvikelsehantering handlar om mer än att bara lösa problem – det är ett strukturerat sätt att skapa långsiktigt värde för både individen och företaget. Genom att samla rätt kompetens tidigt får teamet ett gemensamt fokus, vilket skapar en tydlig plan för att identifiera, analysera och åtgärda avvikelser.
Arbetet är inte bara reaktivt utan också proaktivt, då potentiella problem i liknande produkter och processer undersöks för att minimera framtida risker. Identifieras rätt grundorsaker genom effektiva verktyg som Ishikawa-diagram och 5-Varför, kan åtgärder planeras och genomföras som faktiskt gör skillnad.
För individen innebär detta ett strukturerat arbetssätt där alla får och kan bidra med sin expertis, vilket skapar en stark problemlösningskultur och möjligheter till professionell utveckling, från något som egentligen är ett problem.
För företaget leder det till hållbara förbättringar och kontinuerlig uppdatering av processer och rutiner. Det handlar inte bara om att lösa dagens problem utan också om att lära av dem för att bli bättre i framtiden.
När arbetet avslutas har både individen och företaget utvecklats – och de framgångarna tillsammans med ett starkare team och en förbättrad kvalitetskultur är väl verkligen en orsak att fira.
Avvikelsehanteringen enligt eller i linje med 8D-metoden är därför mer än en metod och angreppssätt – det är en investering i kvalitet, samarbete och framtida konkurrenskraft.
Boka demo
Upptäck ledningssystemet som faktiskt hjälper
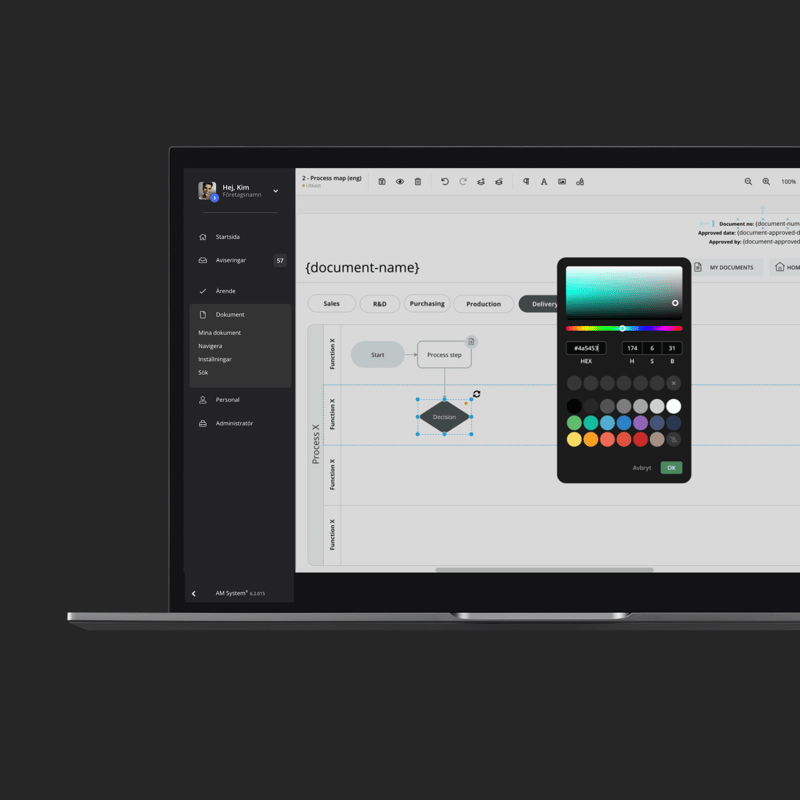