Article
What is a quality management system?
-
Editorial team
-
- Quality Management System
- 2 min reading
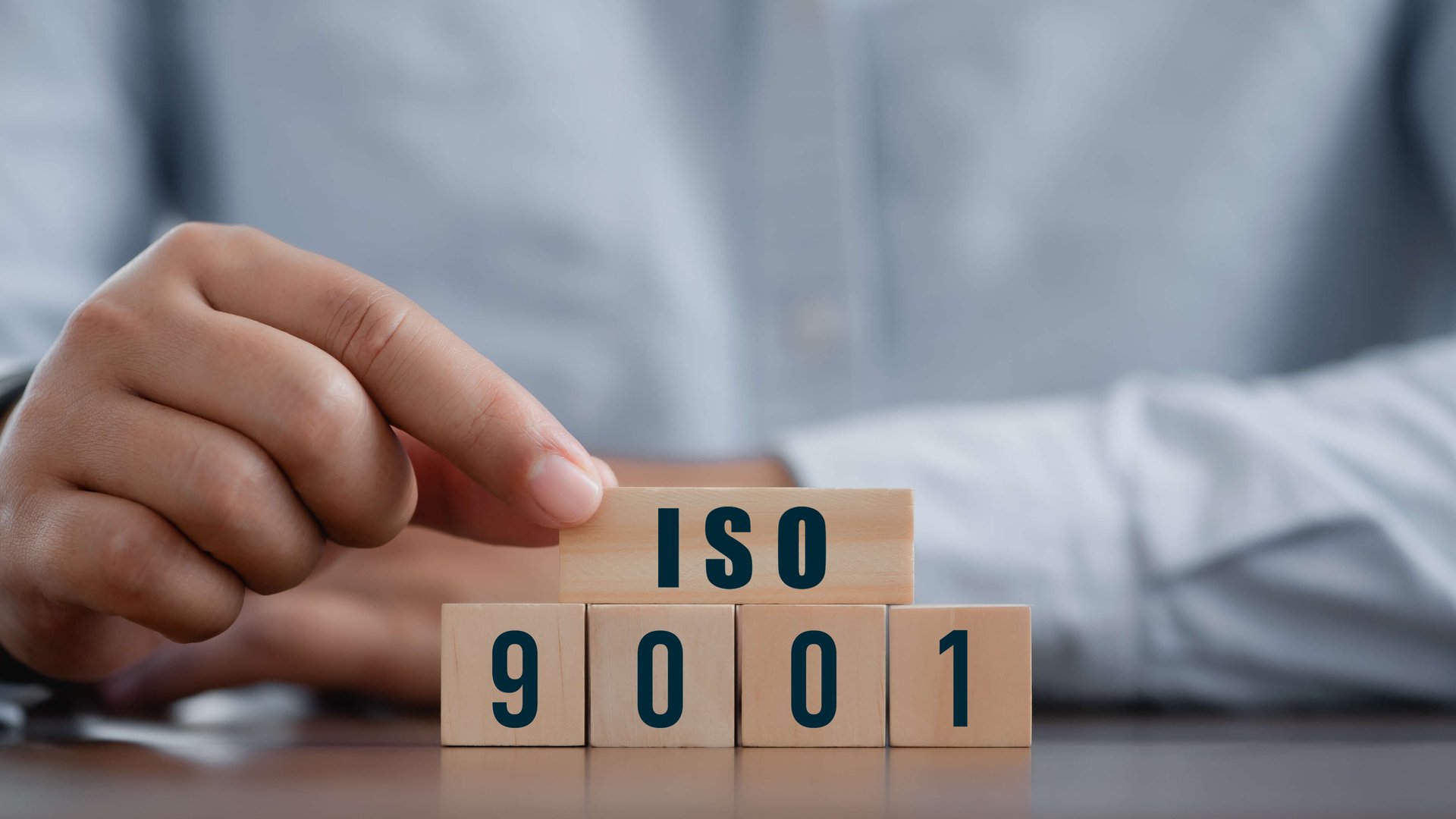
A quality management system (QMS) is a tool that helps companies structure, manage, and improve their operations. It ensures that processes, procedures, and requirements are followed consistently. By using a digital system, handling documents, cases, and workflows becomes more efficient.
A QMS is not just a collection of documents—it’s a mindset and a way of working that involves all employees and integrates throughout the organization. By clarifying roles, responsibilities, and workflows, a quality management system builds trust with customers, partners, and other stakeholders.
Benefits of a quality management system
- Increased efficiency through automated processes
- Improved collaboration and clearer responsibility distribution
- Easier compliance with legal and certification requirements
- Enhanced traceability and control over documents and cases
A quality management system creates order and clarity within an organization by gathering all essential processes in one place. It simplifies quality management, reduces administration, and makes it easier to meet standards and regulations.
Makes it easy to do the right things
Discover how AM System brings structure to processes, documents, and workflows.
What Should a management system Include?
A management system should consolidate all guidelines, processes, and documents in one central location to ensure consistency and quality. By incorporating smart tools for document management, case management, and process mapping, structured and efficient work becomes easier.
Document Management
A document management system helps keep track of important files, ensures version control, and facilitates collaboration. With a digital solution, documents can be easily found, shared, and updated in real-time, reducing the risk of errors and information loss. Automated permissions and secure storage ensure that the right person has access to the right information at the right time.
Case Management
A case management system makes it easy to create, track, and resolve cases in a systematic manner. Whether dealing with deviations, improvement suggestions, or complaints, the system provides a clear overview and a structured workflow, minimizing the risk of anything being overlooked.
Process Mapping
A process mapping system simplifies the visualization and optimization of workflows. By creating clear process maps, companies can identify bottlenecks, improve efficiency, and ensure that all employees follow the same guidelines.
Achieve ISO 9001 Certification
ISO 9001 is an international standard for management systems used by companies worldwide to ensure quality and efficiency. To become certified, an organization must meet requirements including:
- Clear documentation of processes and procedures
- Systems for managing risks and opportunities
- Monitoring customer satisfaction and quality objectives
- Leadership commitment to quality management
- Continuous improvement and follow-ups
Achieving ISO 9001 certification demonstrates that a company maintains high standards and systematically works with quality. It enhances brand credibility, simplifies collaborations, and can open up new business opportunities by meeting customer and supplier requirements.
Increase Efficiency with AM System
A management system from AM System is used by management teams, quality managers, and employees to create structure and ensure compliance with procedures and requirements. Through a digital platform, the entire team gains a shared space for documentation, processes, and case management. With our cloud-based platform, information is always up-to-date and accessible, no matter where or when you work.
Get a demo
Ready to make work easier - and more enjoyable?
Want to see for yourself how AM System can make a difference for you? Request a demo and discover how easy it is to create structure, efficiency, and seamless workflows in your daily operations.
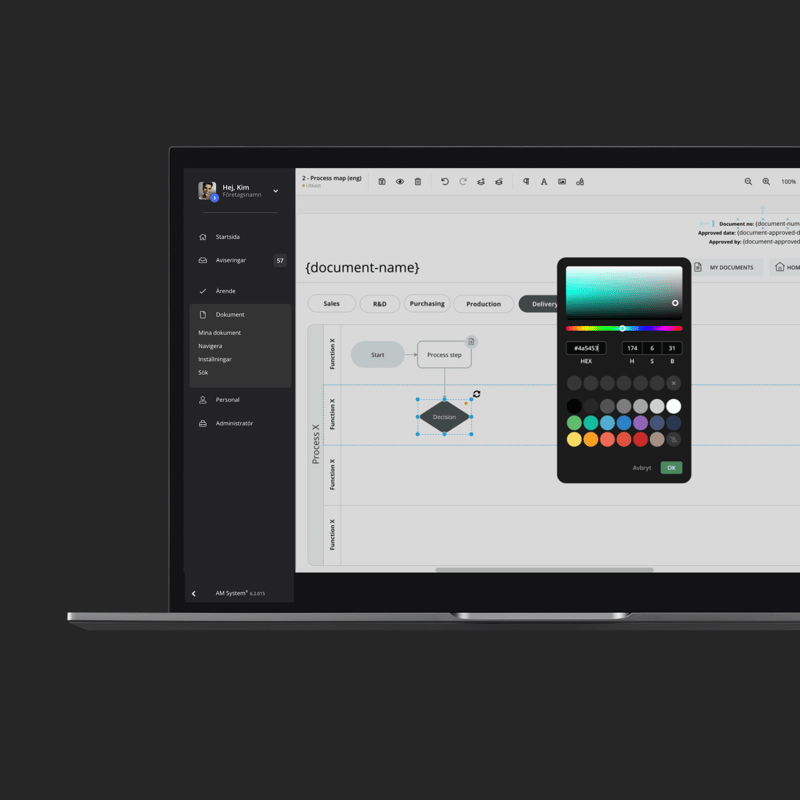