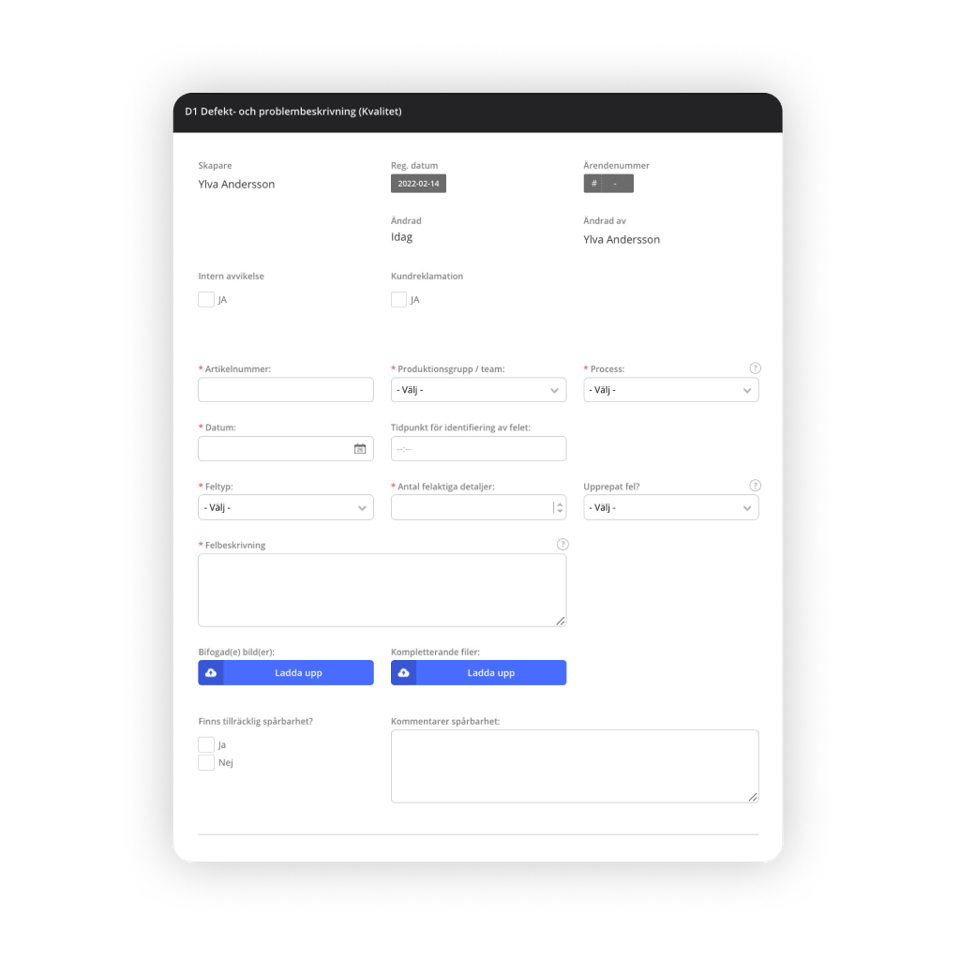
Planning and identifying the problem
Start by clearly defining the problem. Add fields and questions such as:
- Create checklists for sorting: Develop digital checklists that employees can follow to categorize and organize workspaces.
- Document and track decisions: Use case management to log decisions about what to retain or discard.
- Visual follow-up: Capture and upload images to document changes in work environments.
This step can also include fields for temporary corrective actions and identifying similar problems elsewhere in the organization. Notifications ensure that the right people are alerted immediately, keeping the process on track.