Article
Continuous improvement - a culture of development and success
-
Editorial team
-
- Case Management
- 4 min reading
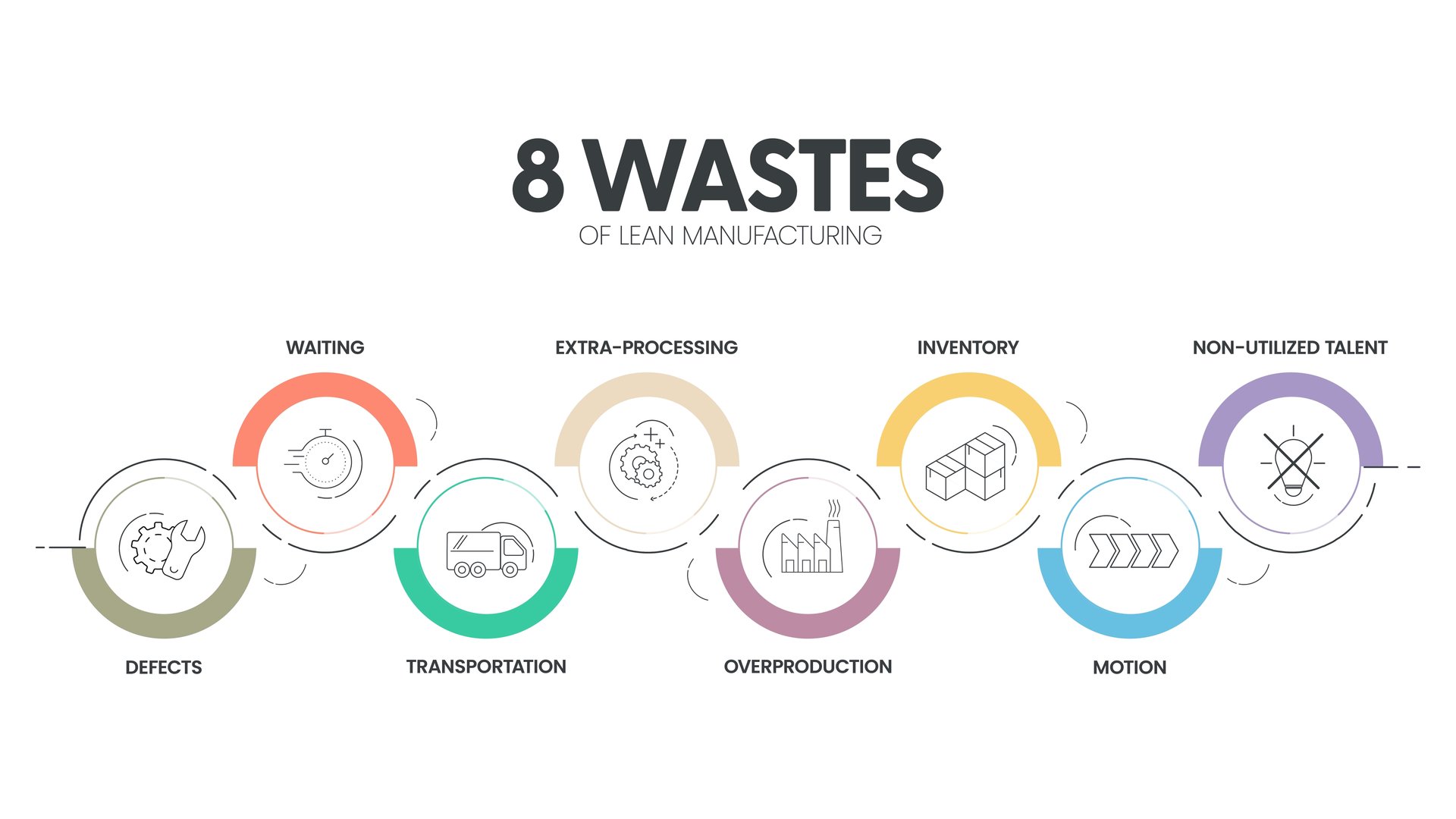
Continuous improvement is a philosophy that underpins many successful organizations. It involves always striving to improve processes, products and working methods, step by step, instead of waiting for big and often difficult changes.
This methodology not only enables higher quality and efficiency, but also creates an engaging work environment where everyone feels involved in the success of the business
Continuous improvement is based on the idea that nothing is perfect and that there is always room for improvement. By identifying small opportunities for improvement and implementing them on a regular basis, companies can create long-term positive change that strengthens competitiveness and customer satisfaction.
What does continuous improvement mean?
Continuous improvement is not a single method or technique, but a way of thinking and acting that permeates the whole organization. It is about constantly asking questions like:
- How can we do this better?
- What can we change to be more efficient?
- Is there anything that can be simplified or improved?
This approach means that improvements are not limited to specific departments or projects, but that everyone in the organization contributes to identifying and implementing improvements. This could be anything from optimizing a production line to improving communication between departments or enhancing the customer experience.
An important element of continuous improvement is to always base decisions on facts and data. By analyzing information about how processes work today, it becomes easier to identify where the problems are and what solutions are most effective.
Methods for working with continuous improvement
There are many different methods that can be used to structure continuous improvement work. Some of the most established are:
Lean
Lean is a methodology that aims to maximize value for the customer by eliminating anything that does not add value. Originally developed within the Toyota Production System (TPS), Lean focuses on creating a smooth flow and reducing waste in all forms.
The eight types of waste, or 8 wastes of Lean, that Lean identifies are:
- Waste by producing more than is needed
- Waste due to waiting times.
- Waste due to unnecessary transportation.
- Waste due to too much or incorrect handling.
- Waste due to overstocking
- Waste due to unnecessary movements.
- Waste due to manufacturing products with errors.
- Waste due to underutilized employees and their skills.
Lean is based on principles such as 'just-in-time', where only what is needed is produced, and 'jidoka', which involves automating processes with human supervision to ensure quality.
Kaizen
Kaizen, which means 'change for the better' in Japanese, is a philosophy of continuously improving every aspect of an organization. Kaizen is about making small, continuous improvements that add up to big results over time.
A key part of Kaizen is involving employees in the improvement process. Those who work closest to the processes often have the best insight into what can be improved and how it can be done. Kaizen meetings and workshops are often used to gather ideas and develop solutions in teams.
Six Sigma
Six Sigma is a data-driven methodology used to improve quality and reduce variation in processes. By using statistical tools, Six Sigma identifies and eliminates causes of defects and deviations. The goal is to achieve a level where less than 3.4 defects per million opportunities occur.
Six Sigma often follows the DMAIC (Define, Measure, Analyze, Improve, Control) cycle, where each step aims to create sustainable improvements.
Total Quality Management (TQM)
Total Quality Management (TQM) is a holistic approach to quality that emphasizes that every part of the organization, from product development to customer service, has a responsibility to deliver value to the customer. TQM is based on principles such as customer focus, employee engagement and continuous improvement.
How continuous improvement creates value
Working with continuous improvement means that an organization systematically seeks opportunities to improve all aspects of its operations, from production and delivery to internal processes and customer relations. The impact of continuous improvement goes far beyond individual gains - it creates a foundation for long-term success and sustainable development. Here's how continuous improvement can create value in several crucial areas:
Improving quality
Quality is at the heart of any successful business. By identifying and eliminating flaws in processes, you ensure that your products and services consistently meet or exceed customer expectations. This means that you not only improve the end product, but also strengthen your organization's trust with customers and other stakeholders.
Example: By implementing standardized work methods and using Lean principles such as just-in-time and jidoka, you can minimize errors in production. When a problem is detected at an early stage - for example, a deviation in material quality - it can be addressed before it affects the final product. This not only reduces rework costs, but also ensures that your deliveries are of the highest possible standard.
More efficient use of resources
Resources - be it time, materials or labor - are always limited. By focusing on eliminating waste and inefficient working practices, you free up resources that can be used to create more value in your business. This can mean anything from reducing overproduction and waiting times to optimizing supply chains and reducing energy consumption.
Example: A company discovers that certain machines in production are often idle while waiting for the next work step. By analyzing the process and redistributing workflows, lead times can be reduced and machines used more efficiently. This increases productivity without requiring additional investment.
Stronger employee engagement
Employees are an organization's most important resource, and their engagement is crucial to the success of improvement efforts. When employees feel that their ideas and efforts contribute to the success of the business, they become more motivated and engaged. Involving them in the improvement process - for example through Kaizen workshops or improvement teams - creates a culture of participation and innovation.
Example: A team on the floor of a production facility is tasked with identifying small improvements in their working environment. They propose to move tools and materials closer to workstations, reducing unnecessary movement. The change leads not only to a more efficient working day, but also to increased satisfaction and pride among employees, who see that their ideas are taken seriously.
Higher customer satisfaction
Customer satisfaction is a direct reflection of the quality of your products and services, as well as how well you can meet customers' needs and expectations. By continuously improving your offers and deliveries, you show that you are a reliable partner that prioritizes customer success. This strengthens relationships and can also create loyalty that leads to repeat business and recommendations.
Example: A manufacturing company notices that some deliveries are often delayed due to logistics bottlenecks. By analyzing and adjusting the supply chain, the company can reduce late deliveries and offer customers shorter lead times. This improvement not only leads to more satisfied customers but also to the company being seen as a more competitive player in the market.
Coherent value creation
Continuous improvement creates value on multiple levels, but it is when these effects interact that the real results emerge. Improved quality leads to more satisfied customers, which strengthens the brand and generates more business opportunities. More efficient use of resources frees up capital to invest in innovation and development. Stronger employee engagement builds a culture that fosters creativity and accountability, which drives improvement.
By embedding continuous improvement into your business strategy and daily operations, you create an organization that not only adapts to change, but actively drives it. It is a powerful route to long-term success and sustainability in a competitive world.
Summary: Continuous improvement as a strategic key
Continuous improvement is more than just process improvement - it is a philosophy that permeates the entire organization and creates a culture of learning and development. By using proven methods such as Lean, Kaizen and Six Sigma, companies can create a systematic and effective strategy to address challenges, improve quality and strengthen their position in the market.
For manufacturing companies, continuous improvement is a strategic key to long-term success. By identifying and implementing improvements every day, you can build a business that not only meets customer expectations but also drives innovation and competitiveness.
Get a demo
Ready to make work easier - and more enjoyable?
Want to see for yourself how AM System can make a difference for you? Request a demo and discover how easy it is to create structure, efficiency, and seamless workflows in your daily operations.
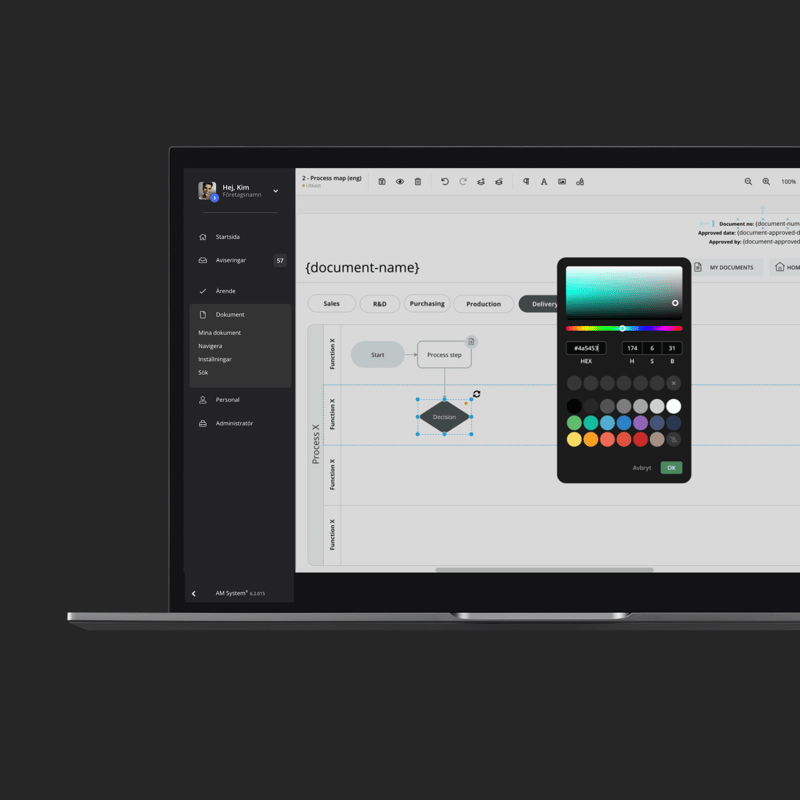