Article
Step-by-step guide to process mapping
-
Editorial team
-
- Process Mapping
- 4 min reading
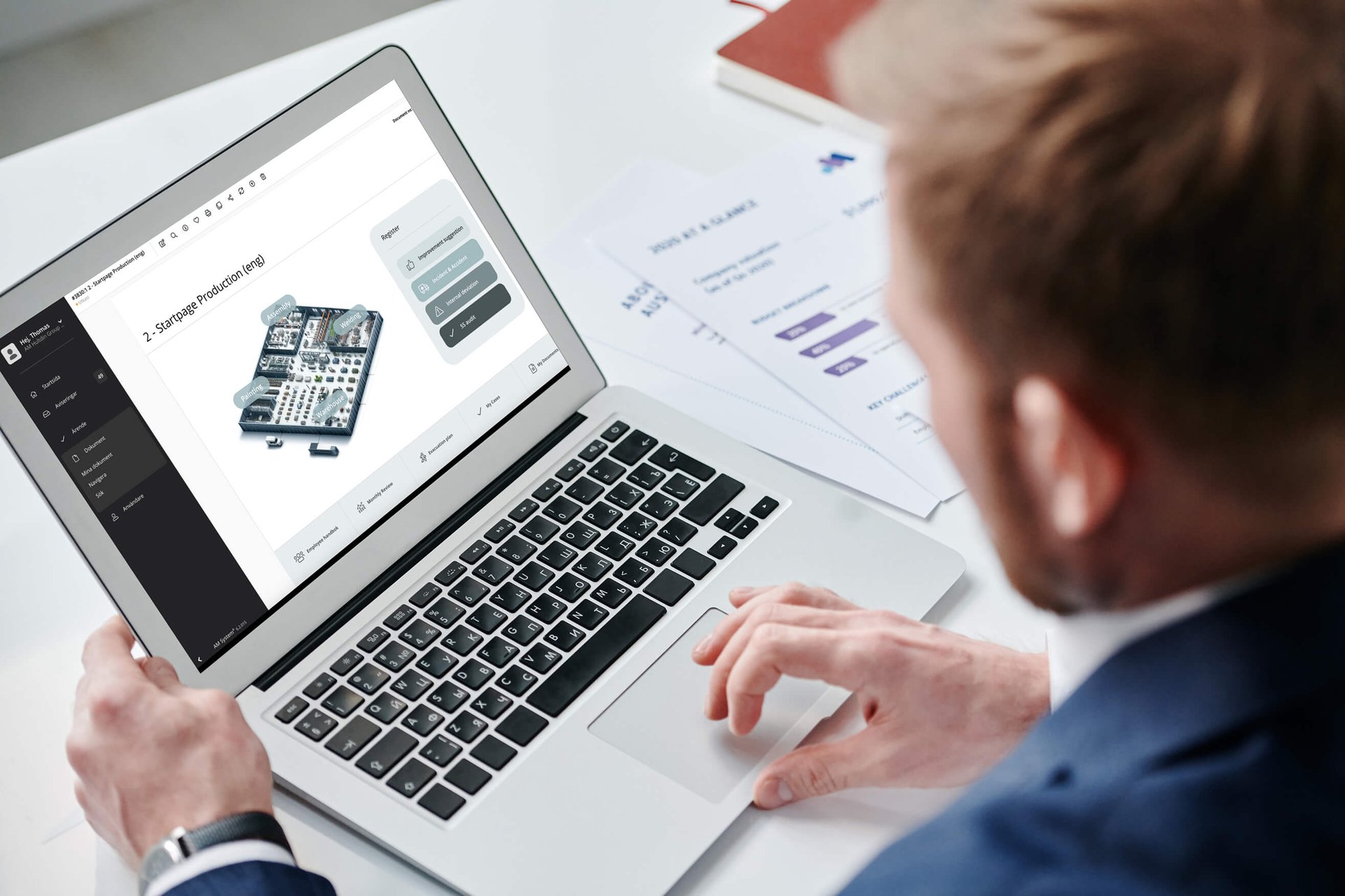
Step-by-Step guide to process mapping
Understanding and improving how an organization works is key to long-term success. Process mapping is a method that helps visualize workflows and identify both strengths and areas for improvement. By creating a clear picture of how work is carried out, companies can ensure that everyone follows standardized and efficient practices. It also lays the foundation for continuous improvement and greater competitiveness.
In this article, we walk you through five simple steps to help you create a process map that makes workflows visible and supports improvement initiatives.
How process mapping Works
Process mapping involves describing and visualizing how different parts of the organization's work are done. Instead of using long and detailed texts, this is often done through clear diagrams or flowcharts. This method makes it easy to analyze and understand workflows and the relationship between different steps in the process.
How to create a process map – step by step
Getting started with process mapping is easier than you might think. Here are five practical steps to help you visualize your processes in a way that’s easy to understand – and use.
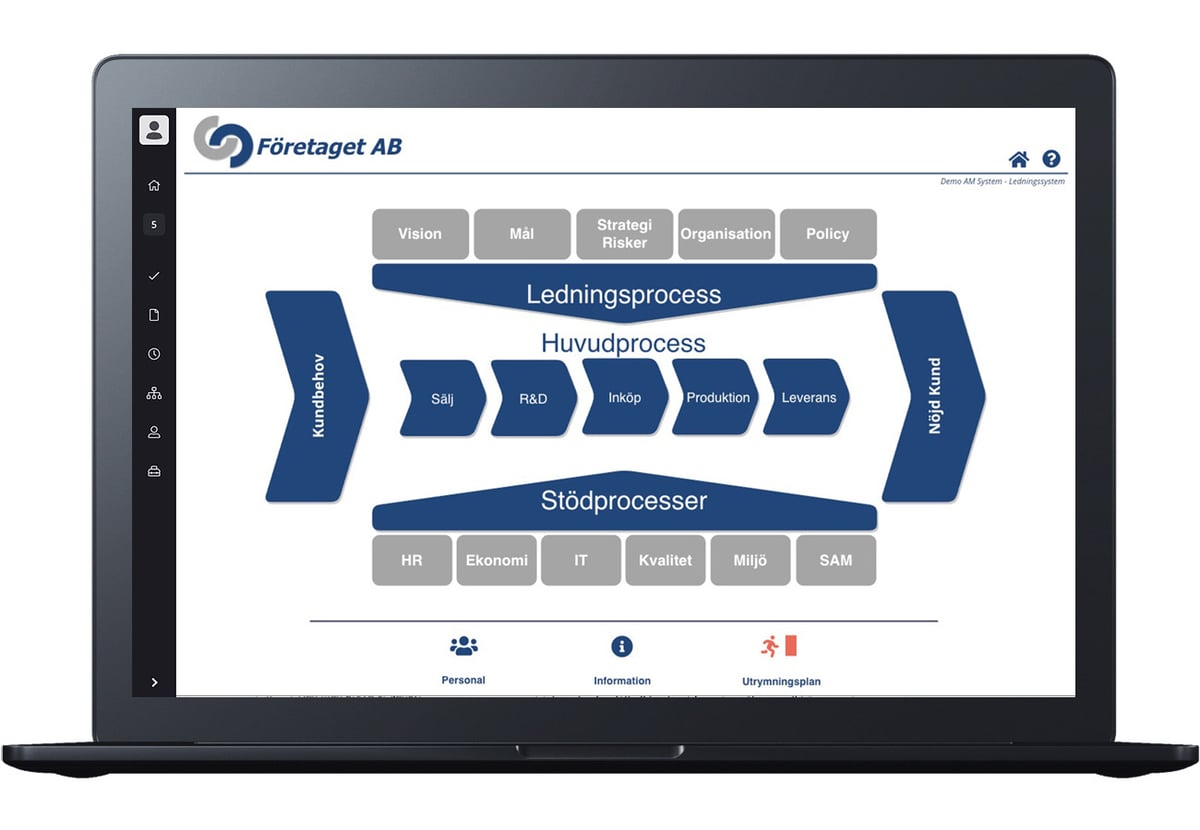
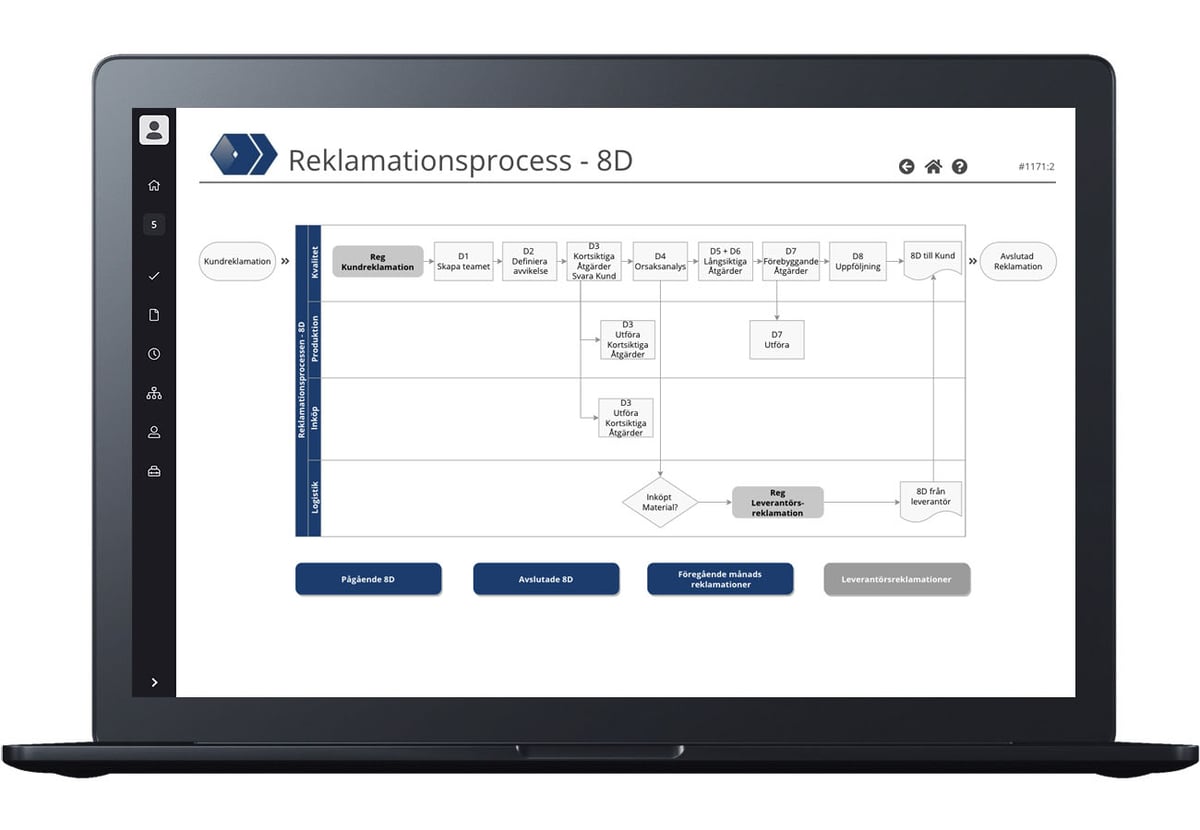
- Choose a process to map
Start with a process that is important, recurring, or problematic. It might be something that often causes confusion or an area where efficiency could be improved. A clear purpose will yield better results. - Involve key people and identify activities
No one knows the process better than the people who work with it. Involve team members from different roles to outline the steps and actions involved. Then list the activities and clarify who is responsible for what. - Structure the flow
Sort all the activities in logical order – from start to finish. Make sure the flow is clear and complete. This step lays the foundation for a visual map that everyone can follow. - Build your process map
Sketch the process by hand or use a digital process mapping tool. With AM System, you can easily create clickable process maps that link to documents, tasks, and the next steps – all in one unified platform. - Analyze and improve
Once the map is complete – use it! Identify improvement areas, update the map when things change, and make sure it stays relevant. A good process map is a tool for continuous improvement.
Three main types of processes
Although every organization is unique in its structure and operations, most workflows can be divided into three main categories:
- Management processes
Management processes guide and navigate the organization. They include strategic activities such as environmental analysis, planning, goal setting and monitoring. For example, setting business objectives and ensuring that all parts of the organization work in line with them. Management processes are also about ensuring that laws, requirements and standards are upheld and that resources are used in an optimal way. Without clear management processes, the organization risks lacking direction and focus. - Main processes or core processes
Core processes are at the heart of the business and are based on customer needs. These processes aim to create and deliver the value that the customer expects, whether it is a good or a service. In a manufacturing company, this may include steps such as product development, sourcing, manufacturing and delivery. The main processes are the most business-critical and often require careful analysis to ensure they meet both internal and external requirements. - Support processes
Supporting processes are those that enable the main processes to be carried out. They may not be as visible to the outside world, but their importance to the success of the organization is crucial. Supporting processes include areas such as HR, IT and finance, which provide the organization with the right conditions to deliver its products or services. An example could be HR's role in recruiting and training staff or IT's responsibility for maintaining digital systems that support production. In a traditional process model, quality is often placed under supporting processes, but in more modern manufacturing companies, quality can be seen as a central or integrated process.
Why is process mapping important?
Process mapping not only creates structure, but also contributes to a deeper understanding of how the organization works. When processes are clearly documented and visualized, it becomes easier to spot inefficient steps or activities that do not add value.
A common outcome of process mapping is that unnecessary work steps are identified and eliminated, leading to better use of resources and lower costs. At the same time, improvements introduced can strengthen the quality of what is delivered to the customer.
Furthermore, process mapping promotes collaboration and communication within the organization. When employees have a clear picture of how their work affects the whole, their commitment and understanding of their own role increases. This leads to a stronger culture of collaboration and a greater sense of responsibility.
How to get started with process mapping?
To start process mapping, it is important to first map the current situation, i.e. how work is actually done today. Involve employees from different parts of the organization to ensure that you get as accurate and complete a picture as possible.
Once the current situation is mapped, you can start visualizing the processes, using tools such as flowcharts or process models to visualize the workflow in a clear and easy-to-understand way. It is also important to analyze the process thoroughly to identify areas for improvement and clarify who is responsible for the different steps in the process.
After the analysis, you can implement the improvements and ensure that the new processes are communicated and understood by everyone. This step is crucial for the changes to have an impact and become part of the daily work of the organization.
To summarize
Process mapping is a method that helps organizations get a clearer picture of their workflows and identify improvement opportunities. By analyzing and visualizing the ways of working, the conditions are created for working more clearly, structured and efficiently, while making it easier to meet both internal and external requirements.
Whether the focus is on management processes, main processes or support processes, process mapping provides a clear structure for improvement work. By working methodically with this, organizations can ensure that their processes support the business objectives and strengthen its long-term development. Process mapping thus becomes a practical and concrete part of creating a better functioning organization.
Get a demo
Ready to make work easier - and more enjoyable?
Want to see for yourself how AM System can make a difference for you? Request a demo and discover how easy it is to create structure, efficiency, and seamless workflows in your daily operations.
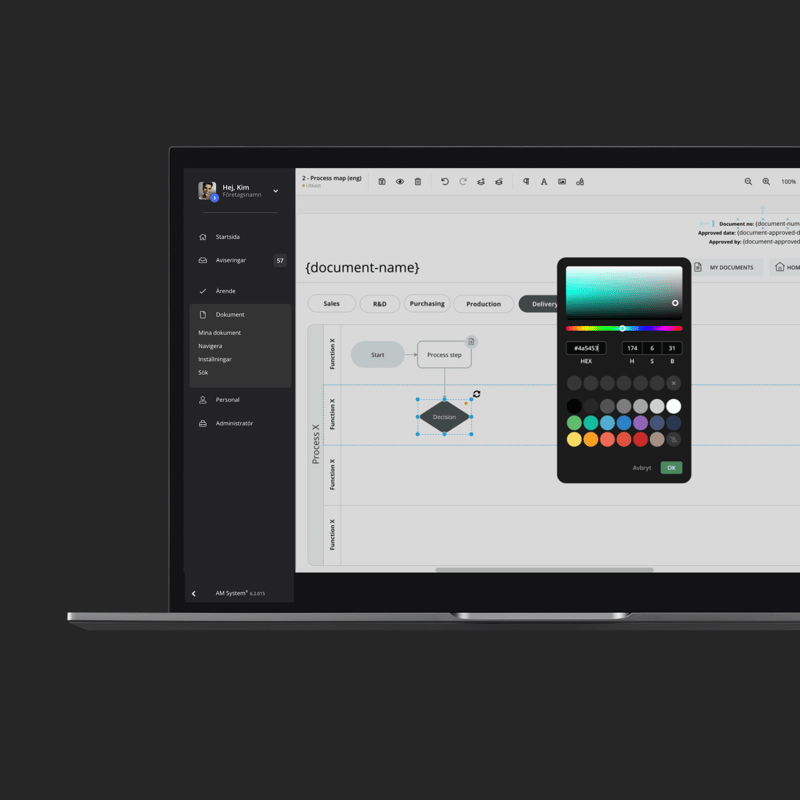