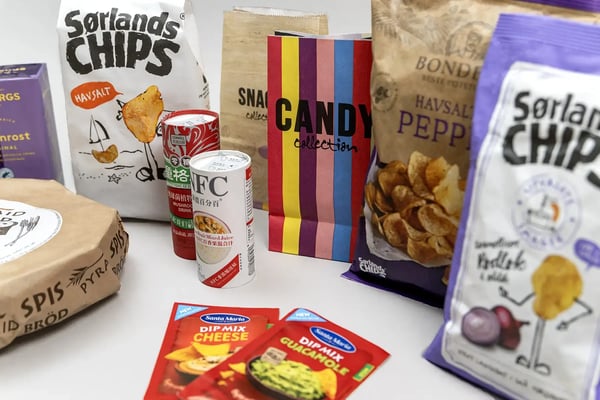
Log Max harvests success worldwide – chose AM System for their entire quality management system.
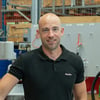
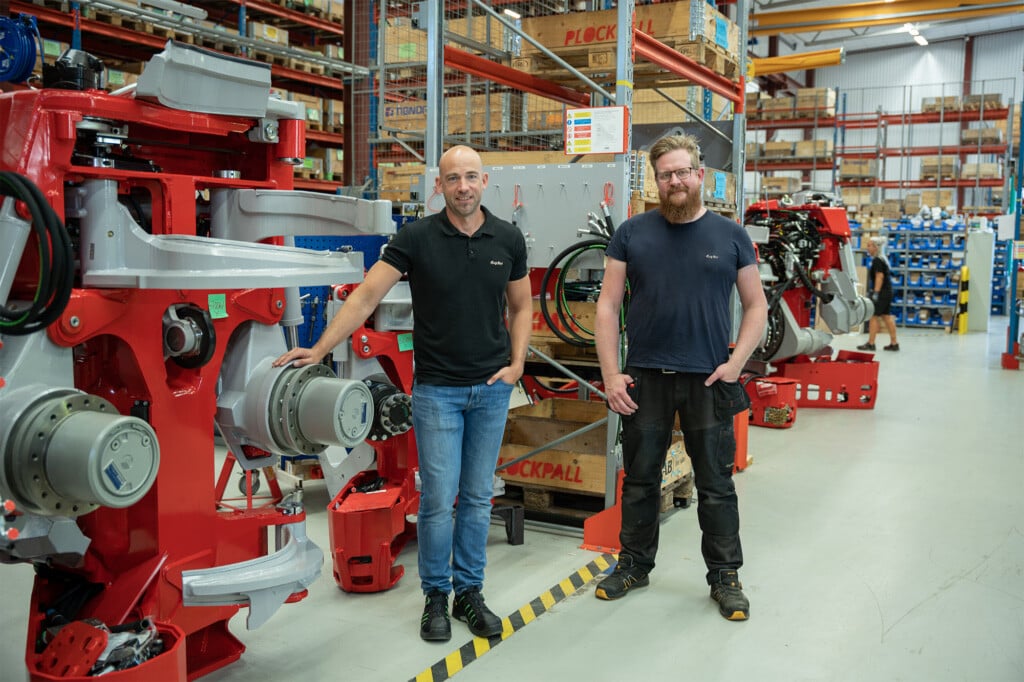
- 13
models of harvester heads
- 484
harvester heads manufactured in 2021
A harvester head needs to fell, delimb, and cut trees—deep in inaccessible terrain. This is a product area where Log Max, based in Dalarna, Sweden, has made a name for itself as a reliable supplier. Here, they share their approach to quality management and how they have integrated processes, their quality management system, and workflows directly into AM System.
Founded in 1980 in Grangärde, just outside Ludvika, Log Max was a privately owned company for many years. Last year, the company produced 484 harvester heads of various sizes—ranging from the smallest, weighing around 400 kg, to the largest, exceeding 4 tons. In total, they offer 13 models tailored to different forest environments.
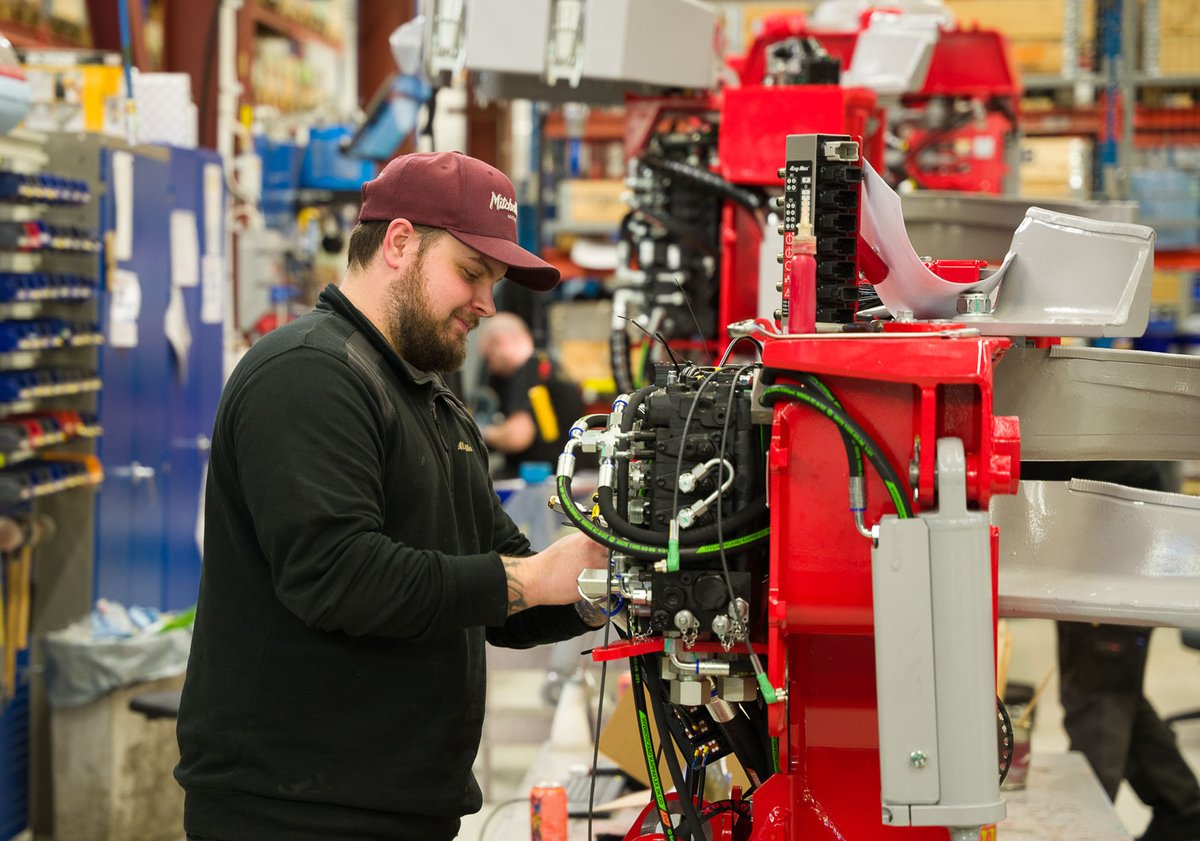
Log Max products are sold in various countries through distributors and in-house agents. The company’s primary focus is on design, engineering, and assembly. All parts are subcontracted to manufacturers and then assembled by Log Max, which was acquired in 2012 by Komatsu Forest, a publicly traded global corporation.
From scattered folder structure to unified platform
Log Max has been ISO 9001 certified for many years. Previously, their quality management system was housed in a separate Wiki site, which felt difficult to update, navigate, and search within. Johan Ericson, Head of Engineering, began looking for a suitable platform to manage processes, cases, and documents.
- We used to manage change notifications in Excel documents, which were then sorted into folders. I had previous experience with AM System’s case management module from another company and knew it could solve many of our challenges. However, I had never worked with their document management module before. So, we conducted a thorough evaluation and ultimately chose AM System for its comprehensive solution, Johan explains.
"Today, we have an incredibly clear overview. In fact, we proudly showcase AM System to visiting customers and highlight the advantages it gives us.”"
Seamless implementation at an affordable cost
During their evaluation, Log Max found that many other system providers had high startup costs and limitations.
– Some required hundreds of thousands of kronor in startup fees and came with locked templates that we couldn’t modify. With AM System, we got a low startup cost, short implementation time, and flexible templates for both documents and case management, Johan explains.
After a few training sessions with an AM System customer success manager, Johan began mapping Log Max’s processes, uploading governing documentation, and designing case workflows.
Log Max main process, visualized as a swimlane model, directly in AM System
The importance of collaboration and management commitment
Johan is part of Log Max’s management team and has experienced strong support from leadership throughout the project—a crucial factor for success. Early on, he also involved his colleague Fredrik Fröst, a production technician. Together, they built case workflows and trained staff internally.
– “With version 6, the ability to draw our processes directly in AM System has been a major upgrade. Previously, we used a separate program for visualization, which then had to be renamed, saved, and uploaded. Now, everything is in one platform,” Johan explains.
"Each department has their own customized start pages where they access everything they need for their work and can easily navigate further.."
- These homepages, assembly instructions, work descriptions, and case workflows have been my main focus, says Fredrik.One of several different start pages - this one for Production
A system with many use cases
Today, Log Max has integrated all governing documentation into AM System and has created structured forms for deviations, complaints, incidents, and accidents. The system is also used for test protocols, incoming goods inspection, customer visits, export controls, international travel applications, and much more.
– For the Elmia Wood trade fair, we set up a form to register visitors who wanted follow-ups—right from tablets. This resulted in a structured overview for sales teams to conduct efficient follow-ups, says Johan.
Another example is “100-hour cases”, registered when a customer reports issues with a harvester head within 100 hours of delivery. These issues are often production-related, and by separating these cases, Log Max can quickly identify if a problem stems from manufacturing or assembly.
"With AM System, we have gained an overview that we previously lacked. Now, it’s easy to track and prioritize cases."
- Then, of course, it is important to supplement the work done in the system with physical meetings and reconciliations. This means that we create an understanding between different processes and get a consensus on what can be improved, Johan explains.
Log Max construction process, drawn in AM System
Strong understanding of the customer in the forest
After an interview with Log Max employees Johan and Fredrik, it becomes clear that the company's success is based on high technological competence combined with a strong understanding of customers' everyday lives. In Sweden, we are spoiled with a well-developed internet connection, but it is far from everyday life for Log Max end users.
- Our products are installed on machines in difficult-to-access environments, where access to roads and digital infrastructure can be severely limited. In some places, there is no internet connection and it can take several days to reach a telephone network. So it's important that our products work. Unexpected downtime can be extremely costly, says Johan.
A wide range of expertise
Although Log Max may seem to operate in a traditional industry, the company spans a wide range of disciplines. In Johan's department alone, there are employees in hydraulics, mechanics, mechatronics, control system development, technical documentation and communication.
- All of them are specialists in their field and work together to achieve the best possible end result. It's both a thrill and a challenge. In addition, we are stationed in different locations, so access to correct documentation and clear workflows is crucial for everything to work, says Johan.
Global player with a local focus
Today, Log Max harvester heads can be found in forestry operations around the world. At the same time, the company is focused on working with local subcontractors as far as possible. Between 35-40% of all parts are manufactured within a ten-mile radius of Grangärde. Similarly, the company's technical development is closely linked to their own competencies.
- We sell on quality and a well-engineered product. Our competitors are good, so we have to be at the forefront. What's important to us is a robust and simple design with smart technical solutions that provide high utilization and low fuel consumption. This helps our customers to be successful, concludes Johan.
Johan Ericson and Fredrik Fröst at Log Max
Areas of use
-
Process visualization
-
Governing documentation
-
Case workflows for deviations, complaints, incidents, and accidents
-
Test protocols
-
Incoming goods inspections
-
Customer visit tracking
-
Export controls
-
International travel applications
-
100-hour cases
-
Trade fair visitor registrations
-
Customers register complaints directly via AM System’s public link feature
Effects & results
- Less software needed when we handle more in AM System
- Fewer emails and scattered documents in Word and Excel
- We increase quality by getting a better overview of changes in production
- Easier to find what you are looking for in the management system as a whole
- We get shorter communication channels and thus become more efficient
READ MORE
Related case studies
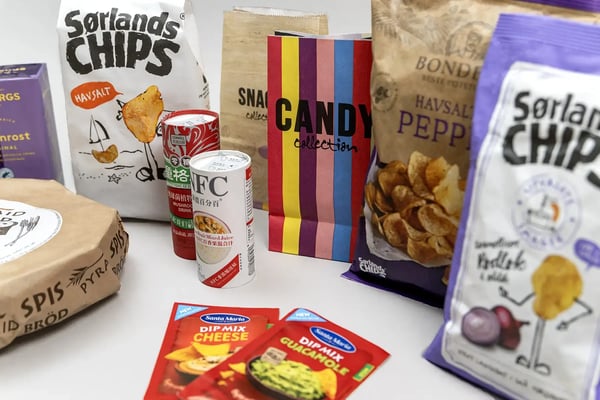
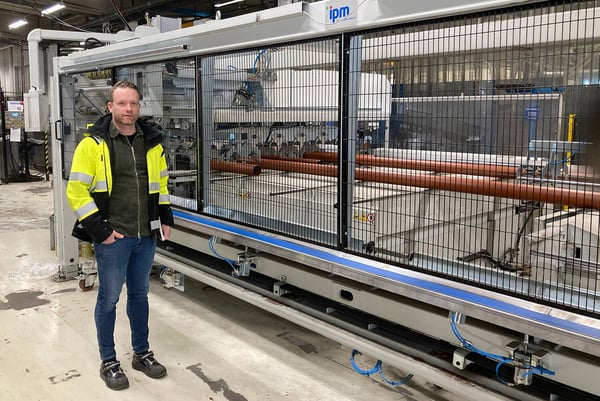
Case Studies
Pipelife saves money and time with AM System
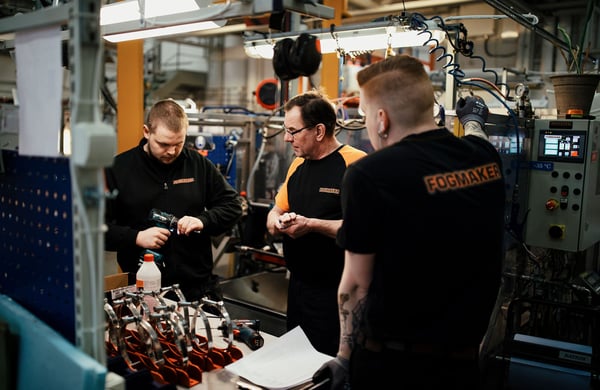
Case Studies
How Fogmaker uses AM System to meet its own requirements
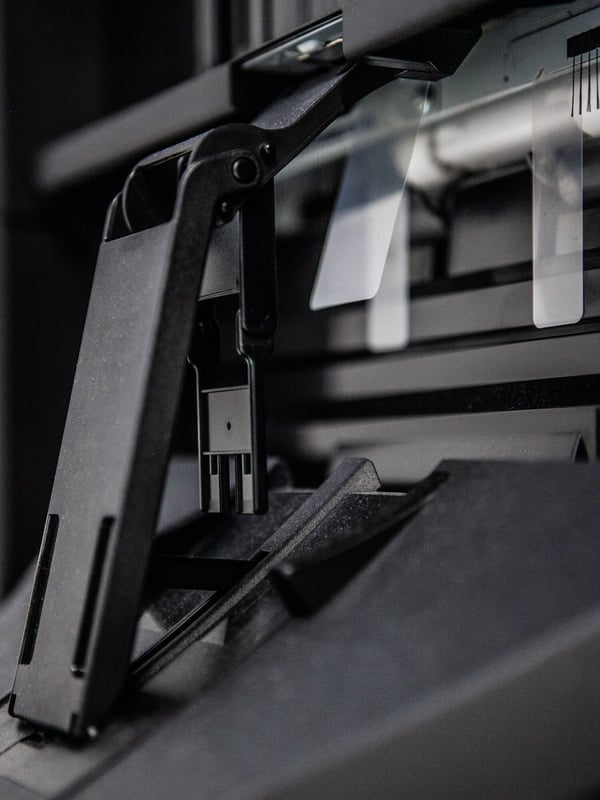
Case Studies
Matthews Marking System brought new life to it's QMS System
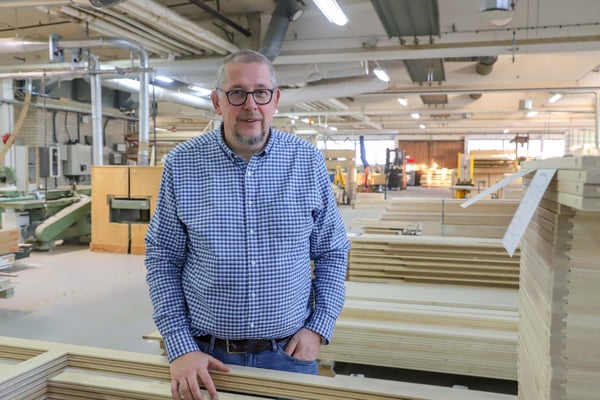
Case Studies
Enably aims for ISO certification and brings together the entire management system in AM System
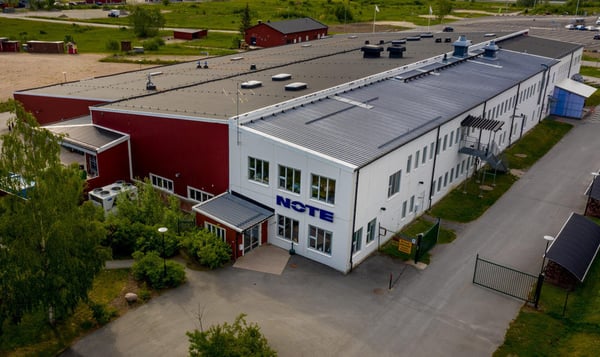
Case Studies
How NOTE ensures efficiency and ISO compliance with AM System
Request a demo
Ready to make work easier and more enjoyable?
Want to see firsthand how AM System can make a difference for you? Request a demo and discover just how easy it is to create structure, efficiency, and seamless workflows in your daily operations.
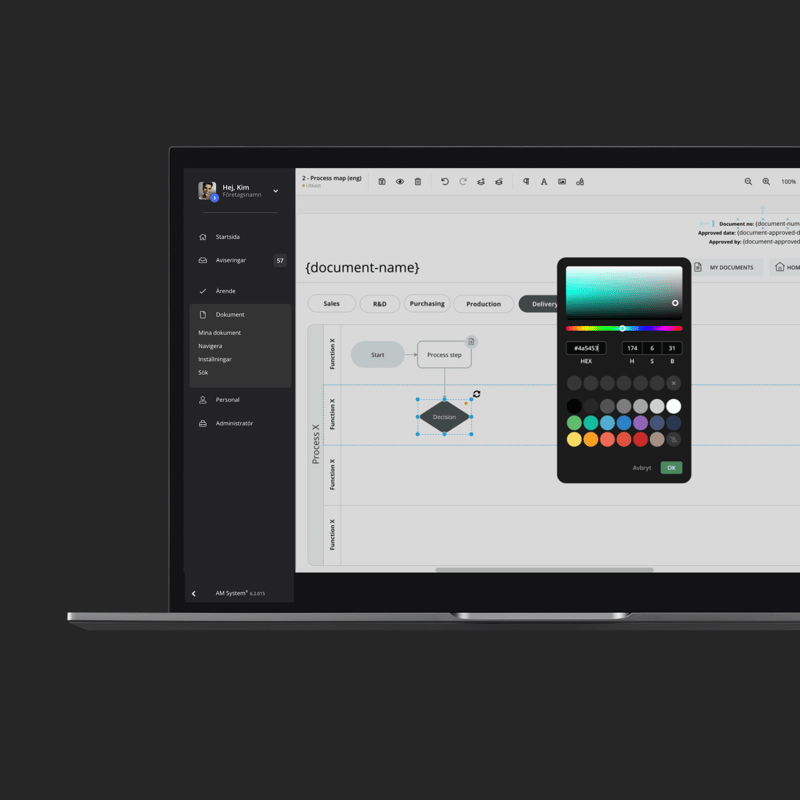