Artikel
Effektiv problemlösning med 8D-metoden: Så säkrar ni kvalitet och kundnöjdhet
-
Redaktion
-
- Ärendehantering
- 4 min läsning
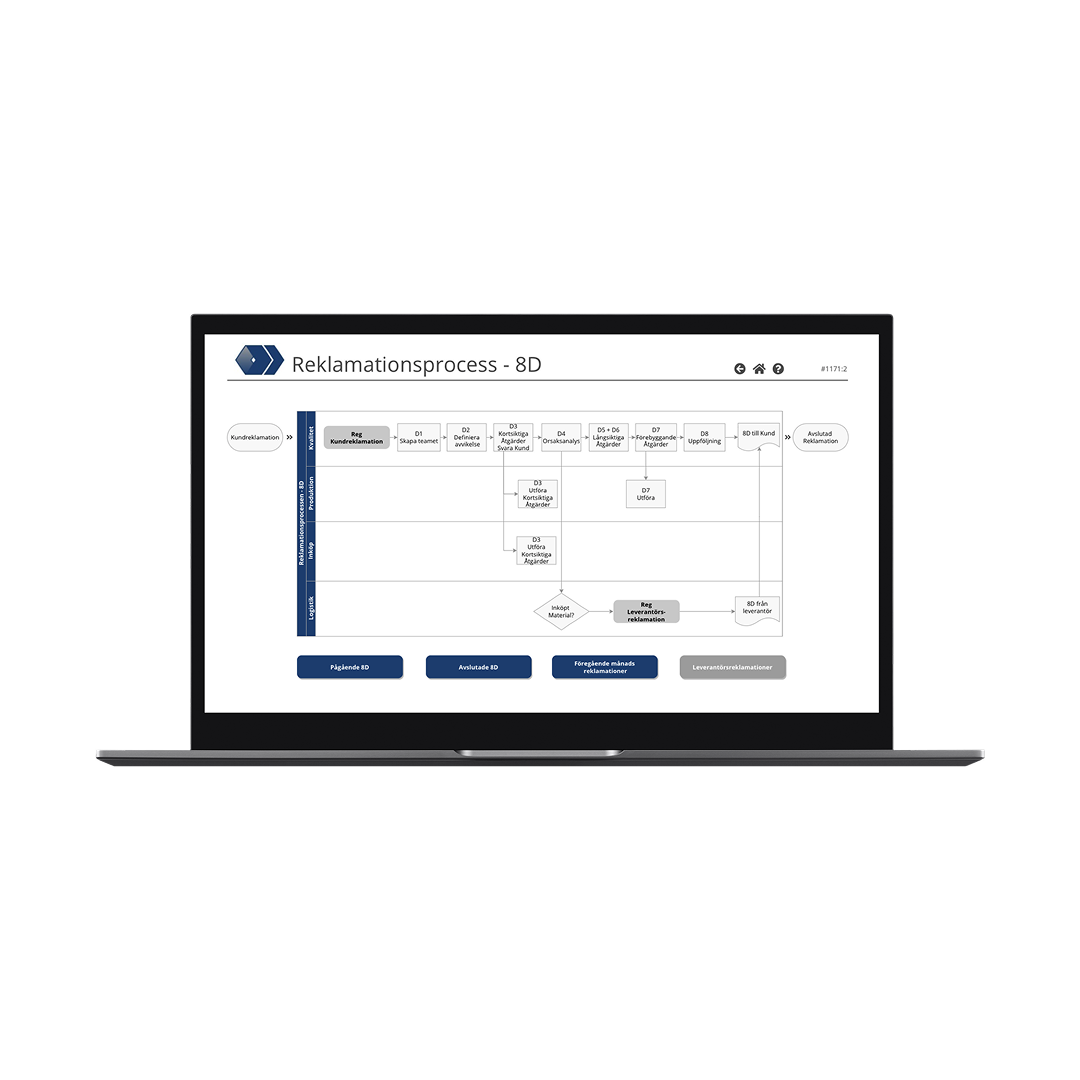
8D-metoden, eller Eight Disciplines, är en strukturerad och systematisk metod för problemlösning som utvecklades av Ford för att identifiera, analysera och eliminera problem. Metoden är särskilt värdefull för tillverkande industri där avvikelser kan få stora konsekvenser för både produktion och kundrelationer. Med hjälp av 8D-metoden kan ni inte bara lösa problem snabbare, utan också skapa en långsiktig lösning som minskar risken för att samma problem återkommer.
Genom att digitalisera och standardisera arbetet med 8D kan ni effektivisera problemlösningen och generera rapporter som tydligt beskriver vad som gick fel, varför det inträffade och hur ni planerar att åtgärda det – både på kort och lång sikt.
Så fungerar 8D-metoden
8D-metoden bygger på nio discipliner som vägleder er genom hela processen, från att definiera problemet till att säkerställa att det aldrig inträffar igen. Varje steg stärker förståelsen för grundorsakerna och skapar en struktur för att implementera hållbara lösningar.
De olika stegen i 8D-metoden:
D0-Förbereda och planera
- Identifiera problemet: Bekräfta att det verkligen finns en avvikelse som kräver strukturerad problemlösning. Dokumentera initiala detaljer som omfattning, påverkan och potentiella risker.
- Bedöm nödvändigheten av 8D: Avgör om problemet är tillräckligt komplext eller omfattande för att motivera användning av 8D-metoden.
- Samla resurser: Säkerställ att rätt verktyg, data och resurser finns tillgängliga innan processen påbörjas.
- Informera och eskalera: Kommunicera om problemet till relevanta intressenter och säkra ledningens stöd om det behövs.
D1 - Formera team
- Sätt samman ett tvärfunktionellt team som har den tekniska kompetens och erfarenhet som krävs för att förstå och lösa problemet.
- Säkerställ att teamet representerar alla relevanta avdelningar, exempelvis produktion, kvalitet, underhåll och logistik.
- Klargör roller och ansvar inom teamet för att effektivisera arbetet.
D2 - Definiera problemet
- Beskriv problemet detaljerat: Vad har hänt, Var i processen det inträffar, När det började och Hur det påverkar produktion eller produktkvalitet.
- Kvantifiera problemet (t.ex. antal defekta artiklar, påverkan på leveranser eller ekonomiska förluster).
- Skapa en tydlig problemdefinition för att säkerställa att alla inblandade förstår omfattningen.
D3 - Implementera tillfälliga åtgärder
- Vidta snabba, kortsiktiga åtgärder för att minimera påverkan både för kunden och produktion, exempelvis sortera och isolera defekta produkter eller justera processparametrar.
- Säkerställ att tillfälliga åtgärder inte påverkar andra kunder eller delar av verksamheten negativt.
- Övervaka effekten av de tillfälliga åtgärderna tills permanenta åtgärder är på plats.
D4 - Identifiera grundorsaker
- Utför en grundlig rotorsaksanalys för att identifiera den verkliga orsaken till problemet, inte bara symptomen.
- Använd verktyg som 5 varför, fiskbensdiagram (Ishikawa) eller Paretoanalys för att kartlägga möjliga orsaker.
- Verifiera grundorsaken genom att testa hypoteser och bekräfta att den verkligen är roten till problemet.
D5 - Bestäm och verifiera korrigerande åtgärder
- Identifiera möjliga åtgärder som motverkar grundorsaken på ett effektivt sätt.
- Analysera och simulera åtgärdernas genomförbarhet, kostnad och potentiella bieffekter.
- Verifiera åtgärderna i en kontrollerad miljö eller genom pilotprojekt för att säkerställa att de fungerar som avsett.
D6 - Implementera korrigerande åtgärder
- Inför de valda lösningarna i full skala i processen eller produktionen.
- Uppdatera arbetsinstruktioner, processbeskrivningar och andra relevanta dokument.
- Utbilda personal om de nya arbetssätten och säkerställ att åtgärderna blir en del av den dagliga verksamheten.
D7 - Förebygg återkommande problem
- Identifiera andra processer eller produkter där samma grundorsak kan finnas och tillämpa lärdomarna proaktivt.
- Implementera förebyggande åtgärder som t.ex. regelbunden processövervakning, förbättrad leverantörskontroll eller ökad kvalitetssäkring.
- Uppdatera ledningssystem, rutiner, instruktioner, styrplaner och riskbedömningar för att integrera åtgärderna.
D8 - Fira framgång och lärdomar
- Dokumentera hela processen, inklusive lösningar, lärdomar och förbättringar.
- Sprid informationen till hela organisationen för att bygga en kultur av lärande och förbättring.
- Fira teamets framgång för att stärka motivation och engagemang i framtida förbättringsinitiativ.
Fördelarna med 8D-metoden
Att använda 8D-metoden erbjuder en strukturerad och effektiv strategi för att hantera avvikelser och genererar flera betydande fördelar för tillverkande företag:
Färre avvikelser och reklamationer
Genom att identifiera och eliminera grundorsakerna till problem förebygger ni att samma avvikelse uppstår igen. Detta leder till en minskning av störningar, reklamationer och garantiärenden, vilket bidrar till stabilare processer och högre produktkvalitet.
Lägre kostnader
Att åtgärda problem på ett grundläggande plan innebär att ni undviker återkommande kostnader för avbrott, omarbetningar, kassationer och kundkompensationer. Effektiv problemlösning minskar också spill och optimerar resursanvändningen, vilket stärker lönsamheten.
Djupare kunskap om verksamheten
Varje avvikelse blir en möjlighet att analysera och förstå era produkter, processer och leverantörskedjor bättre. Genom att systematiskt använda verktyg som rotorsaksanalys byggs en större förståelse som kan användas för att förbättra andra delar av verksamheten.
Högre kundnöjdhet
Effektiv och snabb hantering av problem minimerar påverkan på kunderna, till exempel genom att säkerställa leveranser av rätt kvalitet och i tid. En tydlig kommunikation och långsiktiga lösningar stärker kundernas förtroende för er verksamhet och ert varumärke.
Ökad medarbetarengagemang
Den tvärfunktionella arbetsmetoden i 8D-metoden skapar engagemang och delaktighet hos medarbetarna. När problem löses på ett strukturerat sätt och framgångar delas, motiveras teamet till att bidra till fler förbättringar.
Stärkt förbättringskultur
Genom att integrera 8D-metoden i era processer bygger ni en organisation som systematiskt arbetar med förbättringar. Det stärker verksamheten som helhet och förbereder företaget för framtida utmaningar.
Bättre riskhantering
Identifieringen av grundorsaker och implementeringen av förebyggande åtgärder hjälper till att minimera risken för oväntade avvikelser och stora störningar i produktionenn
8D-metoden är inte bara en problemlösningsmodell utan också en strategi för att bygga robusta processer och långsiktigt förbättra verksamheten.
Digitala 8D-rapporter: Ett modernt arbetssätt
I dagens digitala arbetsmiljö är traditionella, pappersbaserade processer ofta ineffektiva. Med digital 8D-rapportering kan team arbeta tillsammans i realtid, vilket sparar tid och ökar precisionen. Alla inblandade får omedelbar tillgång till rapporten, och förändringar kan spåras och kommuniceras smidigt.
Med ett digitalt ledningssystem blir det dessutom enklare att följa upp och analysera data från tidigare avvikelser. Ni kan identifiera trender, förbättra processer och säkerställa att era rutiner uppfyller såväl interna krav som externa standarder.
Vill ni ta kontroll över era avvikelser och skapa en kultur av kontinuerlig förbättring? Läs mer om hur ni kan arbeta med 8D-rapporter i AM System
Boka demo
Upptäck ledningssystemet som faktiskt hjälper
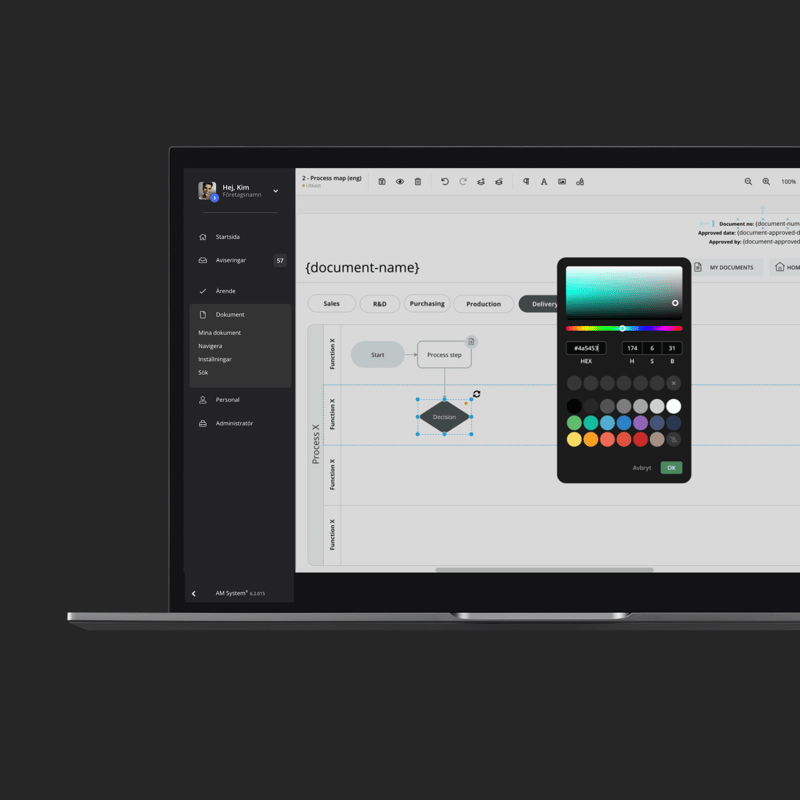