Article
What is a quality system?
-
Editorial team
-
- Quality Management System
- 4 min reading
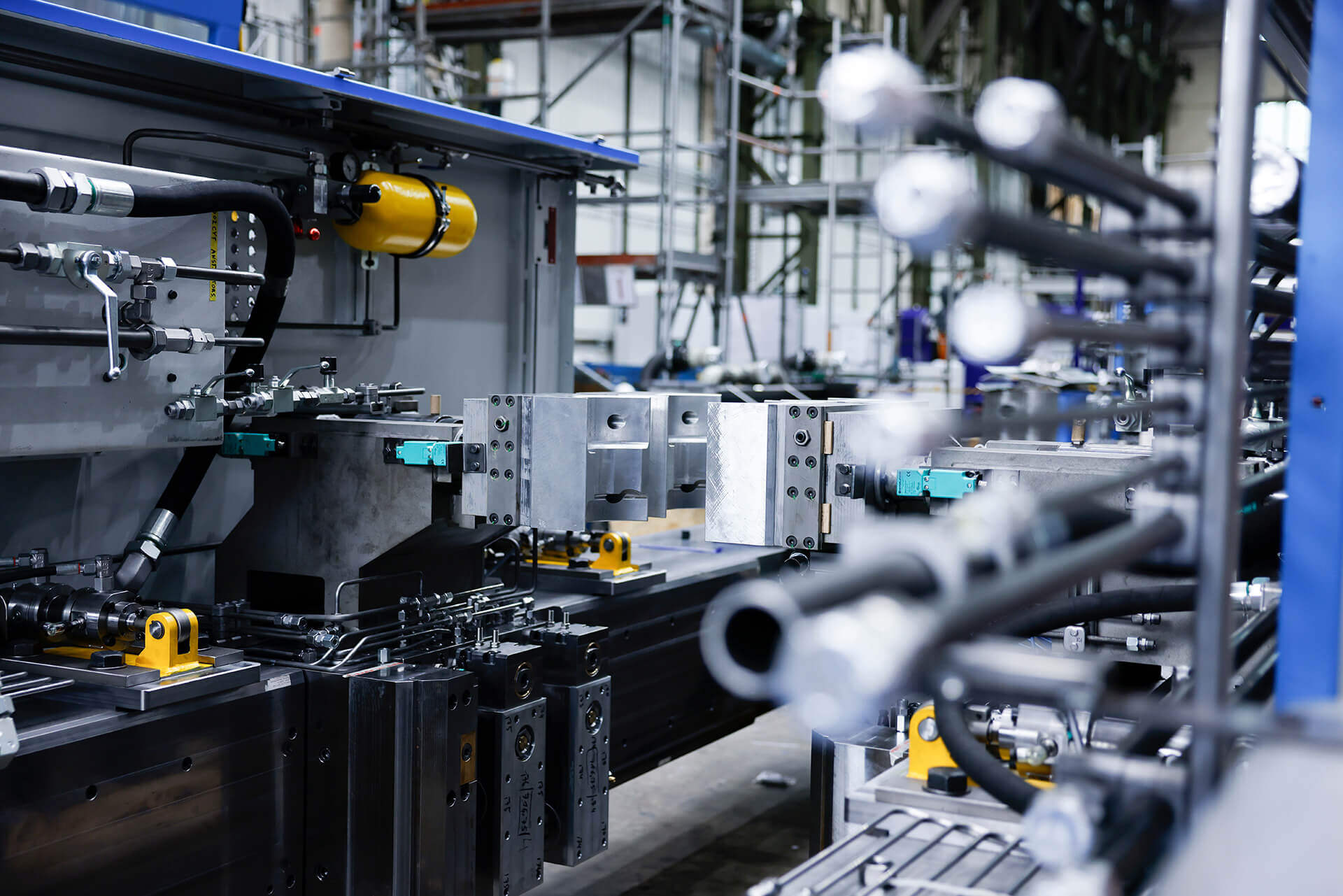
Quality management systems or quality systems is a structured way of working with quality, deviations, and continuous improvements within an organization. The purpose is to ensure that a service or product meets the requirements set by customers, management teams, and industry regulations.
Quality systems in practice
A Quality management systems (QMS) can take many forms. Sometimes it’s a binder on a shelf or a shared folder on a server where routines and instructions are stored. Other times, it’s part of a cloud-based solution – like a digital management system – where you can visualize processes, manage documentation and deviations, and clearly assign responsibilities.
ISO 9001 Certification
ISO 9001 is an international standard for quality management systems. It provides a framework for working systematically with quality and continuous improvement. To become certified, an organization must meet a set of requirements related to leadership, customer focus, processes, and follow-up. Certification shows that you take quality seriously – both internally and towards customers and partners.
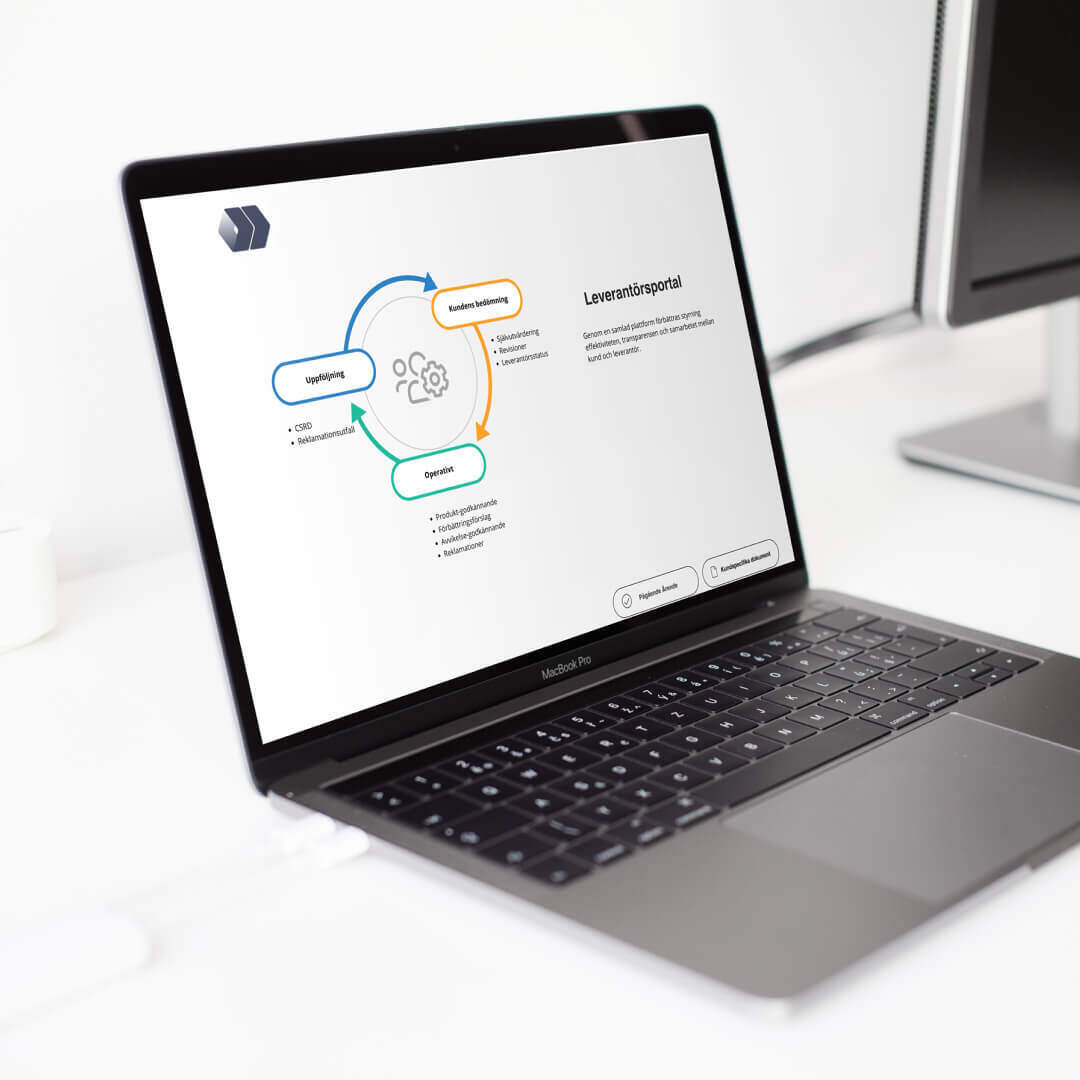
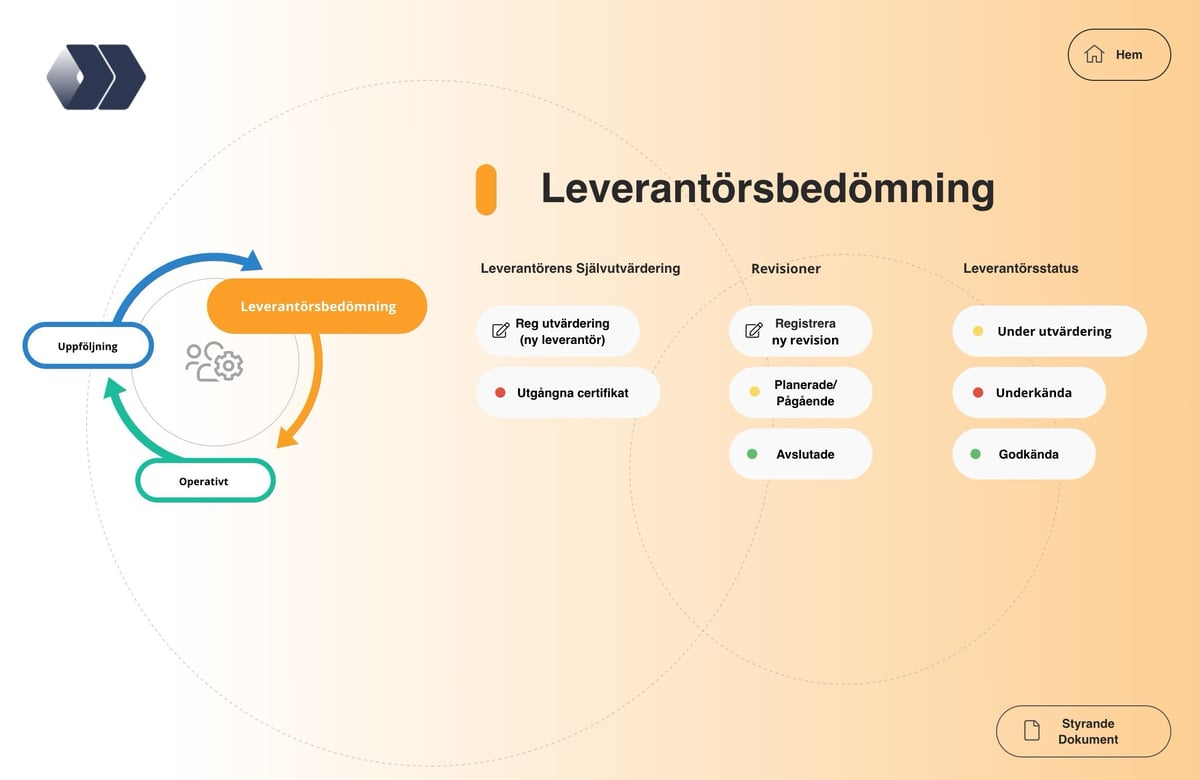
Example of a supplier portal and supplier evaluation dashboard created in AM System. Visually intuitive and clickable for users.
Benefits of a digital quality management system
- Clear overview: Centralize your processes, documents, and responsibilities
- Better control: Easier to follow up on goals and prioritize actions
- Resource efficiency: Identify where efforts and time are most needed
- Drive improvement: Track, analyze, and continuously improve
- Data-driven decisions: Access traceable data and clear reports
Make it easy to do the right thing
Discover how AM System helps you bring structure to processes, documentation, and workflows.


Example from AM System. Users get a visual and clickable overview of key areas such as improvement suggestions, incidents, internal deviations, and 5S audits.
Do we need a quality management system?
Everyone who delivers a product or service has different goals and requirements they want to meet, to be a profitable, competitive and sustainable business.
Through a quality management system you can:
- Work on continuous improvement, by also demonstrating the improvements you make by comparing with the previous year.
- Map your working methods and processes, so that all roles, responsibilities and activities are clear to everyone.
- Document and manage your procedures, guidelines and policies.
You will avoid forgotten post-it notes, emails circulating internally and improvement suggestions that never materialize.
What requirements do we need to meet?
Always start by looking at your different requirements and build on them. Your requirements can come from, for example
- Regulations and legal requirements
- Your own quality requirements
- Contracts
- Requirements or certifications from external stakeholders
- Customers' needs
ISO 9001 certification
For some industries, there are requirements for quality management to follow a set standard that allows organizations to become certified to that standard. These standards allow organizations worldwide to follow the same guidelines and together ensure that their customers and stakeholders receive products and services that are safe, reliable and of high quality. One such management system standard for quality management is ISO 9001, where procedures can include everything from customer care to having a plan for solving practical problems such as malfunctions or complaints.
Thus, one or more certifications in ISO standards may be a requirement for some organizations, while it can also be a competitive advantage. A quality management system signals that you take your tasks, laws and guidelines seriously and are willing to continuously improve.
Implementing a quality management system
1. think about how the work itself will be done
What does it look like in your organization? Who is responsible for which parts and who needs to be involved in the quality management work?
2. embed, embed, embed
To succeed, you need to share responsibility and help each other. Participation from the manager and the management team is extremely important, as is anchoring with other employees. Everyone will be involved to a greater or lesser extent.
3. Appoint project team and project manager
A project manager is needed to lead the work. This person should be a good communicator and have experience in managing both processes and people. Think about why you are doing this work and define the purpose and objectives. Here you will benefit from the different requirements you want to meet.
4. Work together and map your current situation
Set aside time for some initial workshops to map out how you work today. Think about risks in the different stages of your operations and highlight areas for improvement.
5. Visualize your processes
Identify your main process and complete it with your different sub-processes. Draw and visualize your operations as clearly as possible. Here you can divide the work and start with priority processes, and then gradually expand.
6. Relate and supplement with documentation
What documentation do you have today to support your processes? Does it need to be supplemented? Relate the processes to governing documentation in the form of instructions, guidelines and policies.
7. support with case flows
Think about which activities can be supported with digital case forms, forms and checklists. With simple and clear case flows, you ensure that the work is done in the same way every time.
8. think about the end user - keep it simple
Lower the threshold to use by introducing the system as early as possible, and successfully build on it with more content. And create home pages for your different user groups, corresponding to their needs. For example, a production department. They are unlikely to need to see a home page with both the main process and sub-processes, but are more helped by quick shortcuts to the documents they need to read and the cases they register.
9. capture improvements and develop
Listen to your users regularly. What can be done better and more clearly? Are there still paper forms out there that could be integrated into the quality management system? Take the chance and include as many elements as possible. This way, the quality management system becomes a daily tool for both management and employees.
AM System as a quality management system
Not all quality work is done from an office by one person. Rather, it is a way of working that should permeate everything and everyone in an organization.
Therefore, accessibility becomes important
AM System is completely cloud-based and accessible no matter where you work from. With rights, you control who can see and do what in the system. And in which language. AM System is available in Swedish and English and supports more languages.
Therefore, it should be malleable
Quality work is about continuous improvement and therefore a quality management system should be living, not static. AM System is easy to adjust, update and supplement based on your needs.
Therefore it should be user-friendly
The quality management system should make it easy to do the right thing. With AM, you can creatively map out your processes and ways of working, document and create automation that ensures that everyone works in the same way and towards the same goals.
Why your data is valuable to you
By systematically measuring, analyzing and correcting what happens, you create continuous improvement. The data collected in the quality management system thus becomes an invaluable strategic tool for you.
Get a demo
Ready to make work easier - and more enjoyable?
Want to see for yourself how AM System can make a difference for you? Request a demo and discover how easy it is to create structure, efficiency, and seamless workflows in your daily operations.
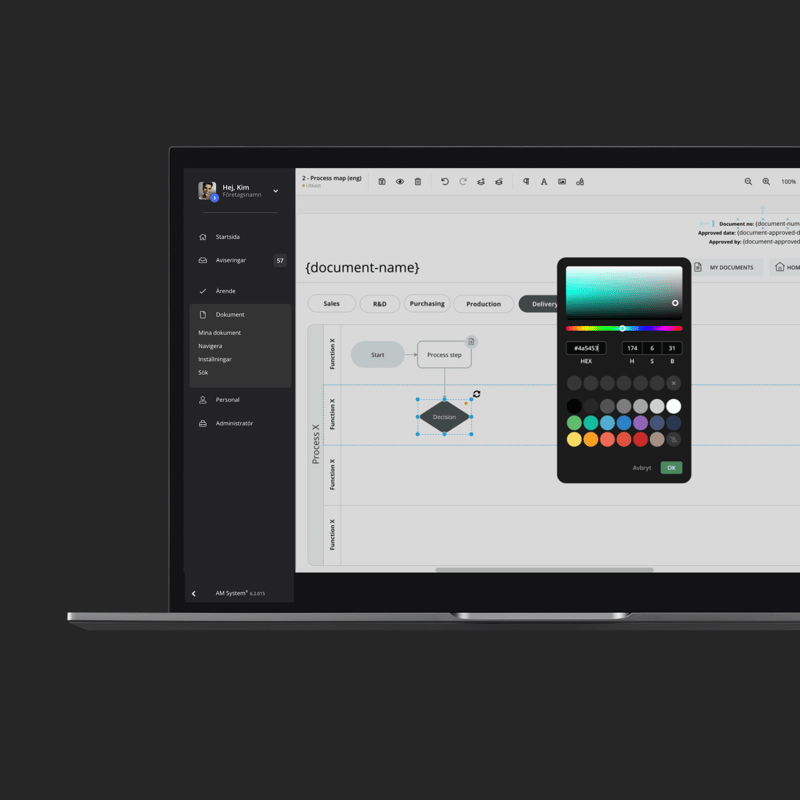