Article
Deviation and deviation management: the key to learning and improvement
-
Editorial team
-
- Case Management
- 4 min reading
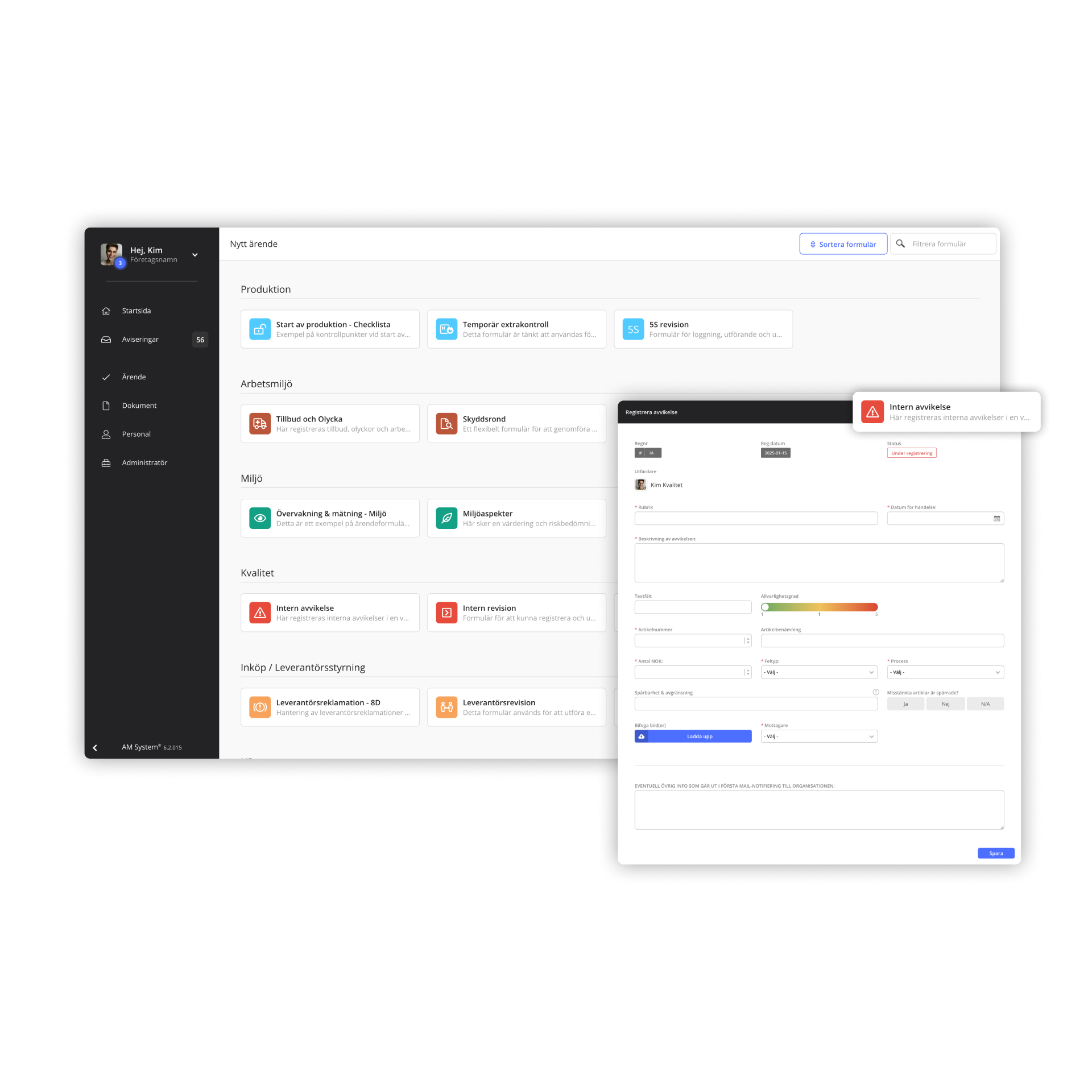
Deviations are an inevitable part of any business, regardless of the industry. They can range from minor issues of detail to major incidents that affect the whole business. How you manage deviations can be critical to the success of your business, as there is likely to be so much to learn across so many processes from a single deviation.
With a structured and clear deviation management process, you can not only minimize the risk of the same error happening again, but also learn important lessons within your organization that will help you prevent similar problems in the future.
Are you maximizing the value of each deviation that occurs?
What is an anomaly?
A deviation can be defined as something that prevents you from following the agreed standards, procedures, or instructions that apply to a process or work step. It could be a broken tool, incorrect raw material, a machine problem or a work environment factor. Deviations can also be the result of human factors, such as lack of knowledge or misunderstanding.
What all deviations have in common is that they pose an increased risk to the business and should be managed in a systematic way to avoid affecting quality, safety or efficiency.
The importance of effective deviation management
Nonconformity management is about much more than just solving problems when they arise - it is a central part of systematic quality work and a prerequisite for creating a learning and improvement-oriented organization. When identified and handled properly, deviations become not only obstacles that need to be addressed, but also valuable opportunities for reflection and development for everyone involved in the planning, execution and monitoring of the process.
Clear and effective deviation management creates a working environment where employees can feel safe and involved in the improvement work. By daring to address deviations in a structured way, you can not only prevent problems, but also ensure that the entire organization learns from the mistakes that occur.
An anomaly is not only a problem to be solved - it is also a source of knowledge. By analyzing the root causes of a deviation, you will gain a deeper understanding of your processes and identify areas that need to be changed and improved. Learning in this context is invaluable, both to avoid similar problems in the future, as well as to continuously improve working practices at an overall level.
How to prevent risks and promote learning
To create a learning organization, it is good to include more people in being able to identify deviations. Then you use each deviation as an opportunity to draw conclusions and share insights. A good way to do this is to systematically work with, document and communicate lessons learned from the deviation management to all relevant departments and employees.
When the whole organization is engaged in learning, nonconformity management becomes a catalyst for continuous development.
One of the benefits of simple and effective incident management is also to identify and address risks before they develop into major problems. When deviations are reported and managed correctly and effectively, you are likely to minimize further negative impacts on production, the working environment or customer satisfaction. This is likely to be the case in many industries and especially in industries where safety and quality are crucial, such as manufacturing. There, deviations need to lead to a clear identification of root causes, short- and long-term activities, as well as to new valuable risk assessments and actions across processes or a family of products.
Creating the culture
To really dare to benefit from deviation management, the culture is as important as the method. Nonconformities are not personal failures, but opportunities for processes or for the organization due to reasons that have not been known or handled correctly. So try to create an environment where employees feel comfortable reporting nonconformities because they are seen as a natural part of the organization's development.
Having a structured and easily accessible system for everyone where you can easily document, analyze and fix deviations greatly facilitates the creation of that culture. A digital tool can make it easier to create an overview and ensure that insights from deviation management are disseminated and used throughout the organization. It becomes not something that "someone else does" but a natural part of everyday life, which creates security for the individual.
By integrating deviation management as a natural part of all employees' everyday work, you can create an organization that not only effectively handles problems when they arise, but also grows and develops from them. In this way, deviation management becomes a strategic tool to constantly strengthen both the quality and competitiveness of your business.
An effective way to manage deviations is to use a digital system like AM System.
Summary of the system
Deviations are a natural part of every business, but they do not have to be an obstacle. With structured and effective deviation management, you can turn problems into opportunities and create a culture of continuous learning and improvement. By using the right tools and methods, you can ensure that your processes not only meet standards and requirements, but also evolve to meet future challenges.
Whether you are at the beginning of your deviation management journey or already have an established process, you can always evolve your work to make it more efficient and value-adding. Start by creating a clear structure, involve your staff and use the lessons learned from each incident to build a stronger and more resilient organization.
Get a demo
Ready to make work easier - and more enjoyable?
Want to see for yourself how AM System can make a difference for you? Request a demo and discover how easy it is to create structure, efficiency, and seamless workflows in your daily operations.
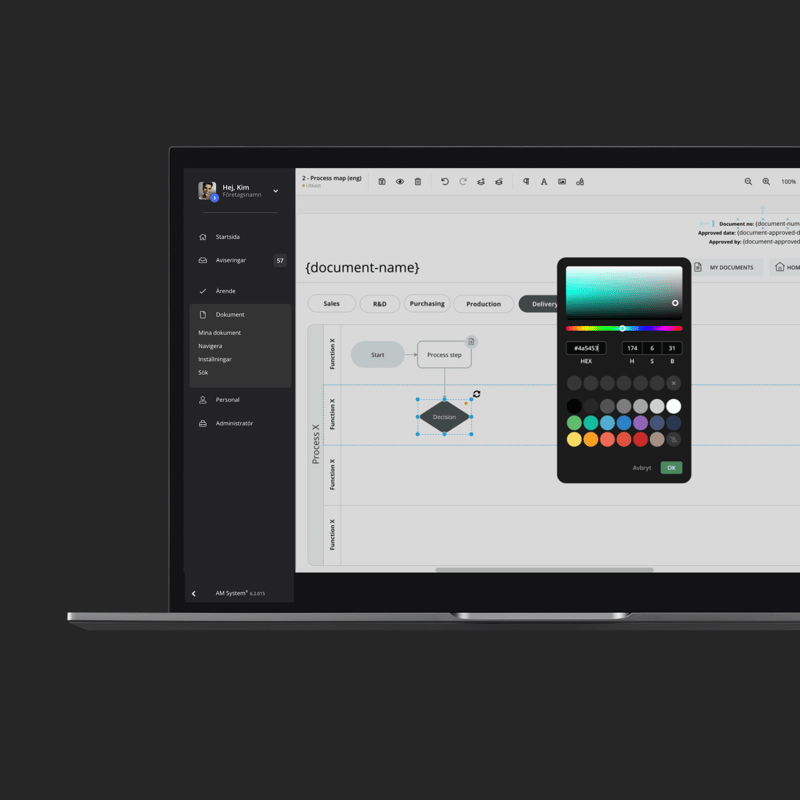