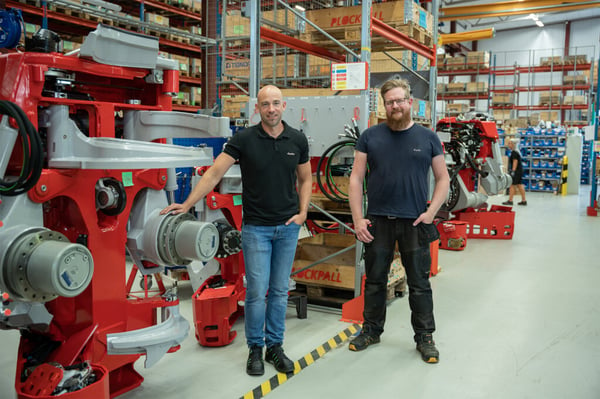
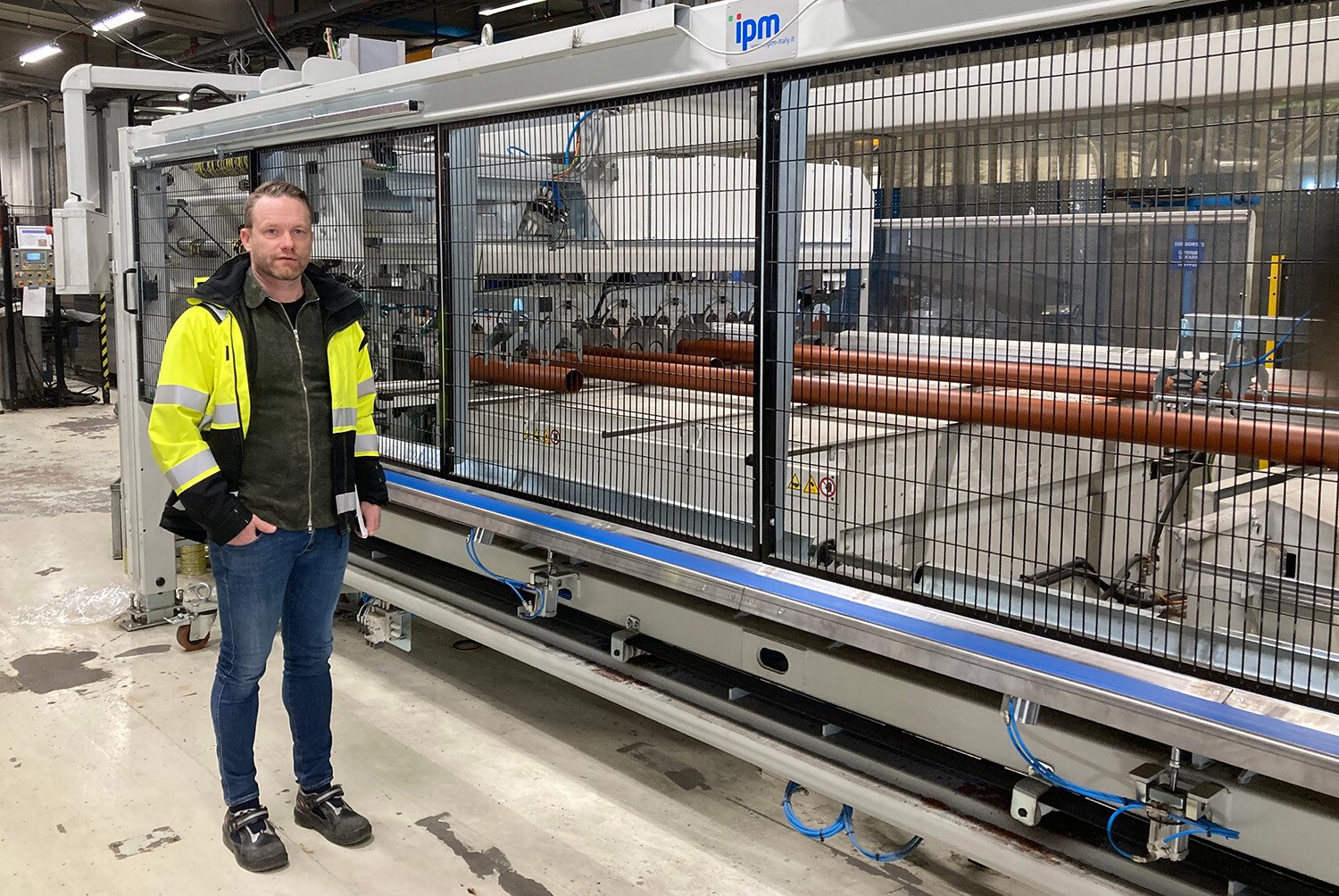
- 4
Times per year Pipelife is audited by a third party
- 190 000SEK
In reduced licensing costs, just in the CRM system.
- 30
Days saved on a single deviation.
From manual handling and multiple systems to digital processes and case flows. This is the journey Pipelife has made with AM System. Internally, the new ways of working are welcomed and there are clear effects in both time and cost savings.
- We have become more efficient as a company and made great savings with AM. So the introduction has paid off several times over, says Tommy Säll, Quality Manager at Pipelife's factories in Ljung and Ölsremma.
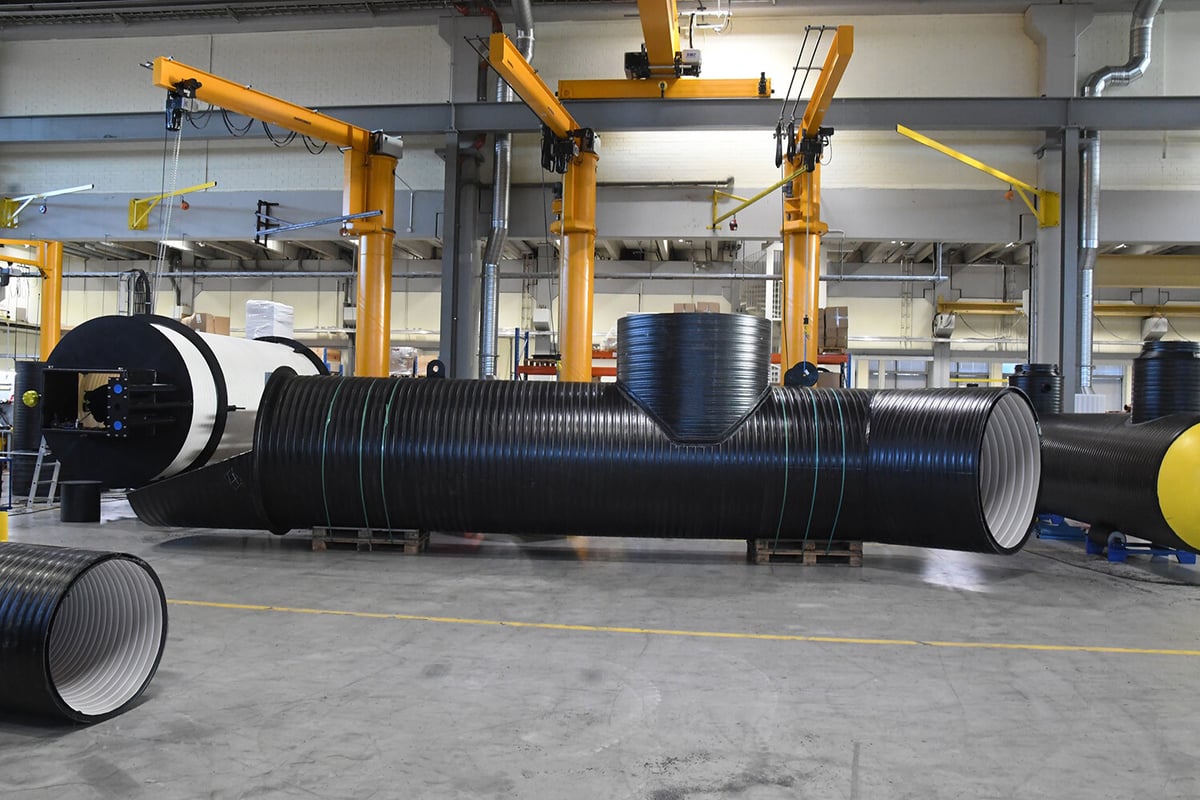
A leading plastic pipe producer
Pipelife manufactures various types of plastic pipe systems, with extrusion and injection molding as the main technologies. The products allow water to flow safely, in water mains to and from waterworks. It also manufactures products for conducting water in domestic environments and various protective pipes for cabling. In the production lines, plastic material is fed in at one end and plastic pipes for various needs come out at the other. The customers are industrial wholesalers and the end users are public utilities around Sweden.
The Pipelife International Group is represented in 26 countries with 26 factories. The headquarters are in Vienna, Austria, where the decision on AM System finally landed.
The importance of internal support
Tommy had experience of AM System from his previous workplace Mastec AB and compared it with other systems when he joined Pipelife.
- I was full of enthusiasm and wanted to get started quickly, but had to re-evaluate and involve more people. We are still 250 employees, so it was good to have a clearer anchoring before we started, Tommy says and continues:
- Case management was our top priority. We had different systems, some on paper, and needed to improve internal deviations, improvement suggestions and complaints. The latter was in our CRM, which was good for the salespeople, but the flow needed to get into production, where it belongs. And within the group there was nothing that suited our needs.
A visualization showing Pipelife's piping systems and product areas.
AM System reduced license costs in other systems
Pipelife works according to the Lean Six Sigma methodology. They created a project, described what they wanted to do, why and what improvements it could lead to. This made it easier to evaluate and get the go-ahead from the IT department in Vienna.
- It turned out that AM System would reduce our license costs in the CRM system by SEK 190 thousand. Just like that. And in a similar way, we have also reduced other license costs, says Tommy.
How did Tommy and his colleagues get started and how was it received internally?
- The advantage of AM is that you can get started very quickly. We mapped out our three priority case flows and trained department managers, who took it further in their processes.
"We went from manual to digital and employees find it easy to use"
Pipelife's complaint flow ensures that all information is recorded. Customer data, part number and name are imported from the SAP business system. The complaints are now processed correctly and saved for future analysis and conclusions.
Areas for improvement come to the surface
Pipelife launched the AM System in October 2020 and was the first to release 6.0, the latest version. Just over a year later, the results are impressive. They've digitized 12 different workflows, consolidated governing documents and created homepages for different user groups. In total, they have 140 licenses of which 30-40 employees use AM System daily.
"Case flows are now completely digital and paperless. Improvements are coming to the surface, saving both time and money"
The reporting of cases has also increased. From 90 to 220 improvement suggestions and from 340 to 697 deviations, when comparing 2020 with 2021. Areas for improvement are coming to the surface, saving both time and money.
- With everything digital, the statistics become clear and we get an overview to prioritize from. We have been clear that all internal deviations must be registered, even recurring ones. One example is a mislabeling we had on a type of pallet, which created major problems. A small but costly error, which meant that we had to drive back entire pallets and relabel. It is now fixed and we have saved about 30 working days, just on that action.Here is a dashboard that Pipelife visualized in AM System, with an overview of the entire improvement work. With clickable shortcuts to Completed, Ongoing, Not Prioritized and Not Feedback suggestions.
Tommy's favorites in AM System
- It is easy to get started and see results.
- The drawing tool in layout documents to create processes and clickable home pages for different users. Like 5S, what you need to see daily is easily accessible.
- The query builder that allows you to save specific queries and link to them from different homepages.
Easier to share information and collaborate
More uses are being added all the time. One such example is instructions and manuals that Pipelife previously managed in another system.
- Now we have made a template in AM System, which our technicians can use to create and publish their own instructions. It works really smoothly and I would appreciate that it would otherwise have taken us six months to get it right.
In the interview with Tommy, the simplicity of AM is emphasized and how well the system has been received. So you ask yourself, how did they go about getting such commitment?
- It hasn't just been easy and it's about finding people who are passionate about improvement. We have some new employees and leaders with valuable experience from Lean, among other things, so it's a joint job. But also fun. It is important to show the benefit, that something happens with what is registered.
Ready to introduce the entire management system
With Lean Six Sigma, Pipelife has created a systematic approach to its improvement work. And by reporting more and more in AM System, this work has been further strengthened.
- Now we are ready to bring the entire management system into AM. This is where our working methods and flows will be. We are looking at the structure for that work and will appoint process owners, who will be the driving force for their respective processes.
So it certainly sounds like there is reason to get back to Tommy to hear how the work is progressing. Because one thing is certain, at Pipelife they want to work together, for better management, digitization and continuous improvement.
Areas of use
Governing documentation, internal deviations, complaints, improvement proposals, audit deviations (internal audits, external audits, system audits, product audits), product testing, FAQ, preparation processes, incidents, safety rounds and risk management.
Data import
From the SAP ERP system, part numbers, designations and customer data are imported into selected flows in the AM System.
Measurable results
- Deviations and improvement suggestions have more than doubled in one year. Problems are coming to the surface and can be dealt with gradually.
- License costs in other systems have decreased by more than SEK 190 thousand in one year.
- Time savings on a single fixed nonconformity: 30 working days
Pipelife Sweden
- Factories: Ljung and Ölsremma in Västergötland
- Product range: Land drainage systems including manholes, drainage systems, infrastructure systems, pressure pipe systems, indoor drainage systems, cable protection systems and infiltration systems
READ MORE
Related case studies
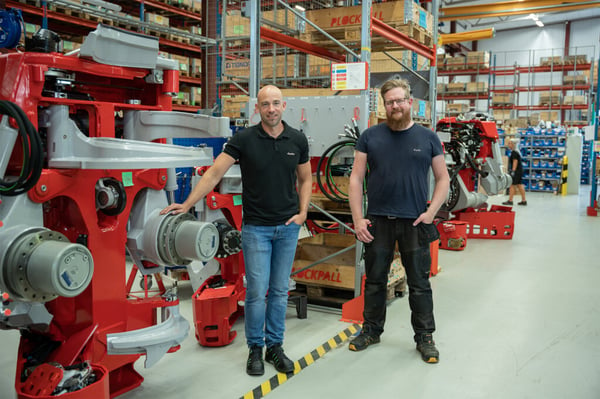
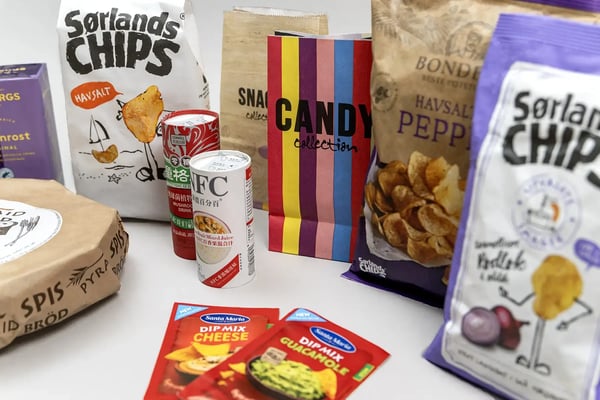
Case Studies
OptiPack uses AM System for its systematic work environment management

Case Studies
Fagerhult - a shining example of good onboarding
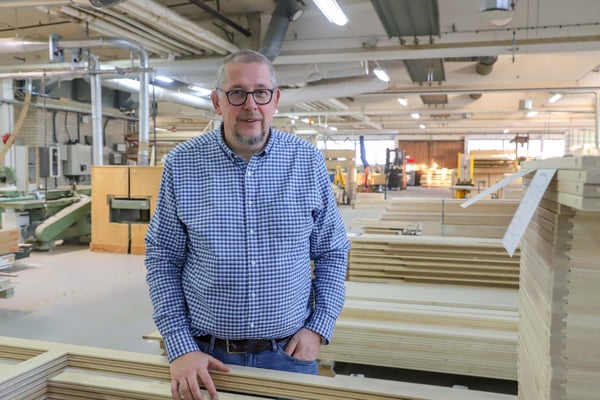
Case Studies
Enably aims for ISO certification and brings together the entire management system in AM System
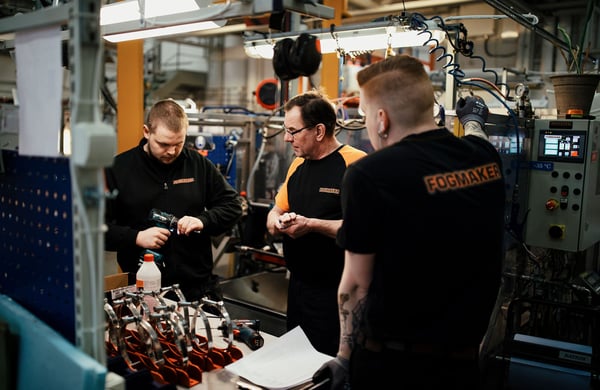
Case Studies
How Fogmaker uses AM System to meet its own requirements
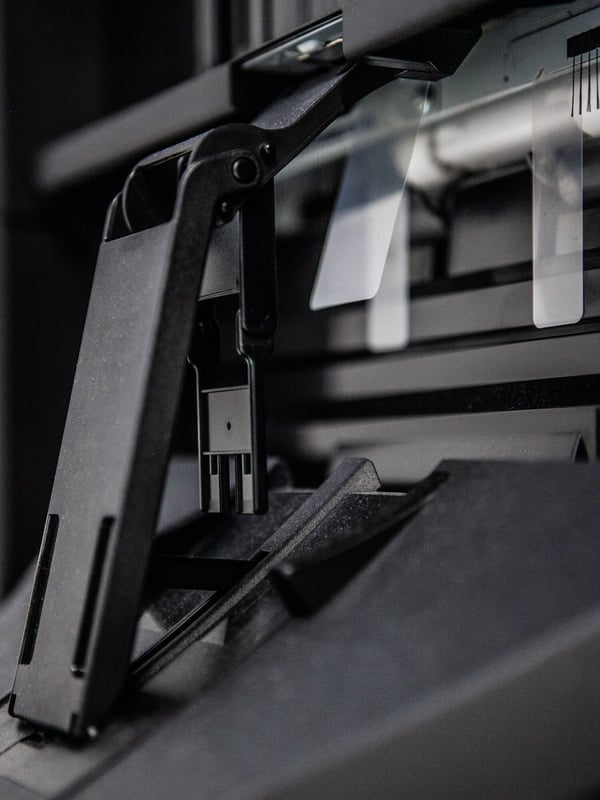
Case Studies
Matthews Marking System brought new life to it's QMS System
Request a demo
Ready to make work easier and more enjoyable?
Want to see firsthand how AM System can make a difference for you? Request a demo and discover just how easy it is to create structure, efficiency, and seamless workflows in your daily operations.
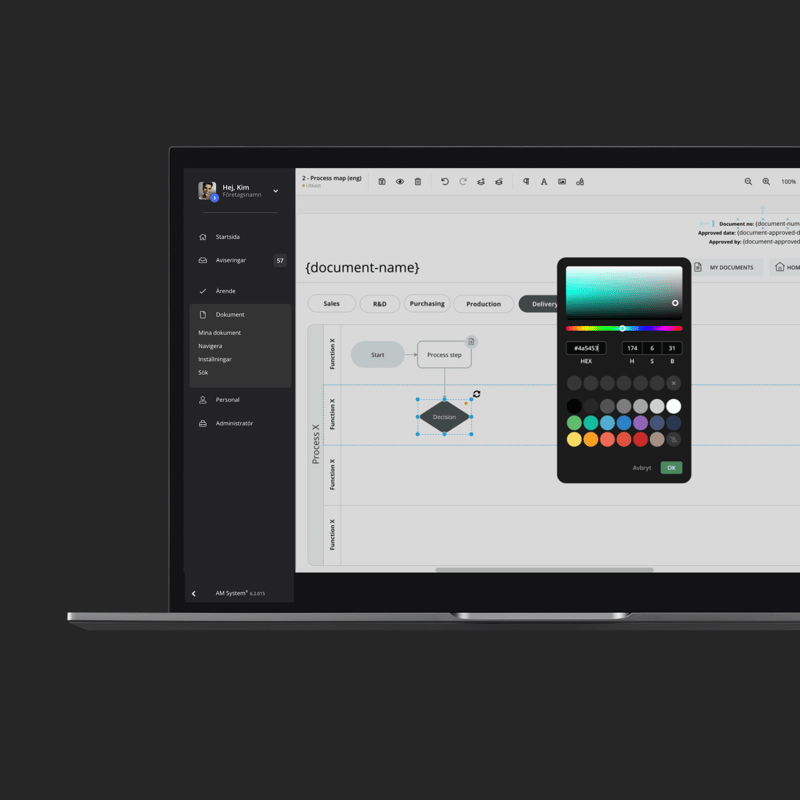