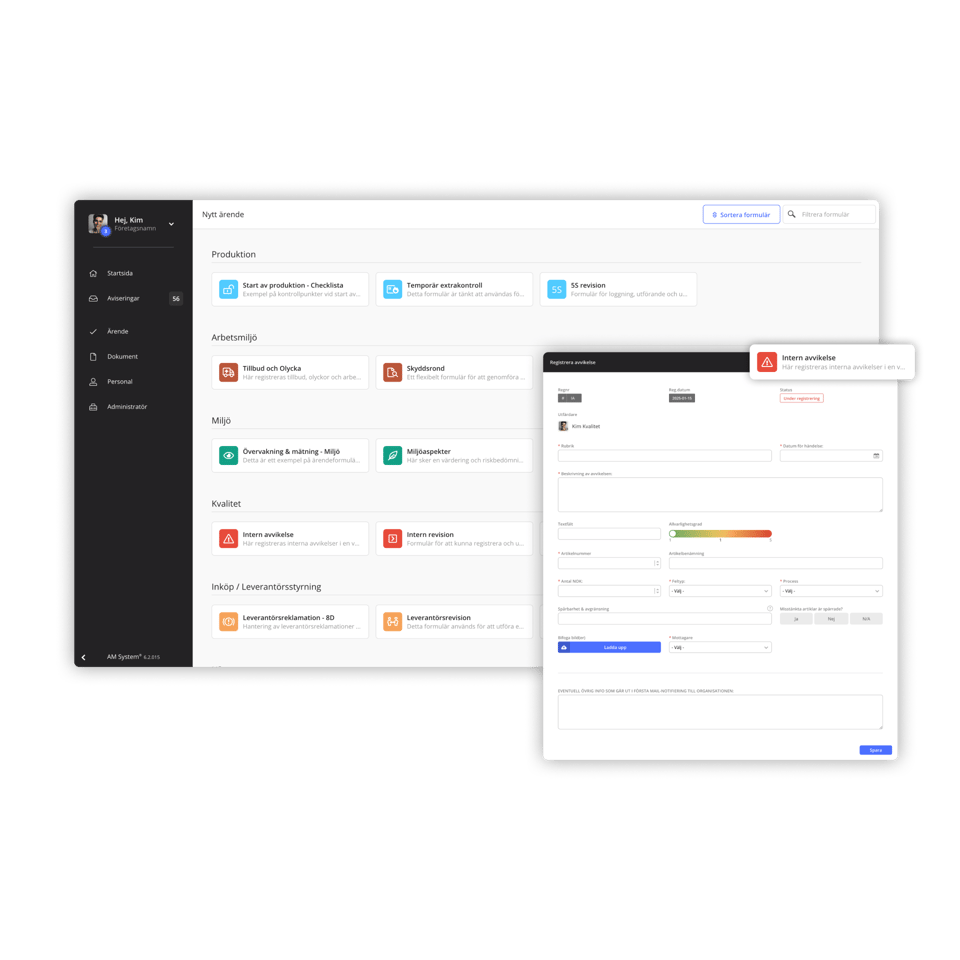
Equip employees with the right tools to empower engagement
Employees’ insights and ideas are often the most valuable assets in continuous improvement. Those working closest to processes have a unique understanding of inefficiencies and potential enhancements. AM System makes it easy for employees to contribute by:
- Reporting issues and ideas in real time: The case management feature allows employees to quickly submit improvement suggestions or highlight inefficiencies, ensuring that no idea is overlooked.
- Providing structure and visibility: Improvement initiatives can be categorized, prioritized, and assigned to the right people, creating a clear roadmap for ongoing projects.
- Encouraging accountability: Employees see that their suggestions are taken seriously, fostering engagement and ownership over improvements.