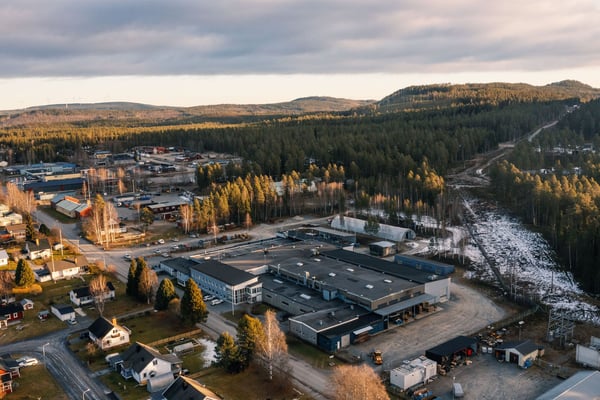
OptiPack uses AM System for its systematic work environment management
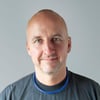
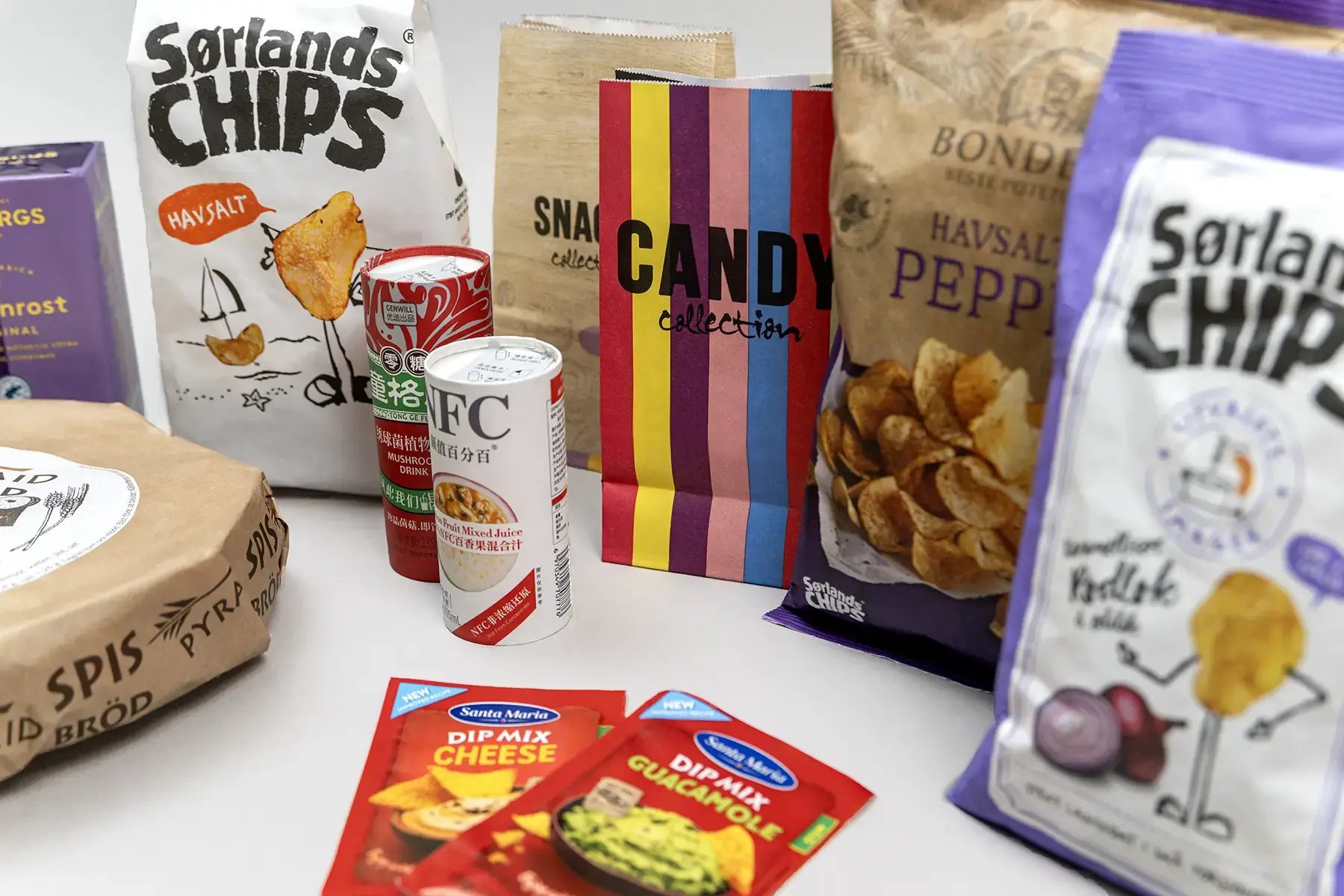
Today, OptiPack has over 6,000 days without serious accidents thanks to good control of the work environment, safety rounds and machine protection. Here you can read about how the company uses AM for its systematic work environment management.
OptiPack has its production facility in Sunne in Värmland. The company has been around since 1939 and is today a leading player in the Scandinavian packaging market, supplying industries such as food, transportation and construction.
Quality and Environmental Manager at OptiPack is Niklas Persson, who is one of those whose everyday life has become easier with the help of AM System.
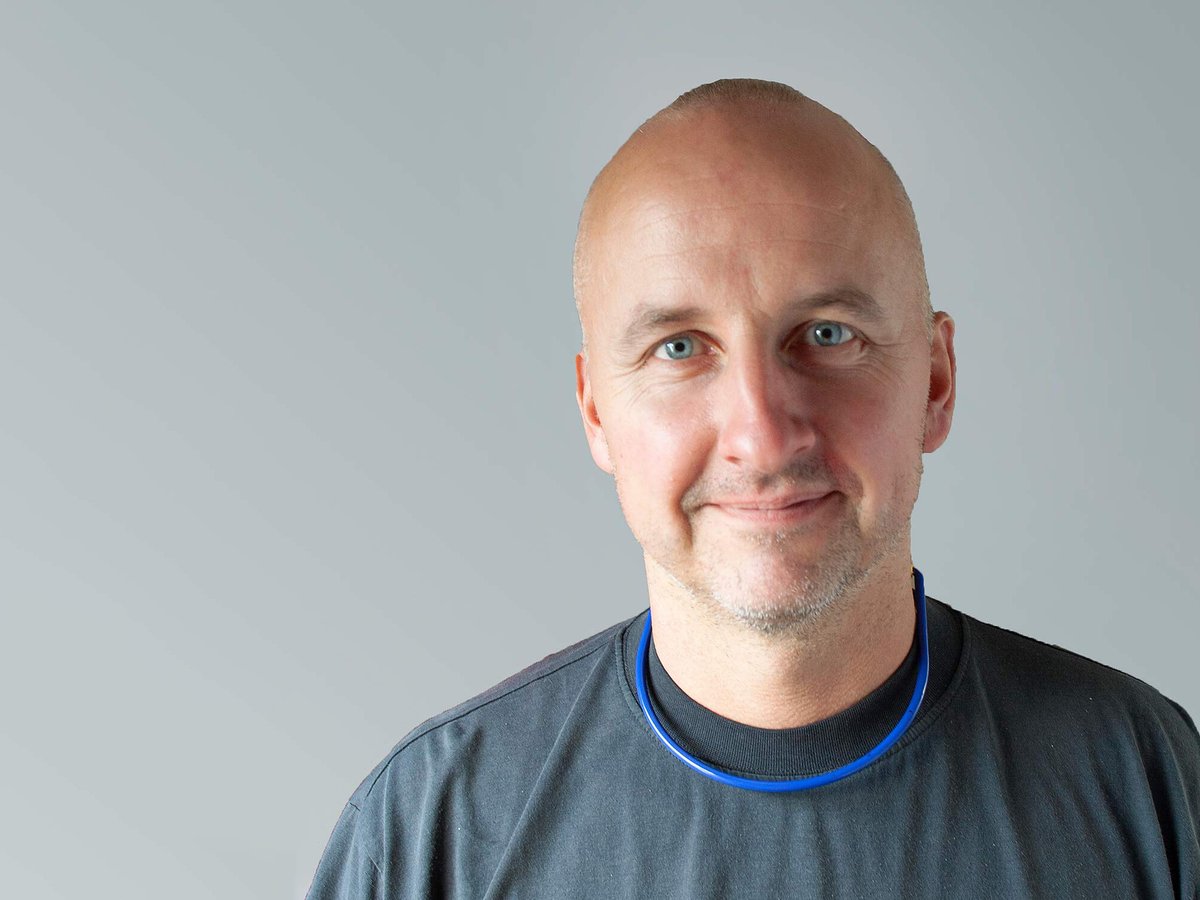
- Before we got AM, we had all our work environment procedures in paper format, says Niklas.
- The action plans we had from work environment meetings, safety committees and safety rounds and so on were each in an Excel sheet in different places distributed on two servers, which meant that rarely did anyone know where the right file was or when we needed to perform an action. Often we simply forgot to go in and implement it.
It was time to do a do-over
Over time, a huge back catalog grew up with things that should have been done, and which only came to the surface when it was time for an audit once a year. But as Niklas took on more and more responsibility for quality and the environment, he began to look towards AM System as a way to become more systematic in his work environment management.
"The system helped me to get it in black and white, who would do what and when"
- I felt it was time to move everything to one place. So I started putting in work environment meetings, safety rounds and risk analyses. I created lists to find out which risks are the most dangerous for us, while the system helped me to see in black and white who would do what and when.
A necessary overview
AM System became the service that gave Niklas an overview of the most important parts of OptiPack's work environment management, and over time they began to use more and more of the system's different parts.
- Today we use AM System for a lot of things. Among other things, we use it for incident reports and to regularly test that the emergency stops on our machines work. That kind of work is incredibly gratifying to do when you have a system that reminds you.
Another function in AM System that has become important to Niklas is the process map. Partly because it is more or less a requirement to have a good process map to comply with ISO 9001.
- We need a process map that explains the input and output of our main processes, says Niklas. But then it's important for all our operators. It's so much easier for them to find their way around when they log in and are greeted by a clear process map from which they can enter things like new maintenance and new cases. Then they have all the processes, policies, instructions, job descriptions and everything else they need that has to do with safety. Being able to get this up with a few clicks is very smooth.
Before the health and safety meeting and safety committee
Another feature in AM that has become important to Niklas is date fields with triggers.
- We have a work environment meeting twice a year and a safety committee twice a year. Before these, for example, I need to do a safety round where you go around all the workplaces and ask how the employees experience the work environment. This should be done before the work environment meeting.
With AM System, Niklas can enter the date of the meetings in the system and receive automatic reminders two weeks before, for both himself and others involved who need to do, for example, safety rounds.
- For me as a coordinator, it makes a huge difference now that the system can do so much on its own. I don't have to remember to send out the right information to the right people and make sure that everyone really gets what they need.
Once Niklas has set up a good routine for something, such as health and safety committee meetings, he can also reuse the routine in the future. This way, he eliminates the risk of things being forgotten.
A safer workplace
- Today we have about 30 different cases in AM System and I feel that nothing falls through the cracks anymore, Niklas explains. No one needs to sit and think about when something should be done, the system takes care of everything. Simplicity is the big positive thing for us.
Today, everyone at OptiPack uses AM System. Initially, there were only a few users with a common login, but soon they saw the benefit of individual logins so that everyone could be responsible for something. Now anyone can go in and make digital signatures on checks, for example, instead of doing it on a piece of paper that has to be archived for a certain number of years.
Another effect of using AM for systematic work environment management has been that Niklas can easily extract statistics from the system.
"If the Swedish Work Environment Authority comes and asks how often we carry out a certain inspection, I can find out exactly what it looks like.
- Then I can easily do follow-ups and take out the right graphs to show the management at the recurring meetings where I need to do it.
It is now over 6,000 days since OptiPack had a workplace accident that meant someone had to stay home from work, even though it is a relatively dangerous industry.
- We have such good control of the work environment, safety rounds and machine protection today that we are doing well," concludes Niklas.
READ MORE
Related case studies
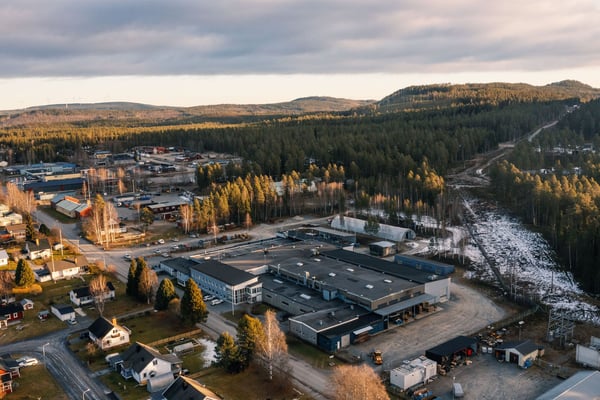
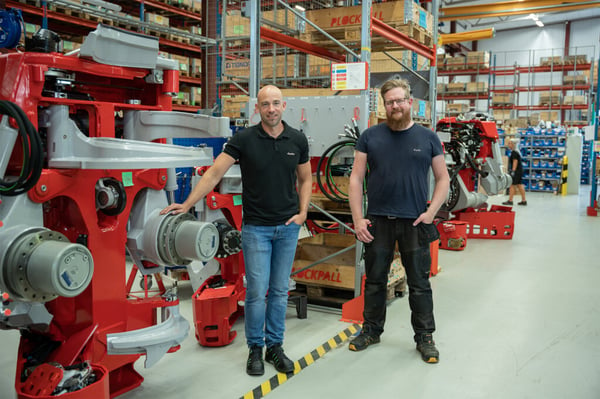
Case Studies
Log Max harvests success worldwide – chose AM System for their entire quality management system.
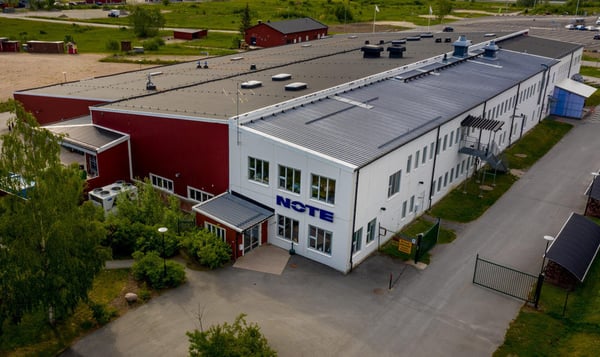
Case Studies
How NOTE ensures efficiency and ISO compliance with AM System
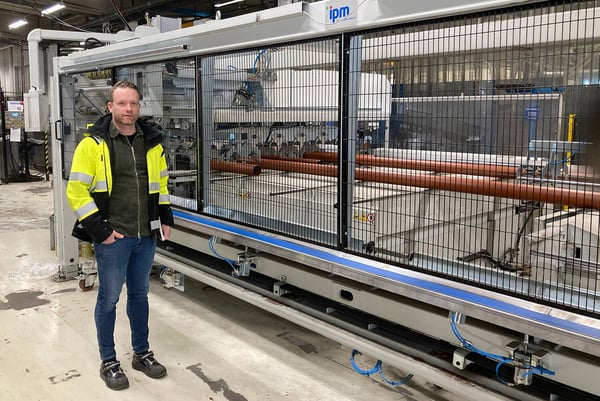
Case Studies
Pipelife saves money and time with AM System
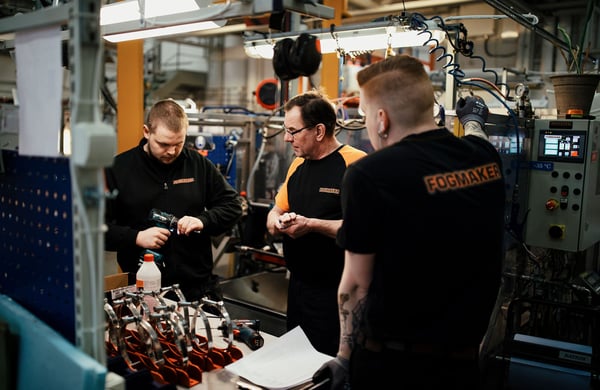
Case Studies
How Fogmaker uses AM System to meet its own requirements
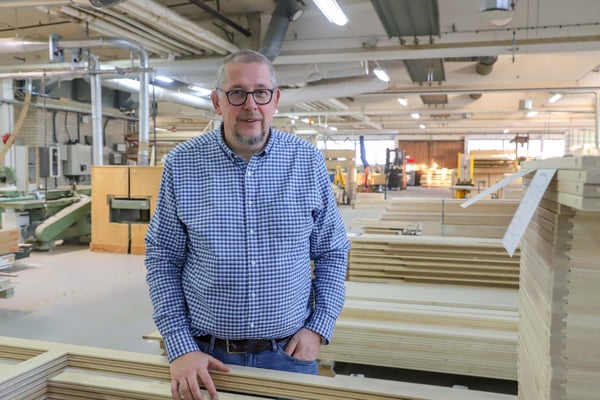
Case Studies
Enably aims for ISO certification and brings together the entire management system in AM System
Request a demo
Ready to make work easier and more enjoyable?
Want to see firsthand how AM System can make a difference for you? Request a demo and discover just how easy it is to create structure, efficiency, and seamless workflows in your daily operations.
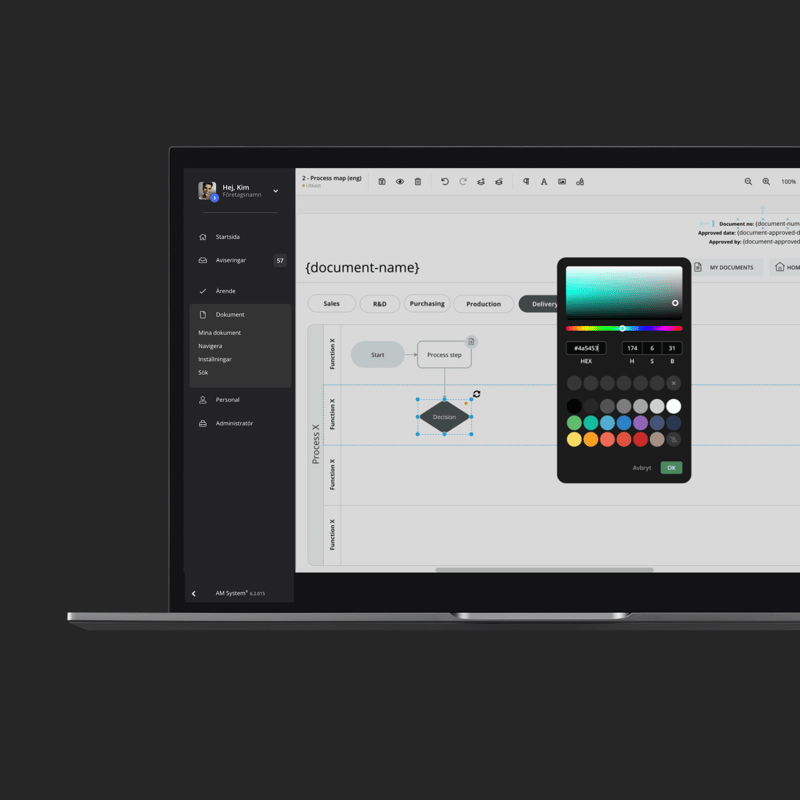