Article
Effective problem solving with the 8D method: How to ensure quality and customer satisfaction
-
Editorial team
-
- Case Management
- 4 min reading

The 8D method, or Eight Disciplines, is a structured and systematic approach to problem solving developed by Ford to identify, analyze and eliminate problems. The method is particularly valuable for the manufacturing industry where deviations can have major consequences for both production and customer relations. Using the 8D methodology, you can not only solve problems faster, but also create a long-term solution that reduces the risk of the same problem recurring.
By digitizing and standardizing your work with 8D, you can streamline problem solving and generate reports that clearly describe what went wrong, why it happened, and how you plan to fix it - both in the short and long term.
How the 8D approach works
The 8D approach is based on nine disciplines that guide you through the entire process, from defining the problem to ensuring it never happens again. Each step strengthens the understanding of root causes and creates a structure for implementing sustainable solutions.
The different steps of the 8D approach:
D0-Prepare and plan
- Identify the problem: Confirm that there is indeed a deviation that requires structured problem solving. Document initial details such as scope, impact and potential risks.
- Assess the necessity of 8D: Determine whether the problem is sufficiently complex or widespread to warrant the use of the 8D approach.
- Gather resources: Ensure that the right tools, data and resources are available before starting the process.
- Inform and escalate: Communicate the problem to relevant stakeholders and secure management support if needed.
D1 - Form teams
- Assemble a cross-functional team that has the technical skills and experience required to understand and solve the problem.
- Ensure that the team represents all relevant departments, such as production, quality, maintenance and logistics.
- Clarify roles and responsibilities within the team to streamline work.
D2 - Define the problem
- Describe the problem in detail: What has happened, Where in the process it occurs, When it started and How it affects production or product quality.
- Quantify the problem (e.g. number of defective items, impact on deliveries or financial losses).
- Create a clear problem definition to ensure that everyone involved understands the scope.
D3 - Implement temporary measures
- Take quick, short-term actions to minimize the impact on both the customer and production, such as sorting and isolating defective products or adjusting process parameters.
- Ensure that temporary measures do not negatively affect other customers or parts of the business.
- Monitor the effect of the temporary measures until permanent measures are in place.
D4 - Identify root causes
- Perform a thorough root cause analysis to identify the real cause of the problem, not just the symptoms.
- Use tools such as 5 whys, fishbone diagrams (Ishikawa) or Pareto analysis to identify possible causes.
- Verify the root cause by testing hypotheses and confirming that it is indeed the root of the problem.
D5 - Determine and verify corrective actions
- Identify possible actions that address the root cause effectively.
- Analyze and simulate the feasibility, cost and potential side effects of the actions.
- Verify the measures in a controlled environment or through pilot projects to ensure that they work as intended.
D6 - Implement corrective actions
- Implement the chosen solutions at full scale in the process or production.
- Update work instructions, process descriptions and other relevant documents.
- Train staff on the new ways of working and ensure that the measures become part of daily operations.
D7 - Prevent recurring problems
- Identify other processes or products where the same root cause may exist and apply the lessons learned proactively.
- Implement preventive measures such as regular process monitoring, improved supplier control or increased quality assurance.
- Update management systems, procedures, instructions, control plans and risk assessments to integrate the measures.
D8 - Celebrate success and lessons learned
- Document the whole process, including solutions, lessons learned and improvements.
- Disseminate the information to the whole organization to build a culture of learning and improvement.
- Celebrate the team's success to strengthen motivation and commitment to future improvement initiatives.
The benefits of the 8D approach
Using the 8D approach offers a structured and effective strategy for managing nonconformities and generates several significant benefits for manufacturing companies:
Fewer nonconformities and complaints
By identifying and eliminating the root causes of problems, you prevent the same non-conformity from occurring again. This leads to a reduction in breakdowns, complaints and warranty claims, contributing to more stable processes and higher product quality.
Lower costs
Fixing problems at a fundamental level means you avoid recurring costs for downtime, rework, scrap and customer compensation. Effective problem solving also reduces waste and optimizes resource use, boosting profitability.
Deeper knowledge of the business
Every non-conformity becomes an opportunity to better analyze and understand your products, processes and supply chains. By systematically using tools such as root cause analysis, a greater understanding is built that can be used to improve other parts of the business.
Higher customer satisfaction
Efficient and timely handling of problems minimizes the impact on customers, for example by ensuring deliveries of the right quality and on time. Clear communication and long-term solutions strengthen customers' trust in your business and brand.
Increasing employee engagement
The cross-functional approach of the 8D methodology creates employee engagement and involvement. When problems are solved in a structured way and successes are shared, the team is motivated to contribute to more improvements.
Strengthening the culture of improvement
By integrating the 8D method into your processes, you build an organization that systematically works on improvements. This strengthens the business as a whole and prepares the company for future challenges.
Better risk management
Identifying root causes and implementing preventive measures helps minimize the risk of unexpected deviations and major disruptions in production.
The 8D approach is not only a problem-solving model, but also a strategy for building robust processes and improving operations in the long term.
Digital 8D reports: a modern way of working
In today's digital work environment, traditional, paper-based processes are often inefficient. Digital 8D reporting allows teams to work together in real time, saving time and increasing accuracy. Everyone involved has immediate access to the report, and changes can be tracked and communicated smoothly.
A digital management system also makes it easier to follow up and analyze data from previous incidents. You can identify trends, improve processes and ensure that your procedures meet both internal requirements and external standards.
Do you want to take control of your non-conformities and create a culture of continuous improvement? Learn more about how you can work with 8D reports in AM System
Get a demo
Ready to make work easier - and more enjoyable?
Want to see for yourself how AM System can make a difference for you? Request a demo and discover how easy it is to create structure, efficiency, and seamless workflows in your daily operations.
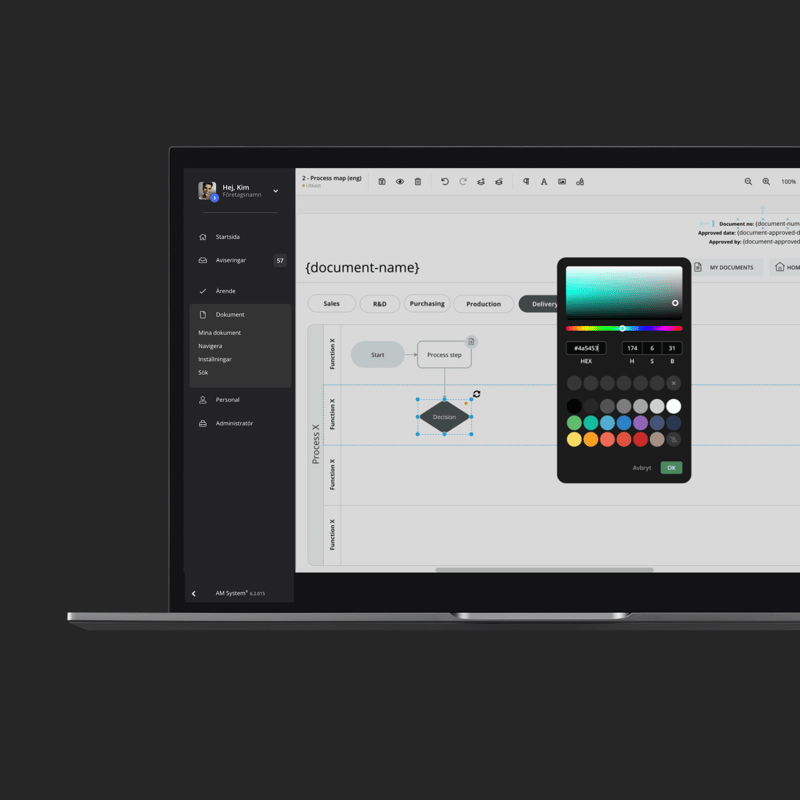