Article
The 5S-methodology: The foundation for an efficient and well-organized workplace
-
Editorial team
-
- Document Management, Quality Management System
- 2 min reading
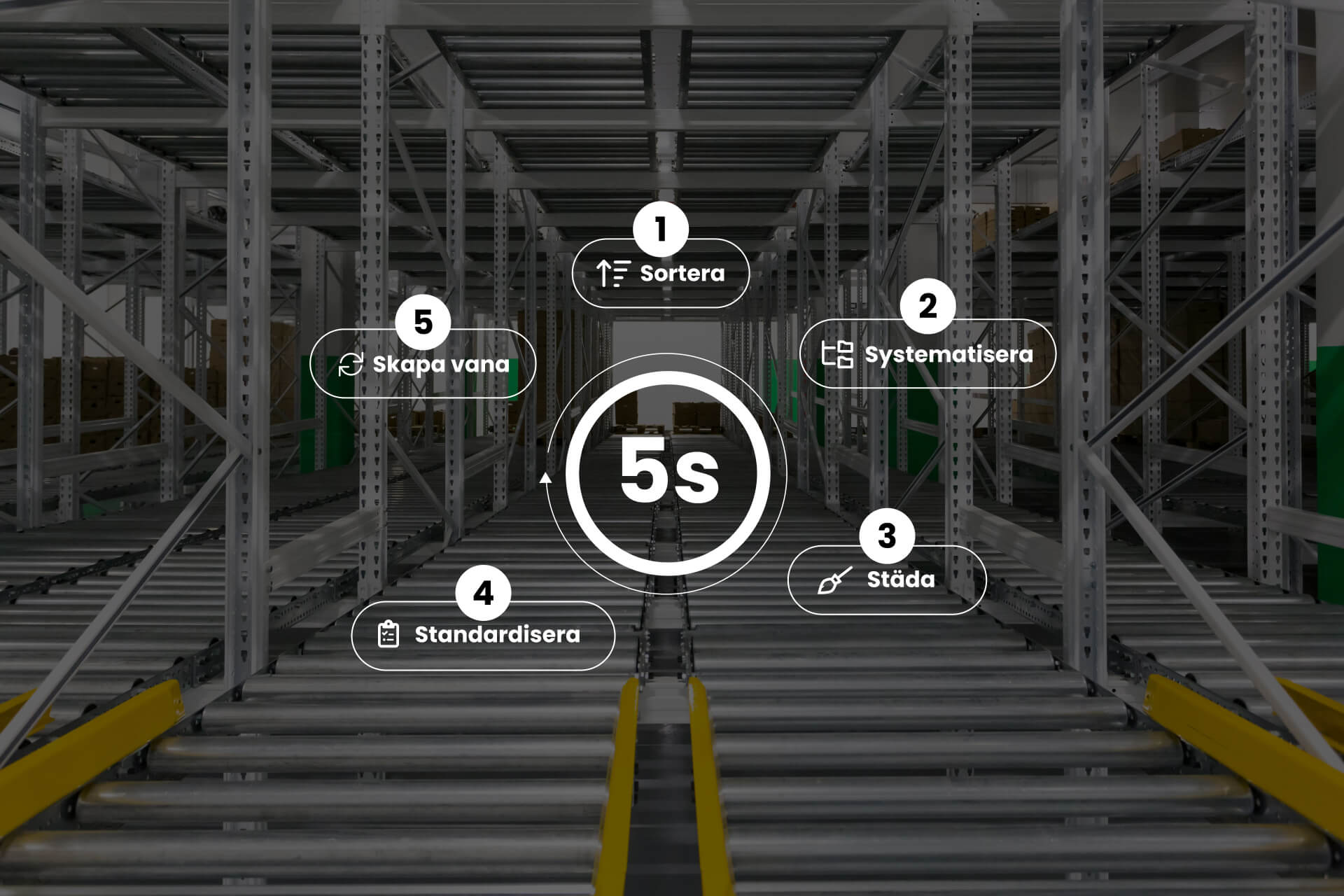
In an era where efficiency, quality and safety are critical to business success, the 5S-methodology is one of the most powerful tools for creating order and structure. Originally developed in Japan as part of the Toyota Production System, 5S has become a universal method for optimizing work environments and improving processes. It is as useful in manufacturing as it is in offices, warehouses and other workplaces.
But what makes 5S so successful, and how can you implement it to achieve sustainable results?
What is the 5S-methodology?
5S (part of lean manufacturing) is a structured approach to creating and maintaining order. The name comes from five Japanese words, all starting with the letter "S", which represent five steps to organize the workplace:
- Sort (Seiri): Go through all the items in the workplace and remove what is not needed. This frees up space, reduces distractions and creates a work environment free of unnecessary distractions.
- Systematize (Seiton): Organize the necessary items so that they are easily accessible and always in their right place. "A place for everything, and everything in its place" is the watchword here.
- Clean (Seiso): Clean the workplace regularly. This is not just about cleanliness, but about creating an environment where problems such as spills, damage or wear can be quickly identified.
- Standardize (Seiketsu): Create standards and procedures to ensure the workplace is kept organized and clean over time.
- Create habit (Shitsuke): Introduce a discipline and culture where everyone follows and upholds the 5S principles. This is the most critical step for 5S to be a long-term success.
Why is 5S relevant to today's workplace?
Although the 5S-methodology has its roots in 20th century industry, its principles are timeless and highly relevant to modern workplaces. Here are some of the main reasons:
- Efficiency: Eliminating waste and creating smooth workflows frees up time and resources for value-adding activities.
- Quality: When the workplace is organized and standardized, the risk of errors and deviations is reduced.
- Safety: A well-organized workplace is also a safer workplace, where risks of accidents and injuries are minimized.
- Engagement: When employees are involved in creating a better work environment, both satisfaction and responsibility increase.
Common challenges with 5S - and how to overcome them
Implementing 5S can be challenging, especially if there is resistance or lack of commitment. Here are some common obstacles and how you can overcome them:
- Resistance to change: involve employees early on and demonstrate the tangible benefits of 5S.
- Lack of follow up: Introduce regular inspections and audits to ensure that procedures are followed.
- Unclear objectives: set clear and measurable objectives for what 5S will achieve, such as improved safety or shorter lead times.
- Maintaining standards: Make sure there is a plan to continuously train and remind employees of the 5S principles.
Success with 5S requires commitment
The key to a successful 5S implementation lies in the commitment of the whole organization. It's not just about introducing new procedures, but about creating a culture where everyone takes responsibility for keeping the workplace organized, safe and efficient. By continuously improving and developing work according to the 5S principles, organizations can achieve long-term improvements and increased quality.
The role of digitalization in the 5S approach
Historically, the 5S-methodology has often been implemented using manual tools - paper checklists and whiteboards. While this can work, there is a risk that work becomes inefficient or procedures are forgotten.
By using a digital tool like AM System, you can take 5S to the next level.
Here are some examples of how digital tools can enhance the impact of 5S:
- Automated documentation: Digital checklists and reports allow you to monitor and analyze how well 5S is being implemented over time.
- Real-time communication: A digital management system makes it possible to share information directly with all employees, wherever they are.
- Visual instructions: A digital tool can include images, tutorials and videos showing how a workplace should look according to your 5S standard.
- Traceability: You can easily see who is responsible for different tasks and follow up on their timely completion.
- Flexibility: as many digital systems are cloud-based, you can manage and monitor 5S from a computer, tablet or smartphone.
Digitization is not about replacing the 5S approach, but about enhancing and simplifying its application.
5S is more than a method - it's an investment in your workplace and its future.
Get a demo
Ready to make work easier - and more enjoyable?
Want to see for yourself how AM System can make a difference for you? Request a demo and discover how easy it is to create structure, efficiency, and seamless workflows in your daily operations.
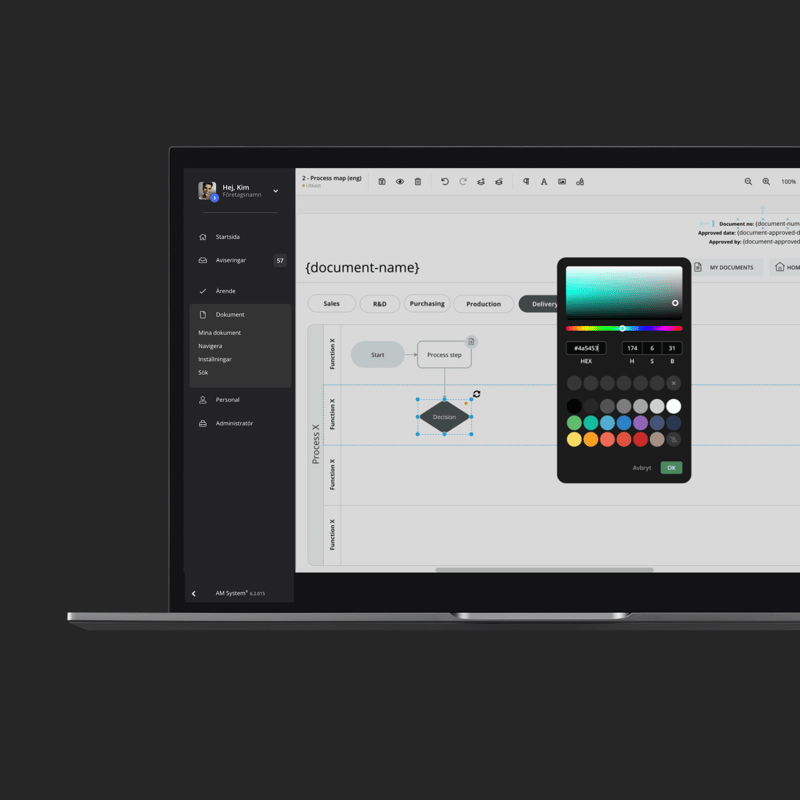