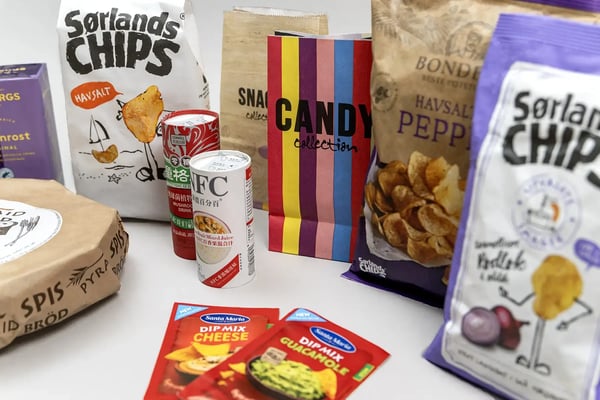
Enably aims for ISO certification and brings together the entire management system in AM System
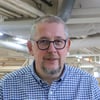
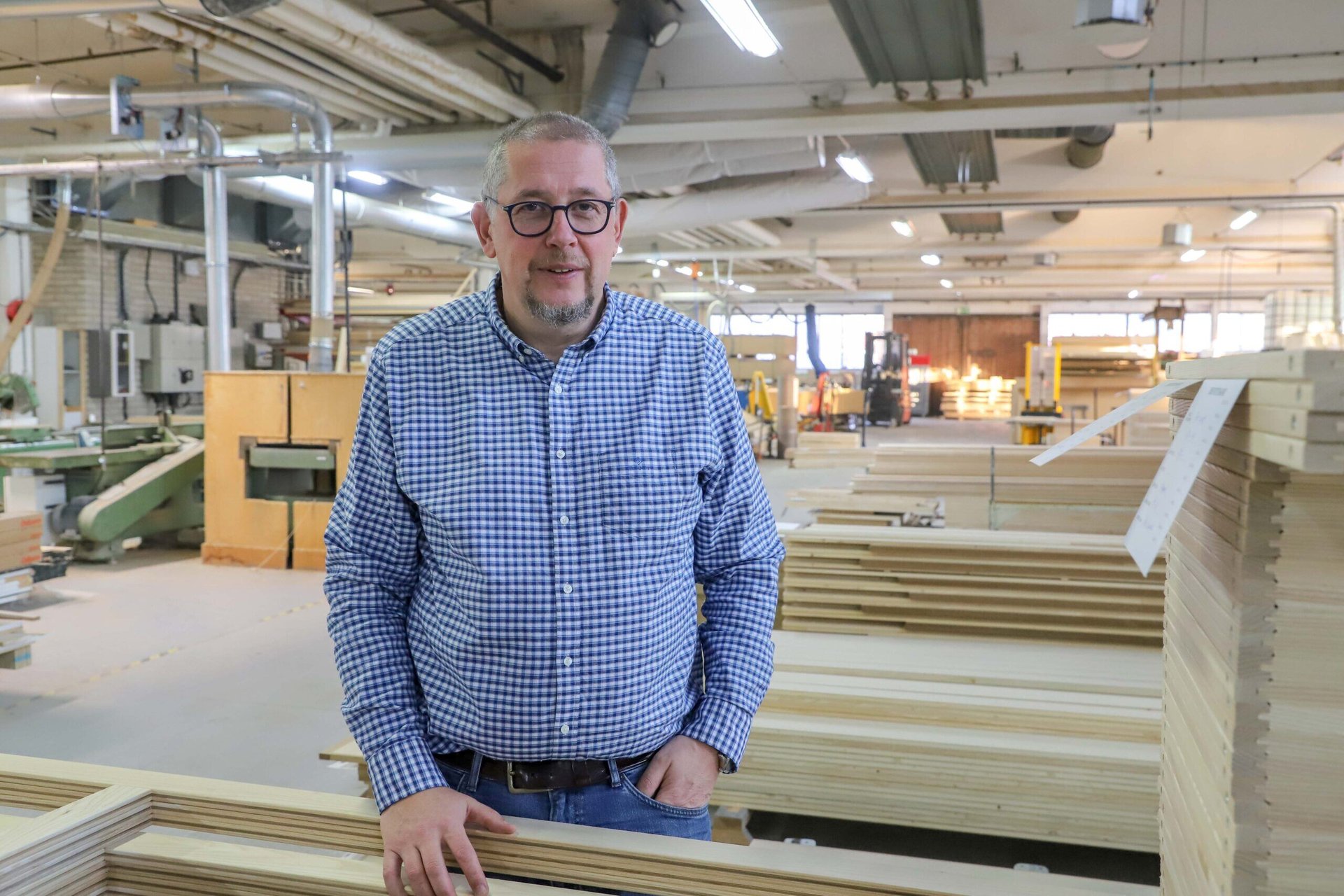
At Enably in Sävar, just outside Umeå, wood and metal parts are combined in innovative solutions. A specialty joinery with 50 employees who have ISO certification 9001 and 14001 in sight. AM System is the platform they have chosen to gather the management system and we took the temperature of the work with CEO Peter Forssell.
The family business Enably started in 1937 and for many years went under the names Sävar Snickeri, Sävar Metall and Sävar Industrihus. In 2020, the brands were streamlined into one Enably and in the same year the board decided to start work to achieve ISO 9001 and 14001 certification.
Peter Forssell joined Enably in 2019 as CEO/Chief Executive Officer and has extensive experience from service-producing companies and sales companies. At Enably, he has worked with business development, marketing and to realize the goal of ISO certification, which will complement their previous FSC certificate.
In AM System, Enably has visualized all their processes. Here is their main process, clickable and easy to navigate.
Wood and metal in symbiosis
Two product areas are particularly large at Enably. Laboratory furniture for the Swedish market and fold-out beds for hotels and hospitals in Sweden, Norway and Germany. In addition, they also manufacture specialized furnishings for hotels, among others.
The laboratory furniture is offered as a full-service solution, which is unique. From technical design to 3D visualization, production and subsequent assembly, including preparation of media, water, air and sewage. A complete solution that means that customers do not have to worry about the boundaries of responsibility between different contractors.
The experience of combining wood and metal makes Enably stand out as a specialty joinery.
- We are appreciated for our experience in combining materials, which allows us to take into account both price and material advantages. Our in-house metalworking also allows us to be more agile when it comes to changes, explains Peter.
The journey towards ISO certification
At Enably, there was no previous in-house experience of achieving ISO certification and they needed help understanding all the elements required to become certifiable.
"From word and excel files everywhere, to ONE unified platform"
- We already had separate management systems in our companies that needed to be integrated and felt that we needed external help. After procurement and proper evaluation, the choice fell on AM System as a digital platform and Envima for project management of the integration of the management systems and guidance towards the actual certification. We have a defined three-year plan and they have provided us with knowledge, acted as the main project manager and pushed us to keep the schedule.
AM System started to bring it all together
The work of revising the management system could thus kick off and they started in the Document module to document the right things, in the right place. Peter had worked with AM System's Case module before and supplemented with prioritized case flows.
- During the evaluation, we stuck to different things with different suppliers and when we summed everything up, AM System matched us best. It is the combination of Document and Case that is so complete, says Peter.
Today, Enably has gathered all governing documentation in AM System. Peter built up case flows early on to handle risk observations, fault reports on property and machinery, and internal and external deviations. This is also where all agreements from suppliers and all safety rounds carried out by safety representatives are managed.
Through clear forms and flows, Enably gets control of all its various cases.
Positive user experience
The staff started using the system already a few months after its introduction, and before this summer's audit, there was a thorough review with the staff
"The certification audit went very well. Only three minor discrepancies, which we will extinguish right after the holidays."
- The user experience is positive with intuitive and logical navigation. The case module is powerful and easy to work with and I also appreciate the simplicity of drawing up all our processes.
The greatest use is among officials who are involved in documentation, processes and analyzing results. While production uses AM System for its SOP (standard operating procedure), self-monitoring, safety rounds and to record risk observations that were previously made on paper. These are now digital and accessible via QR codes that production staff can scan and record, via their mobile.
Other uses include customer satisfaction measurement, which is also built into Case and made available via a public link to all customers. And then there's the HR area, which Peter has recently started working on. The aim here is to create flows for employee interviews, introductions for new employees and off-boarding when an employee leaves.
Better in several stages
Enably entered the certification project with the aim of raising quality and becoming more competitive.
- This summer's certification audit went very well. Only three minor deviations, which we will extinguish immediately after the holidays. Overall, we see that the work has reduced our search times and made us more efficient. Previously, we had a lot scattered in word and excel files, a bit everywhere. Now everyone knows that it is here, in AM System, that everything is gathered and they can access relevant information in one place, says Peter and continues:
- The most obvious effect is that we have also visualized our processes and had many good discussions about where different activities are done best and most efficiently. When you draw up all the steps in a process in AM System, it becomes clear where shortcomings can occur. The handover processes between, for example, sales - preparation - production have become clearer and we have adjusted responsibilities and moved some steps where they fit better.Enably's preparation process, visualized directly in AM System
AM System's three biggest advantages, according to Peter
- The whole created in the combination of Document and Case
- The Case module is a favorite. So easy to use and so powerful
- Web-based, intuitive and accessible to everyone
The digital journey continues
At Enably, the work on digitalization continues. Their investment in technical design of laboratory furnishings has come a long way and the goal is that one and the same 3D drawing should be guiding and instructive all the way from sales to final assembly.
- We have something really good going on here. That the architect from the start can get an experience of space and flow through a 3D visualization that allows misjudgments to be avoided. And that we can then reuse that visualization for the customer, preparation, production and assembly. This would result in a 100% digital journey, which is efficient and sustainable in several stages, concludes Peter.
Areas of use
Visualization of all processes, governing documentation, case flows for supplier assessments, fault reports on machines and properties, contract registers, internal and external deviations, customer satisfaction measurement, safety rounds and risk observations.
Impacts & results
- Certification in 9001 and 14001 increases our competitiveness
- Less time is spent searching for information, making us more efficient
- Processes have been visualized and it becomes clear where improvements can be made
- Better dialogues internally as we get a common understanding of how we can work more efficiently
Facts about Enably
- Location: Sävar, Umeå in Västerbotten
- Product range: Special joinery with laboratory furniture, fold-out beds and special furniture
READ MORE
Related case studies
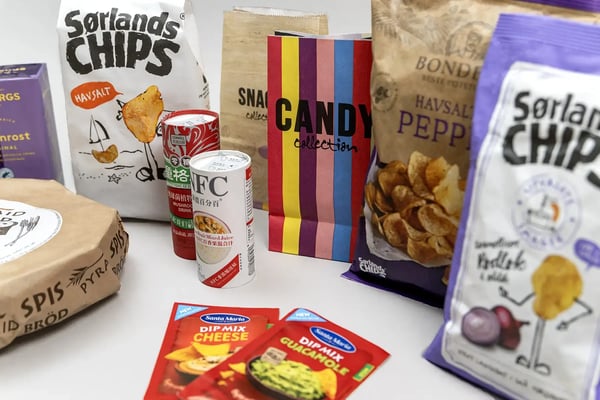
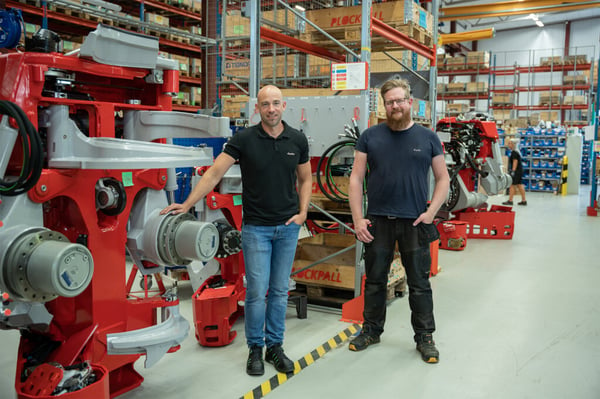
Case Studies
Log Max harvests success worldwide – chose AM System for their entire quality management system.
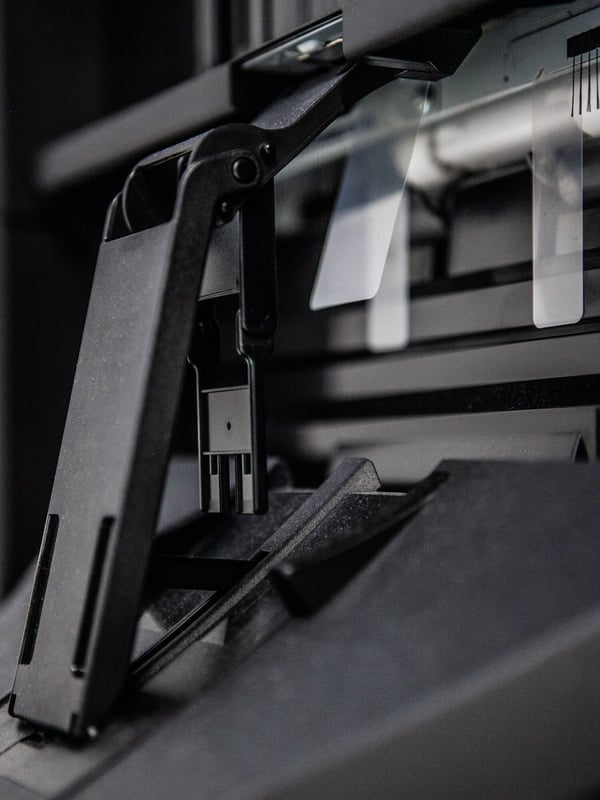
Case Studies
Matthews Marking System brought new life to it's QMS System
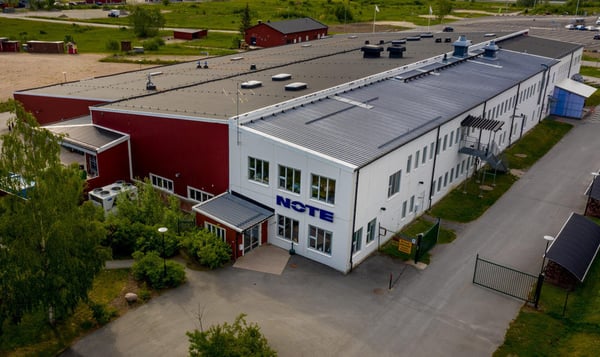
Case Studies
How NOTE ensures efficiency and ISO compliance with AM System
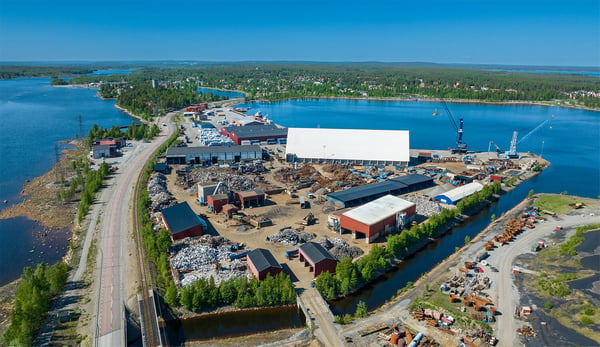
Case Studies
How Kuusakoski built a dynamic quality management system with employee engagement
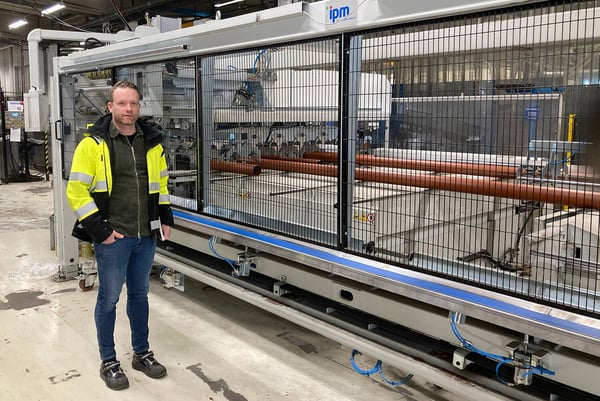
Case Studies
Pipelife saves money and time with AM System
Request a demo
Ready to make work easier and more enjoyable?
Want to see firsthand how AM System can make a difference for you? Request a demo and discover just how easy it is to create structure, efficiency, and seamless workflows in your daily operations.
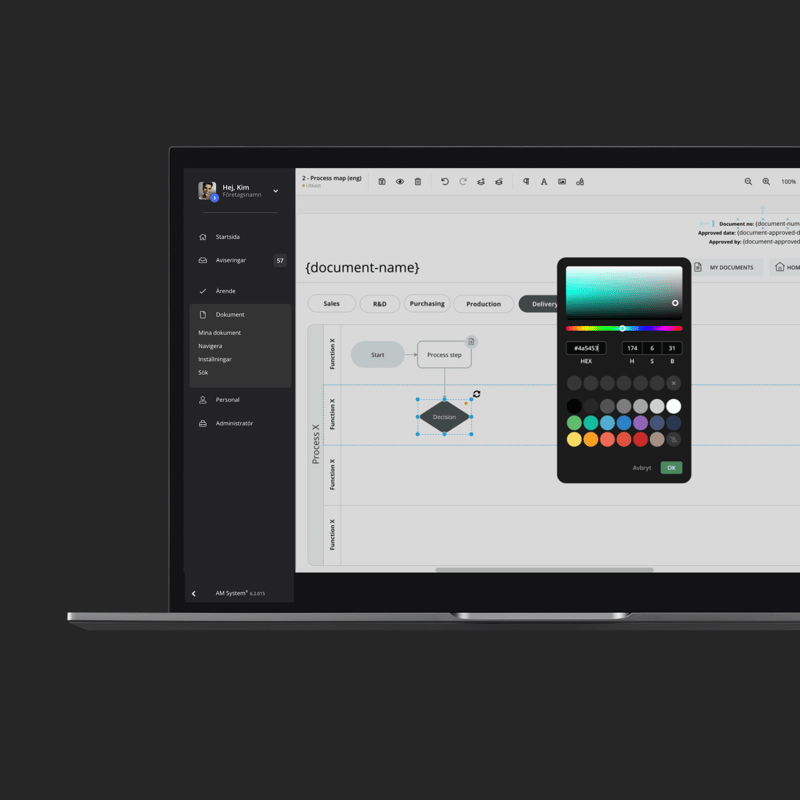