Article
How to build a culture of continuous improvement
-
Editorial team
-
- Case Management, Quality Management System
- 7 min reading
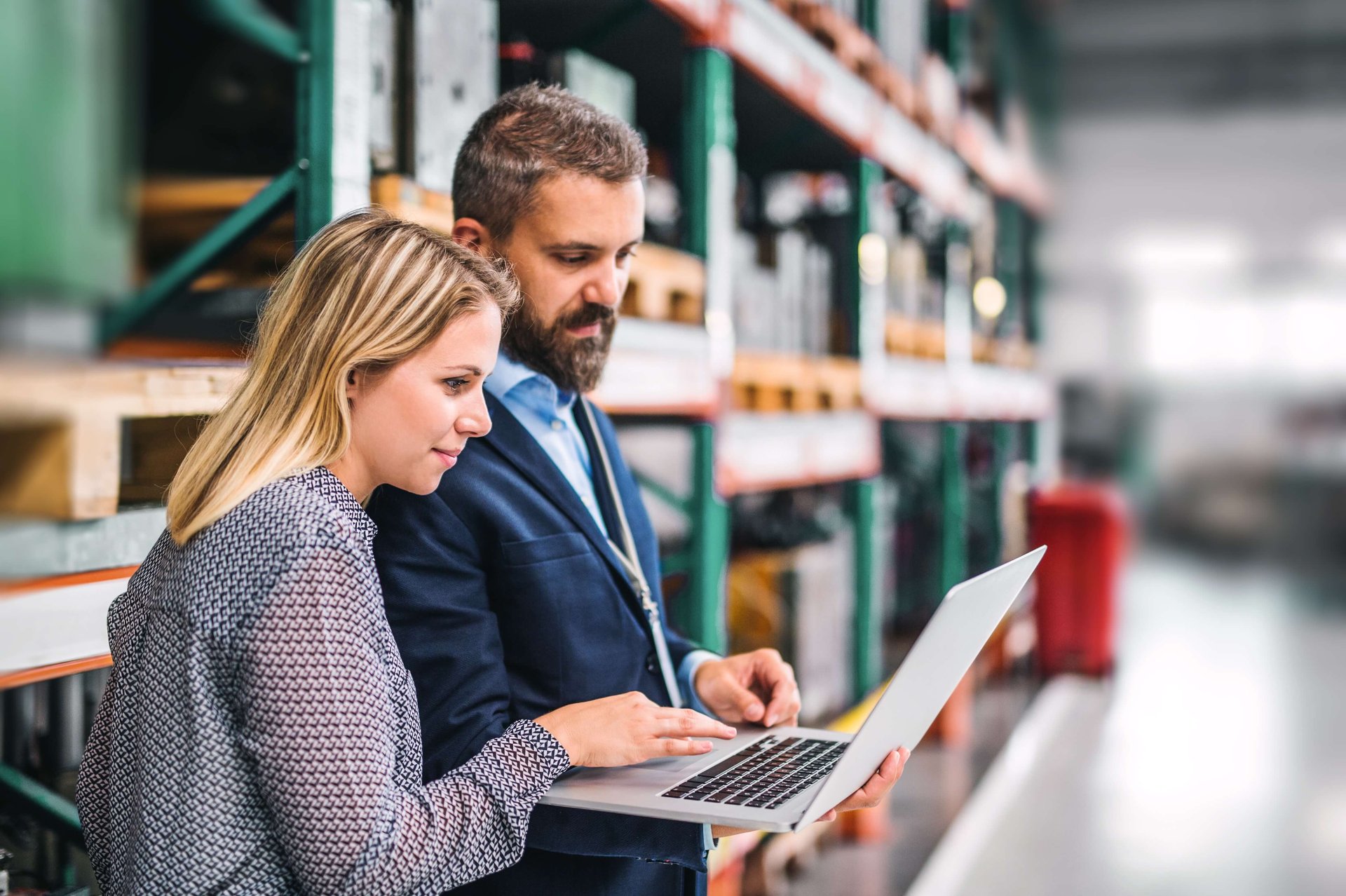
Creating a culture of continuous improvement means making improvement work a natural and obvious part of everyday life in your organization. Success requires not only methods and tools, but also systematic efforts to engage employees, set goals and foster a learning environment. In this article, we outline five key steps to build and maintain a culture of continuous improvement.
1. Involve employees in improvement efforts
Employees are the key to successful continuous improvement. Those who work closest to the processes have a deep understanding of how the business works in practice and can often identify improvement opportunities that are not obvious to management. Engaging employees in improvement efforts is therefore crucial to creating a culture where change is seen as an opportunity rather than a challenge.
Create forums for sharing ideas
In order for employees to share their insights and suggestions, structured forums for exchanging ideas are needed. This can be done through regular meetings, workshops or digital platforms where employees have the opportunity to raise suggestions for improvement and discuss them together.
For example, workshops can focus on specific areas, such as reducing waste in production or improving internal communication flows. Another option is to have weekly improvement meetings where teams are given time and space to reflect on their working practices and discuss what can be done better.
Digital platforms and tools, such as AM System, can complement these meetings by providing a channel for employees to share ideas on an ongoing basis. Such a tool makes it possible to document, categorize and follow up on suggestions in a structured way, ensuring that no ideas are lost.
Provide the right tools for reporting and follow-up
An important part of engaging employees is giving them access to tools that make it easy to participate in improvement efforts. Digital case systems are an excellent example of how technology can be used to facilitate reporting and follow-up of improvement suggestions.
In a digital system, employees can report problems or inefficiencies directly, without having to go through several steps. The system can then be used to prioritize and assign suggestions to responsible individuals or teams, making improvement efforts both transparent and structured.
When employees have access to easy-to-use tools and see that their ideas are documented and acted upon, it builds trust in the process, which in turn boosts engagement.
Build a culture of appreciation
In order for employees to feel motivated to contribute, a culture where their efforts are valued and recognized is needed. It's not just about implementing ideas that lead to big changes, but also about highlighting and rewarding smaller suggestions that contribute to improvements over time.
An easy way to build a culture of appreciation is to highlight successful improvement initiatives during meetings or in internal newsletters. You can also introduce a reward system that recognizes employees who contribute to improvement efforts, for example through awards or symbolic prizes.
Creating a sense that all ideas are important, whether they lead to immediate changes or not, will increase motivation and encourage more people to make suggestions.
Involving employees in the improvement process is about creating conditions for participation and empowering them. By building a culture of openness, support and appreciation, the organization can unleash its full potential and create a strong foundation for continuous improvement.
2. create clear goals and metrics
Clear goals and metrics are crucial to ensure that improvement efforts lead to tangible results. Without goals, efforts can become diffuse and difficult to track, which can lead to a lack of clarity about progress and a loss of commitment. By setting goals that are specific, measurable and linked to the organization's overall strategy, you create a direction for the improvement work and enable a structured follow-up.
Set relevant targets
For improvement efforts to have maximum impact, targets must be relevant and linked to the organization's strategic priorities. This means that the objectives should reflect the areas where the organization has the greatest potential for improvement or where there are challenges that need to be addressed.
For example, a strategic objective could be to reduce the number of defective products reaching customers. This can then be broken down into operational objectives for specific departments, such as improving control processes in production or implementing more detailed testing during the development phase.
By breaking down strategic objectives into operational and tactical sub-objectives, you ensure that improvement efforts are manageable and that all levels of the organization understand their role in achieving the objectives.
Use metrics to track progress
Metrics serve as a tool to assess how well your organization is succeeding in its improvement initiatives. By using concrete metrics, you can identify trends, track successes and gain insight into areas that need further focus.
Examples of relevant metrics may include:
- Quality-related metrics: Number of complaints, defects per unit or reduction in rework.
- Efficiency-related metrics: Production speed, lead times or resource utilization.
- Engagement-related metrics: employee satisfaction, participation in improvement initiatives or number of ideas generated by employees.
Choosing the right metrics is important. They should be easy to understand, relevant to the business objectives and based on data that is accessible and reliable. Using visual aids such as graphs or dashboards can also make it easier for everyone in the organisation to track progress.
Follow up and adjust regularly
Targets and metrics are not static - they need to be monitored and adjusted regularly to ensure they remain relevant and realistic. Regular monitoring allows you to evaluate how well your organization is achieving its goals and identify where improvement efforts need to be strengthened.
An effective way to follow up is to schedule regular reviews, such as monthly or quarterly meetings where teams review their performance and analyze what worked well and what can be further improved.
If necessary, the objectives can be adjusted to better reflect changing priorities or circumstances. For example, if an initial effort to reduce complaints has yielded good results, the focus can be shifted to improving delivery accuracy or increasing employee productivity.
Targets and metrics as a basis for improvement
Creating clear goals and using relevant metrics is a crucial part of continuous improvement. By setting goals that are linked to your organization's strategy, using concrete metrics to track progress, and regularly evaluating and adjusting your efforts, you can ensure that your improvement efforts lead to real results.
This structure helps the organization stay focused and gives employees a clear picture of what is expected and how their efforts contribute to the whole. This not only leads to better results, but also to a culture of accountability and commitment to improvement.
3. lead by example
Leadership is key to shaping a culture where continuous improvement is not just a strategy but part of the organization's DNA. Leaders set the tone for how improvement is prioritized, implemented and perceived by employees. By setting an example and showing commitment, leaders can inspire the organization to actively participate in the change process.
Showing commitment
When leaders actively participate in improvement efforts, they show employees that this work is a priority. Attending workshops, participating in analysis meetings or leading improvement initiatives themselves sends a clear signal that improvement is not just a requirement but an opportunity.
An example is a production manager who gets involved in identifying bottlenecks on the production floor. By being involved in finding solutions and implementing improvements, the manager shows that change management is part of the organization's core business.
Supporting and rewarding efforts
Supporting improvement initiatives and highlighting successes is a powerful way to motivate employees. This can include providing resources to implement ideas, such as time or tools, or recognizing teams and individuals who contribute to improvement efforts. Rewards don't have to be big - recognition during a meeting or an internal award can have a big impact on motivation.
Showing that every improvement effort counts, whether it's a minor workflow or a major process change, creates a sense of appreciation and commitment.
Building trust
Open and inclusive leadership is the foundation for building trust. When leaders listen to employees' ideas, encourage dialog and are transparent with decisions, they create an environment where employees feel safe to participate in improvement efforts.
For example, leaders can regularly invite conversations where employees have the opportunity to share their perspectives and ideas. This strengthens relationships and makes it easier to drive changes that have the support of the whole organization.
4. implement structured methods
For improvement efforts to be successful, a clear structure is required. Using established methodologies such as Lean, Kaizen or Six Sigma provides the organization with a framework that makes it easier to identify, analyse and implement improvements in a systematic way.
Lean: Eliminate waste and optimize flow
The Lean approach focuses on eliminating anything in the processes that does not create value for the customer. This could be overproduction, long waiting times or inefficient transportation. By analyzing your operations based on Lean principles, you can find and fix these wastes, leading to better resource utilization and shorter lead times.
One example is using the '5S' principle of Lean to organize workstations in a way that reduces unnecessary movement and streamlines workflow.
Kaizen: Small steps towards big improvements
Kaizen is about continuously improving operations through small, incremental changes. The focus is on making improvements part of everyday life, rather than large, time-consuming projects. By encouraging employees to regularly reflect on their working practices and suggest small improvements, you can create a long-term culture of change.
For example, a team in a warehouse might identify an unnecessary work routine and suggest a change that reduces the daily workload.
Six Sigma: Data-driven quality and precision
Six Sigma is a methodology that focuses on reducing variation and defects in processes through a structured, data-driven analysis. It uses tools such as DMAIC (Define, Measure, Analyze, Improve, Control) to create improvements that are both effective and measurable.
For example, a company using Six Sigma may identify that a particular production line has a higher defect rate than others. By analyzing the data, they find the cause - perhaps a machine that is not properly calibrated - and fix the problem.
5. Celebrate successes and learn from mistakes
To maintain commitment to improvement, it is important to recognize successes and use mistakes as a source of learning. An organization that celebrates its successes and looks at its mistakes as opportunities for development creates a safe and motivating environment.
Celebrating small and big successes
Every success, big or small, deserves to be celebrated. It could be highlighting a team that has implemented a new way of working, or celebrating a major milestone like achieving a quality target. Recognizing successes shows employees that their work is valuable and appreciated.
For example, a company could introduce an 'improvement of the month' where successful projects are highlighted in internal newsletters or during meetings.
Analyze failures and learn from them
Failures are a natural part of improvement work, and how they are handled is crucial for the development of the organization. By analyzing what went wrong and why, you can avoid repeating the same mistakes.
It is important to create an environment where employees are not afraid to fail. Openness and reflection allow mistakes to be seen as an opportunity for improvement rather than an obstacle.
Sharing experiences and lessons learned
Experiences from improvement work, both successes and challenges, should be shared within the organization. Creating forums where employees can present their projects and insights will spread the knowledge and inspiration to other parts of the organization.
One example is to organize internal presentations where different departments can present their improvement projects and lessons learned. This strengthens collaboration and drives the improvement culture forward.
To summarize
Building a culture of continuous improvement requires commitment from both leaders and employees, and structured methods to drive the work forward. By leaders leading the way, using established practices, and celebrating both successes and lessons learned, organizations can create a sustainable culture that fosters growth and adaptability.
With the right focus, tools and attitude, improvement becomes not just a strategy but part of the organization's everyday life - and a key to long-term success.
Get a demo
Ready to make work easier - and more enjoyable?
Want to see for yourself how AM System can make a difference for you? Request a demo and discover how easy it is to create structure, efficiency, and seamless workflows in your daily operations.
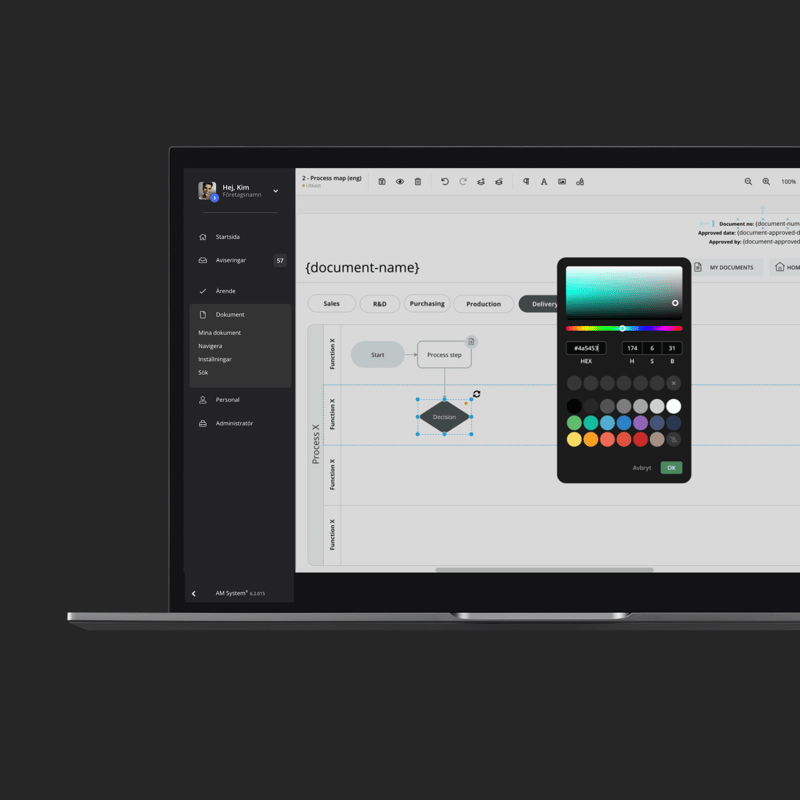